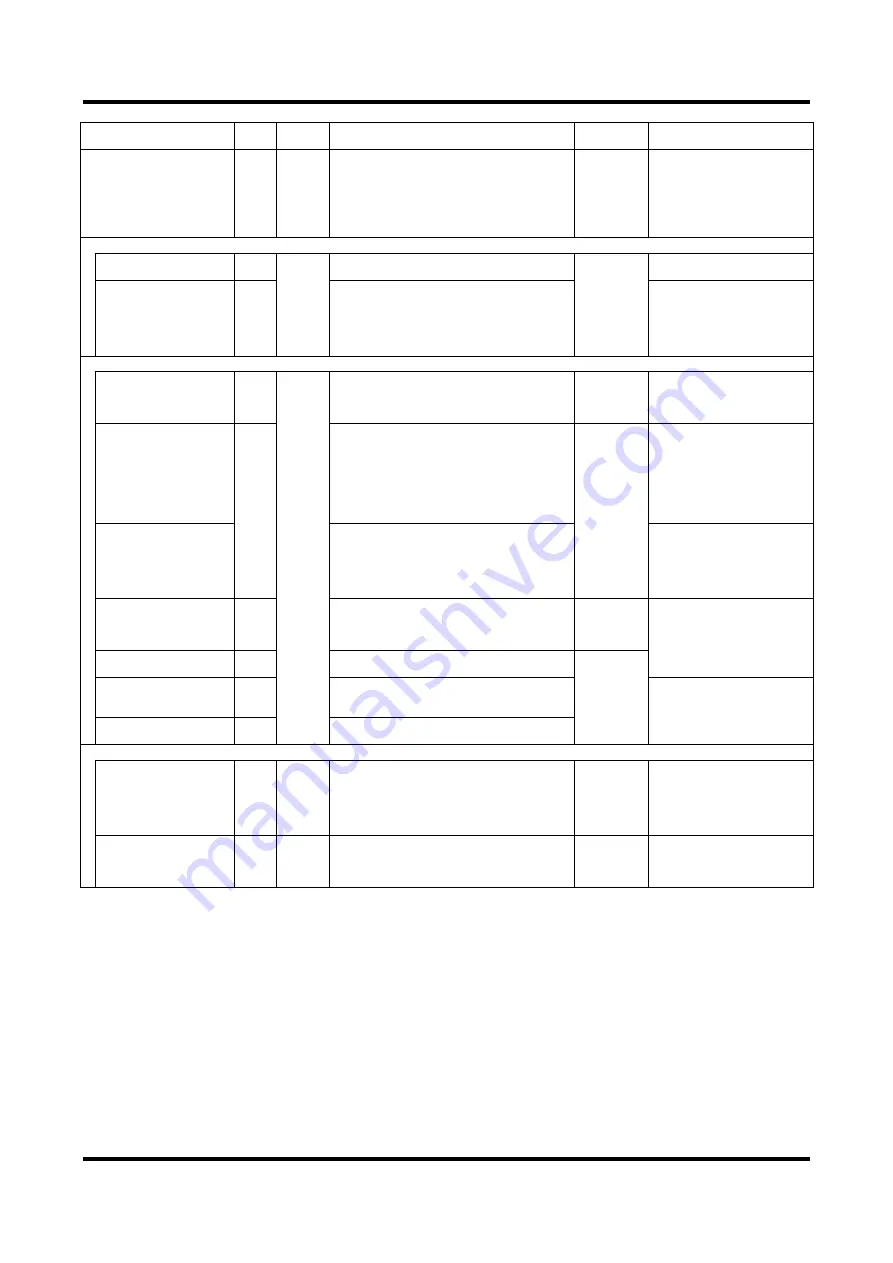
Appendix 3-3
TI71M01D06-01EN 3rd Edition: 2012.12.01
Name
Error
code
Recovery
Cause and condition detected
Action taken
at occurrence
Countermeasure
Monitor pulse error
18.0
Not
possible
Attempted to generate a pulse of 3MHz or more,
which exceeded an allowable monitor pulse output.
The motor overran.
Resonating and hunting.
Error setup
register 2
dependent,
bits 11 to 8
Check the wiring of the motor
cable and encoder cable.
Take an action against
resonance, and set an
appropriate adjustment value.
Set the scaling data to an
appropriate value.
Tandem error
Slave drive error
19.1
Possible
The master has detected an error in the slave.
Error setup
register 1
dependent,
bits 11 to 8
Remove the cause of the
abnormality on the slave side.
Tandem communication
error
19.2
Tandem communication abnormality has occurred
due to noise.
Check the connection status
of the communication cable.
Anti-noise in the
communication cable.
Remov the cause of the
noise.
Power module error
Over-voltage
20.1
Possible
Over-voltage level
main line voltage value
Servo OFF
Regeneration
error output
Check the main power supply
voltage level.
Verify that the motor is not
rotated by an external force.
IPM
fault
20.2
Temperature: 150
C or more
Control current: 12.5V or less
Over-current:
27A or more at 500W, 5
s
54A or more at 2kW, 5
s
Output short-circuited
With 1msec chattering process
Servo OFF
High ambient temperature
and high current duty
The GND of the motor cable
is wrongly wired to one of
phase A, B or C.
Verify that the motor is not
rotated at a high velocity by
an external force.
Current transformer
detection
Detection level: 15A at 500 W, 1
s
45A at 2kW, 1
s
With 1msec chattering process
The GND of the motor cable
is wrongly wired to one of
phase A, B or C.
Verify that the motor is not
rotated at a high velocity by
an external force.
Low
voltage
20.3
Low voltage (servo OFF) level
main line voltage
value < low voltage level
Error setup
register 1
dependent,
bits 7 to 4
Check the main power supply
voltage level.
Low voltage (servo OFF
level)
20.4
Main line voltage value < low voltage (servo OFF)
level
Servo OFF
Phases A and B actual
current monitoring
20.5
Phases A and B actual current vector lengths (after
bandwidth 10 Hz filter processing) exceeded 110%
of the maximum motor current.
It is necessary to repair the
drive board.
Error monitoring amplifier
constant substrate
20.6
Error was detected on the control board amplifier
constant substrate.
Main power supply error
Main power supply error
21.0
Possible
XMPSIG output threshold: 143VAC
XMPSIG from the power module maintained the
OFF state exceeding the value set up in system
setup register 1.
Error setup
register 1
dependent,
bits 3 to 0
Check the main power supply
voltage level.
The main power supply is
momentary shut down.
Fluctuations of the main
power supply are substantial.
Main power supply errorAC
(Open-Phase or Low
Voltage)
21.1
Possible
AC Main Power was detected open-phase or low
voltage over 1 second.
Error setup
register 1
dependent,
bits 2 to 0
Check wiring of every phase of
AC Main Power and the AC Main
Power Voltage.