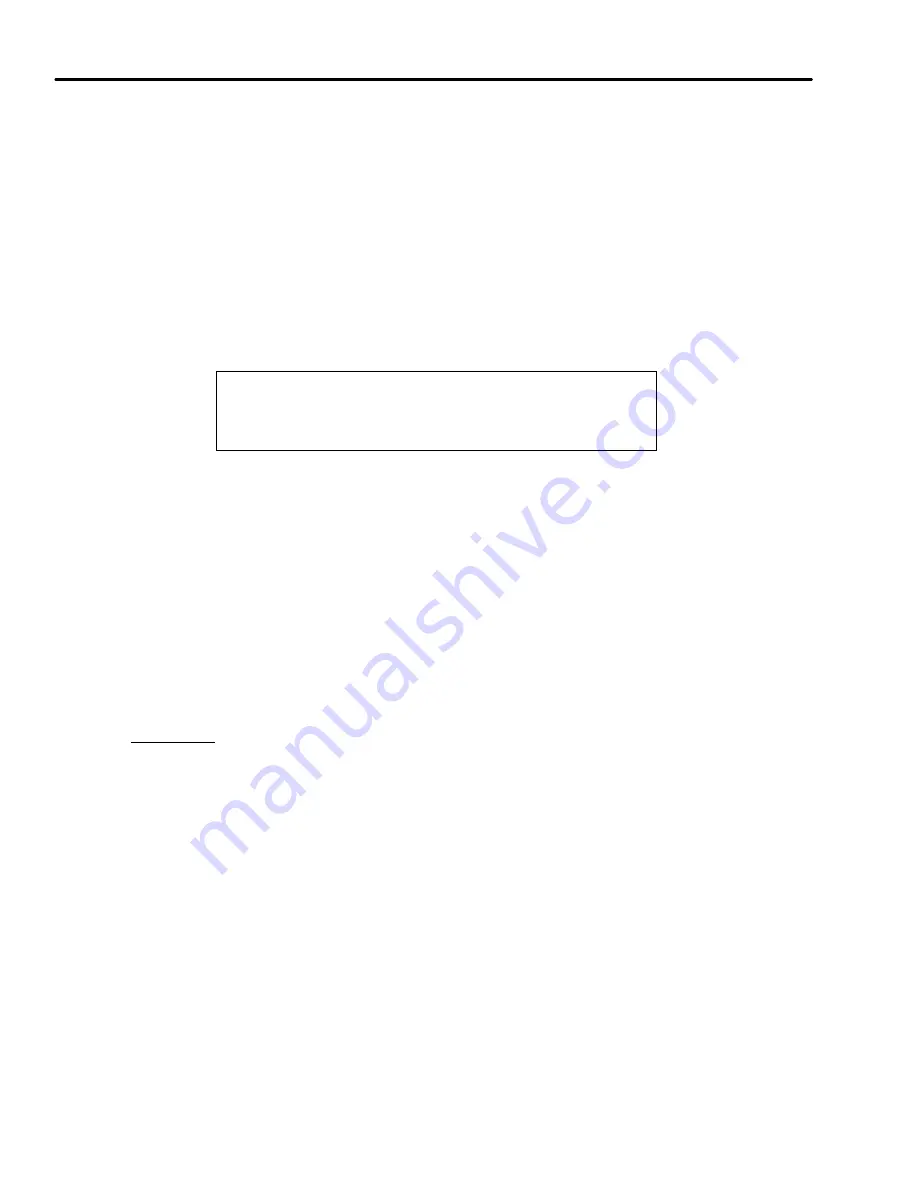
Inspection and Maintenance — GEK 107048
Major Inspection — Disassembly Procedures
MI-D-8
8. Jack the turbine case to exhaust frame flange (position 2) to 0.004
±
0.001 in. Record all dial indica-
tor readings. Recheck all jacks for snugness.
9. Jack the compressor discharge to turbine casing flange (position 3) to 0.002 –0.003 in. Record all
dial indicator readings. Recheck all jacks for snugness.
10. Jack the aft or compressor case to compressor discharge flange (position 4) to 0.002–0.003 in. Re-
cord all dial indicators. Recheck all jacks for snugness.
11. Jack the forward compressor case to aft compressor case flange (position 5 if applicable) to
0.002–0.003 in. Record all dial indicators. Recheck all jacks for snugness.
CAUTION
Do not, under any circumstances remove the mechanical
support jacks or dial indicators until all upper half casings
have been reinstalled and bolted up.
Note:
To prevent out-of-roundness occurring all casings should not be un-
bolted prior to removal. This is very tempting to do when running more
than one (1) shift operation with only one (1) shift crane coverage.
It is permissible to remove every other bolt on the horizontal joint and
every other bolt in the vertical joint except for the top six casings should
not be replaced without being bolted. Again, every other bolt on the
horizontal and vertical joint with six on top is permissible.
Casings should be removed in the following sequence; exhaust frame,
forward compressor case, inlet case, turbine case and compressor dis-
charge. Reinstallation is in the reverse order, i.e. compressor discharge
case, turbine case, etc.
Operation 8 — How to Remove Upper Half Exhaust Frame
Note:
The rail beam, trolley hoist and spreader bar are applicable to vertical
exhaust stack configurations only. On side exhaust stack configura-
tions the cowl cover on the exhaust plenum is removed for access to the
exhaust frame for removal using an overhead crane and normal
rigging.
1. Install the rail beam, trolley hoist, and spreader bar used for exhaust frame and turbine casing re-
moval inside the exhaust duct transition piece.
2. Disconnect and remove as necessary all instrumentation tubing for wheelspace thermocouples and
pressures inside the inner barrel tunnel.
3. Remove the left and right side outer horizontal joint insulating packs and identify for location.
4. Remove the outer insulating pack on the upper half aft vertical flange.
5. Remove the upper half vertical bolting between turbine case and exhaust frame.
Summary of Contents for MS6001B
Page 2: ...Gas Turbine Inspection and Maintenance GEK 107048 I 2 THIS PAGE INTENTIONALLY LEFT BLANK ...
Page 4: ...Inspection and Maintenance Note THIS PAGE INTENTIONALLY LEFT BLANK ...
Page 13: ...INSERT TAB INTRODUCTION ...
Page 14: ......
Page 25: ...INSERT TAB STANDARD PRACTICES ...
Page 26: ......
Page 87: ...INSERT TAB AUXILIARY CONTROLS SYSTEMS MAINTENANCE ...
Page 88: ......
Page 133: ...INSERT TAB SCHEDULED TURBINE MAINTENACE ...
Page 134: ......
Page 157: ...INSERT TAB COMBUSTION INSPECTION ...
Page 158: ......
Page 239: ...INSERT TAB HOT GAS PATH INSPECTION ...
Page 240: ......
Page 313: ...INSERT TAB MAJOR INSPECTION ...
Page 314: ......
Page 316: ...Inspection and Maintenance GEK 107048 Major Inspection 2 THIS PAGE INTENTIONALLY LEFT BLANK ...
Page 363: ...INSERT TAB MAINTENANCE FORMS ...
Page 364: ......