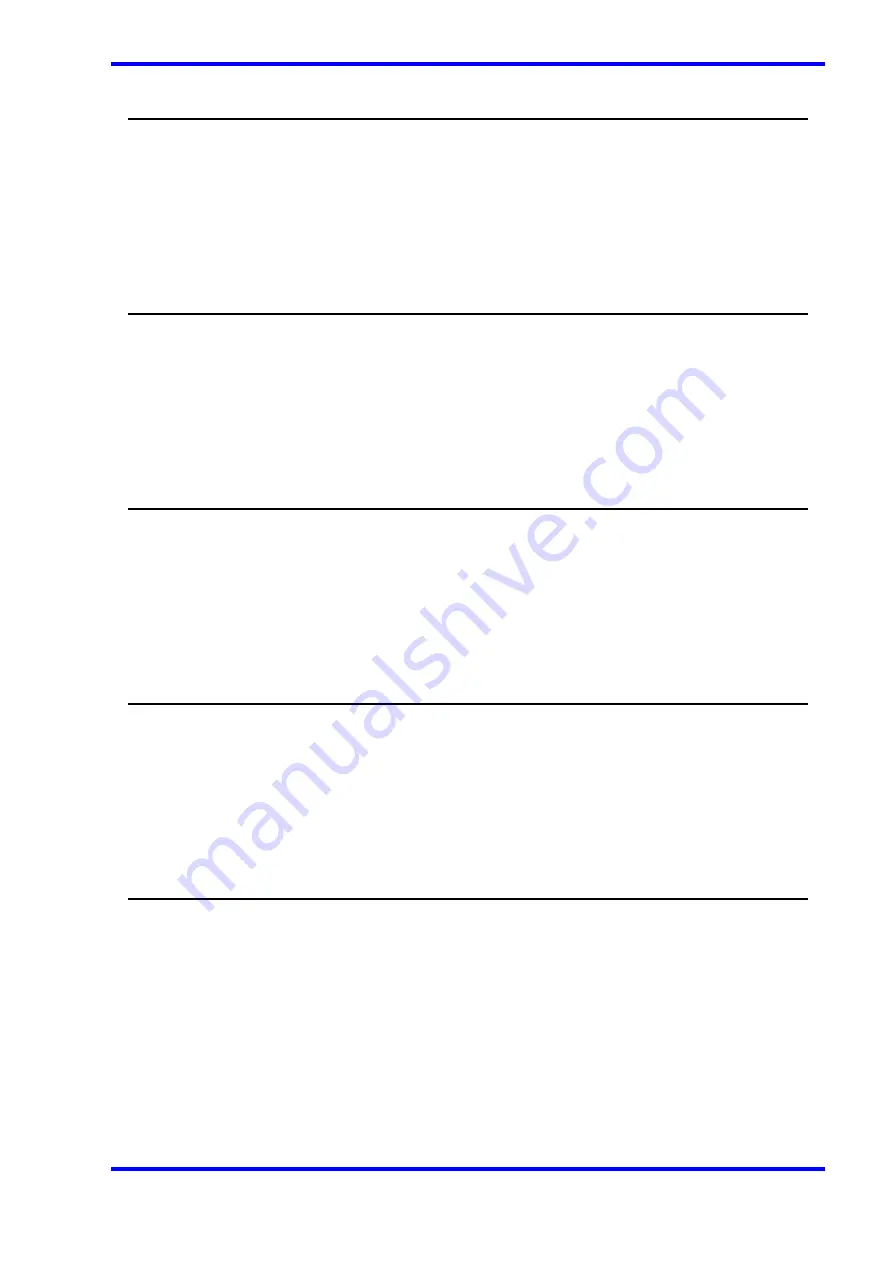
appendix1‑5
20
Frequency notch filter #1
This parameter is used for tuning against resonance.
Specifies the frequency of notch filter channel #1. Filter becomes valid by enabling Notch filter #1
through system register 2.
50
1500
depend on motor.driver type
Min:
Max:
Initial:
Unit:
Hz
Initial value: 1500Hz
Notch1Freq
Dec
21
"Q" value of notch filter #1
This parameter is used for tuning against resonance.
Specifies the 'Q' value of notch filter channel #1. Filter becomes valid by enabling Notch filter #1
through system register 2.
10
500
depend on motor.driver type
Min:
Max:
Initial:
Unit:
1/100
Initial value: 100
Notch1Q
Dec
22
Frequency notch filter #2
This parameter is used for tuning against resonance.
Specifies the frequency of notch filter channel #2. Filter becomes valid by enabling Notch filter #2
through system register 2.
50
1500
depend on motor.driver type
Min:
Max:
Initial:
Unit:
Hz
Initial value: 1500Hz
Notch2Freq
Dec
23
"Q" value notch filter #2
This parameter is used for tuning against resonance.
Specifies the 'Q' value of notch filter channel #2. Filter becomes valid by enabling Notch filter #2
through system register 2.
10
500
depend on motor.driver type
Min:
Max:
Initial:
Unit:
1/100
Initial value: 100
Notch2Q
Dec
24
First lag compensation frequency #1
This parameter is used for tuning against resonance.
Specifies the lower range frequency of the first lag compensation filter. Filter becomes valid by
enabling the first lag compensator through system register 2.
20
999
999
Min:
Max:
Initial:
Unit:
LagFreq1
Dec
TI 71M01D06‑01E 2nd Edition : 2007.01.10‑00