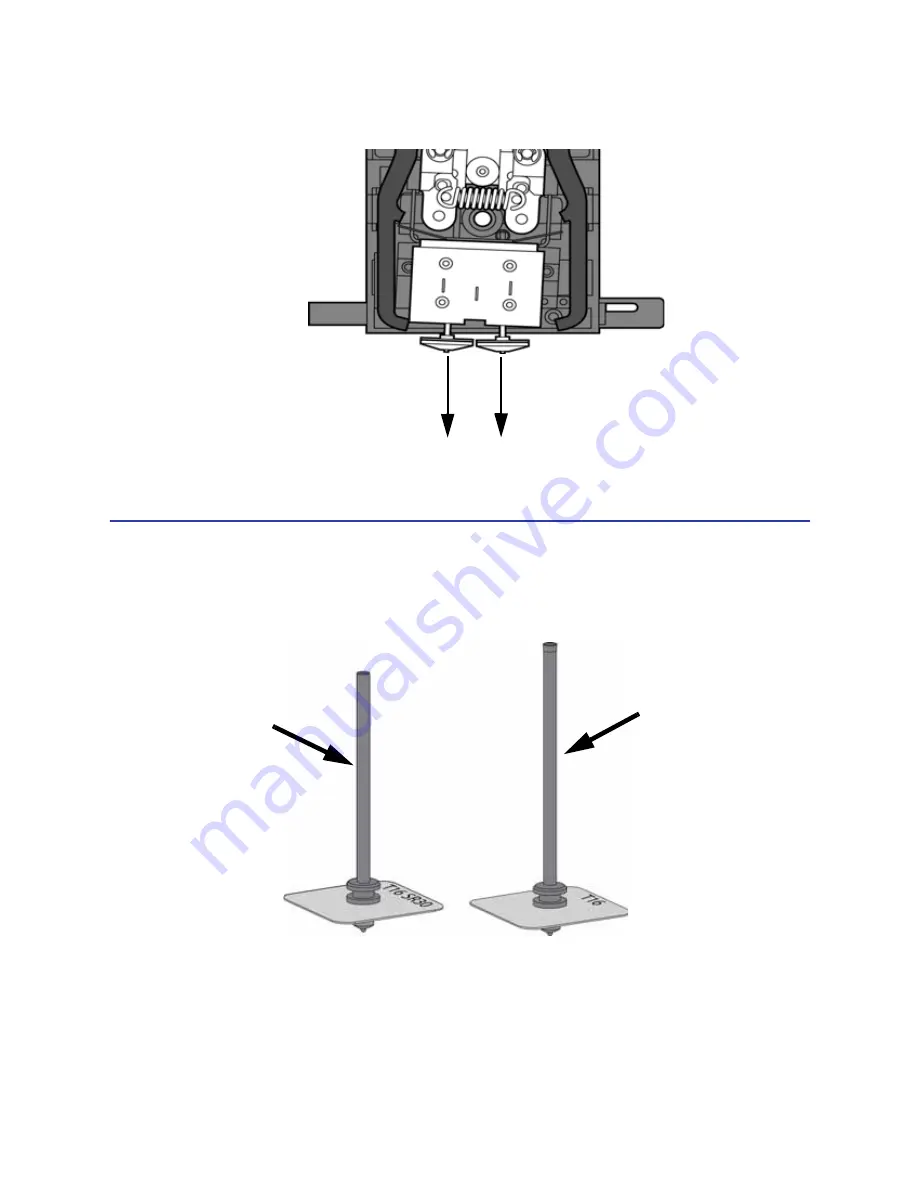
uPrint/uPrint SE Service Manual
7-11
Figure 7-411: Remove the tips
D.
Repeat for second tip if necessary.
Installing tips
1.
Place the tip shield on the tip. Be sure to install the proper tip. See
Figure 7-412: Tip shield alignment
2.
With gloved hand, insert the new tip into the heater block.
3.
Use needle nose pliers to grasp the stainless steel shield of the tip.
4.
Pull the tip shield toward you, then lift up to install the tip.
5.
Push the tip toward the back of the printer once it is all the way up against the heater
block.
Pull tips down to remove
Shorter tube
Imprinted with “T-16
SR30”
Liquefier tubes
Longer tube
Imprinted with “T16”
Summary of Contents for uPrint
Page 1: ...uPrint and uPrint Plus uPrint SE and uPrint SE Plus Service Manual Part No 209010 0001 Rev D...
Page 11: ...1 2...
Page 35: ...2 24...
Page 179: ...4 132 Figure 4 231 uPrint Plus and uPrint SE Plus measurement points and worksheet BL FL FR BR...
Page 207: ...4 160 Figure 4 275 uPrint and uPrint SE measurement points and worksheet BL FL FR BR...
Page 267: ...5 58...
Page 343: ...6 76...
Page 359: ...7 16...
Page 373: ...8 14...