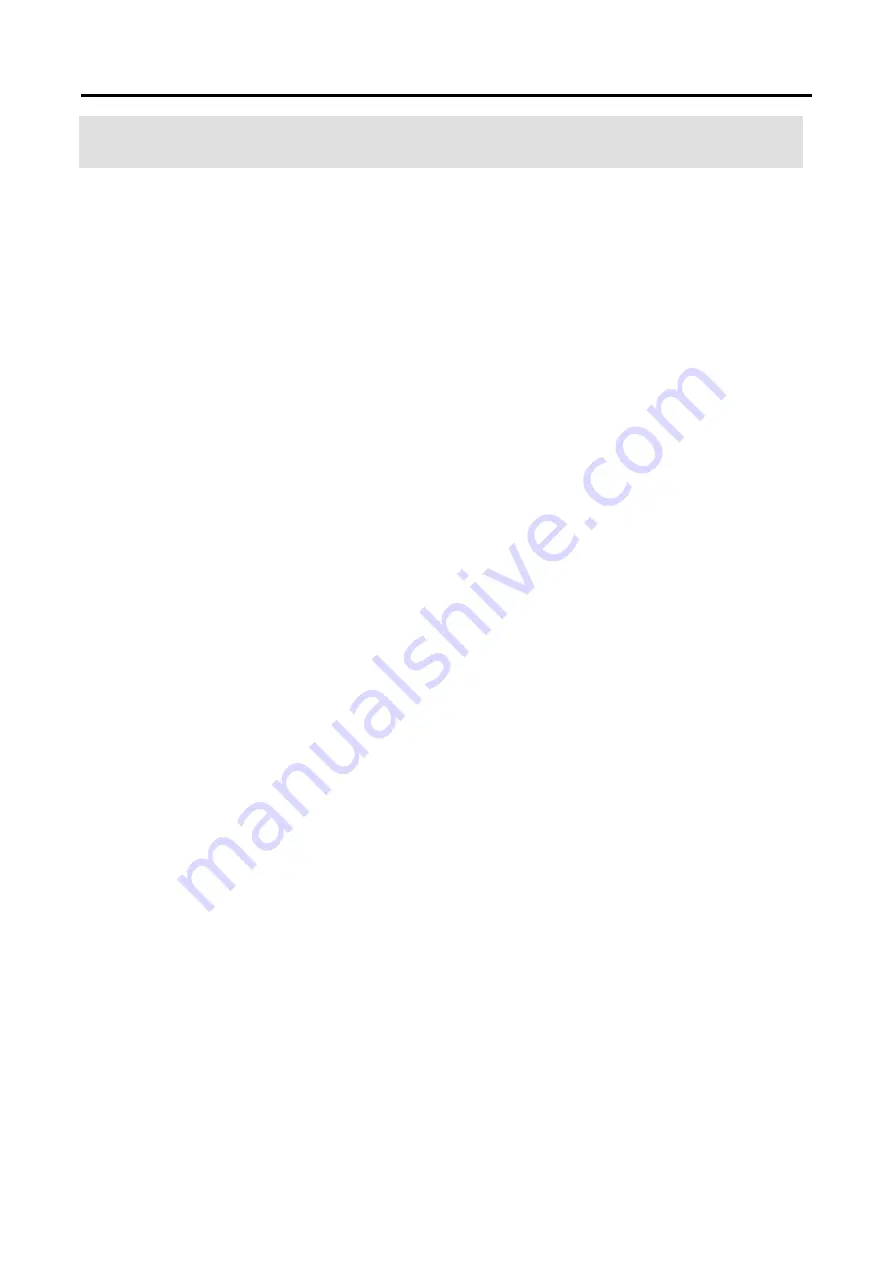
6. Servo Tuning
6-29
6.8 Vibration suppression function
6.8.1 Model following vibration suppression control
When you use the servo motor to drive tables on a machine stand, the stand itself may vibrate as
a reciprocal reactor of the motor.
When the machine stand vibrates, the vibration may cause a reaction with the Positioning
stabilizing time of the table working on the stand.
Model following vibration suppression control suppresses this type of machine stand vibration
and improves Position stabilization time and response.
■
How to use
First, select “01: Model1 model following control” at the system parameter ID07
"Position control selection”, and then perform auto-tuning to adjust the machine to
optimum servo gain. Refer to "6.3.6 Adjustment method for auto-tuning" for instructions
on tuning.
When servo gain tuning is completed, switch Group0 ID00 “Tuning mode” to “02:
ManualTun manual tuning“ after performing auto tuning result saving function.
Set “02: Model2 model following vibration suppression control” at the "Position control
selection”, and then set mechanical anti-resonance frequency and resonance frequency.
When anti-resonance frequency and resonance frequency are already known, set the
values. If anti-resonance frequency and resonance frequency are not known, you can
set by measuring anti-resonance frequency and resonance frequency by system
analysis.
When you measure the anti-resonance and resonance frequencies using System
analysis, set the "Frequency range selection" in the low range. If you set the range in
a high range, the ant-resonance and resonance frequencies in suppressible ranges
created by the Model following vibration suppression control may not be measured.
1 - 125Hz for "Frequency range selection" is recommended.
(For use of the system analysis, see "10.3 System analysis" in another document:
M0010842.)
When the mass of the servo motor is smaller than the machine stand mass, the
anti-resonance and resonance frequencies may not be measured in system analysis.
And, system analysis cannot use during tandem operation. In this case, obtain the
vibration frequency (Model anti-resonance frequency) by calculating the machine
vibration period of the vibrating point at positioning and its reciprocal and set the
model resonance frequency 1.05-1.2 times the anti-resonance frequency.
Set value of Group1 ID12 "Velocity Loop Proportional Gain 1 [KVP1]" as high as
possible within the range that mechanical system can stably work without any
oscillation. If vibration occurs, lower the set value.
Set value of Group1 ID13 "Velocity Loop Integral Time Constant 1 [TVI1]" by referring to
“TVI1 [ms] = 1000/KVP1 [Hz]”, as a rough indication.
Set value of Group1 ID02 "Position Loop Proportional Gain 1 [KP1] by referring to “KP1
[1/s] = KVP1 [Hz]/ 4
・
2
π
”, as a rough indication.
Set value of Group3 ID00 "Model Control Gain 1 [KM1]" by referring to “KM1
≒
KP1”,
as a rough indication.
If vibration increases, lower the value.
Summary of Contents for Sanmotion R 3E S
Page 1: ...M0010630G For Rotary Motor Instruction Manual Analog Pulse Input Type ...
Page 2: ......
Page 76: ...No Text on This Page ...
Page 88: ...No Text on This Page ...
Page 266: ...No Text on This Page ...
Page 332: ...No Text on This Page ...
Page 408: ...No Text on This Page ...
Page 444: ...No Text on This Page ...
Page 511: ...12 7 Optional parts dimensions 12 65 12 Appendix REGIST 1000W Wiring diagram ...
Page 512: ...No Text on This Page ...