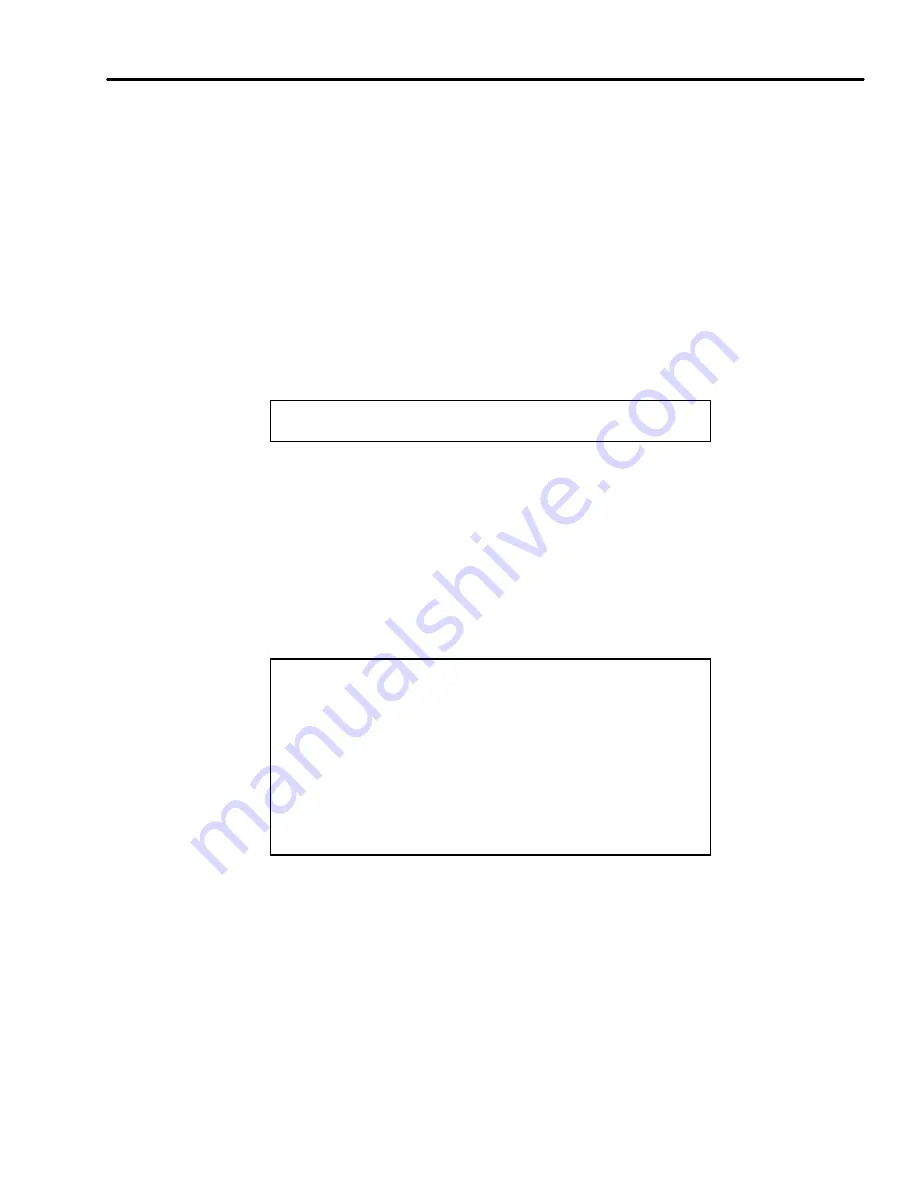
Hot Gas Path Inspection — Inspection Procedures
Inspection and Maintenance — GEK 107048
HGP-I-7
All records and questions arising on the subject should be communicated to your General Electric
Company Field Service Representative.
Bucket deterioration may be classified as cracks, dents, missing metal, and corrosion. Visually
inspect the turbine buckets for these abnormalities. See Figure HGP-I.9 for first stage bucket de-
tails, Figure HGP-I.10 for second and third stage bucket details.
Note:
1. It is recommended that bucket rework be done by qualified General
Electric Company Personnel.
2. In all cases, the bucket rework area must be cleaned and fluorescent
penetrant inspected with ZL-22A, or equivalent when rework is
completed.
CAUTION
Do not attempt to clean buckets prior to inspection.
2. Visually inspect the vane section, platform and dovetail areas, using a ten power (10X) glass ex-
amine the critical area of vane section (root fillets, top 25% of tip including squealer tips and
shrouds, and trailing edges). Any suspected cracks should be locally cleaned using aluminum ox-
ide 220 or 240 grit paper and hand clean to prepare the surface area for fluorescent penetrant test-
ing. Surface temperatures during polishing operations should not exceed 100 degrees Fahrenheit
or ambient temperature whichever is greater. High temperature will cause metal to yield and flow
covering defects so that they cannot be detected.
CAUTION
All first stage buckets have a corrosion resistant protective
coating. This coating is only 0.002 in. thick and extreme
care must be taken to avoid damaging this coating when
cleaning, repairing or handling these buckets. Coated
buckets must be cleaned with aluminum oxide 240 grit at
an operating pressure of not more than 40 psi. Reworking
of coated buckets is allowed, but the rework should be
held to a minimum so that no more coating is removed
than is absolutely necessary to effect the repair.
First Stage Buckets
1. Cracks — Cracks on first stage buckets are unacceptable with one exception: radial cracks on the
bucket squealer tip less than 0.2 in. long are permissible. These cracks usually occur as a result
of Foreign Object Damage (F.O.D.). Crack detection requires the use of fluorescent penetrant on
buckets. Zyglo ZL-22A penetrant is desirable because it will detect tight cracks which red dye type
penetrant cannot detect. Radial cracks in certain areas of the squealer tip may be remedied by re-
moving material. The limits are covered in paragraph 3 Missing Metal.
Summary of Contents for MS6001B
Page 2: ...Gas Turbine Inspection and Maintenance GEK 107048 I 2 THIS PAGE INTENTIONALLY LEFT BLANK ...
Page 4: ...Inspection and Maintenance Note THIS PAGE INTENTIONALLY LEFT BLANK ...
Page 13: ...INSERT TAB INTRODUCTION ...
Page 14: ......
Page 25: ...INSERT TAB STANDARD PRACTICES ...
Page 26: ......
Page 87: ...INSERT TAB AUXILIARY CONTROLS SYSTEMS MAINTENANCE ...
Page 88: ......
Page 133: ...INSERT TAB SCHEDULED TURBINE MAINTENACE ...
Page 134: ......
Page 157: ...INSERT TAB COMBUSTION INSPECTION ...
Page 158: ......
Page 239: ...INSERT TAB HOT GAS PATH INSPECTION ...
Page 240: ......
Page 313: ...INSERT TAB MAJOR INSPECTION ...
Page 314: ......
Page 316: ...Inspection and Maintenance GEK 107048 Major Inspection 2 THIS PAGE INTENTIONALLY LEFT BLANK ...
Page 363: ...INSERT TAB MAINTENANCE FORMS ...
Page 364: ......