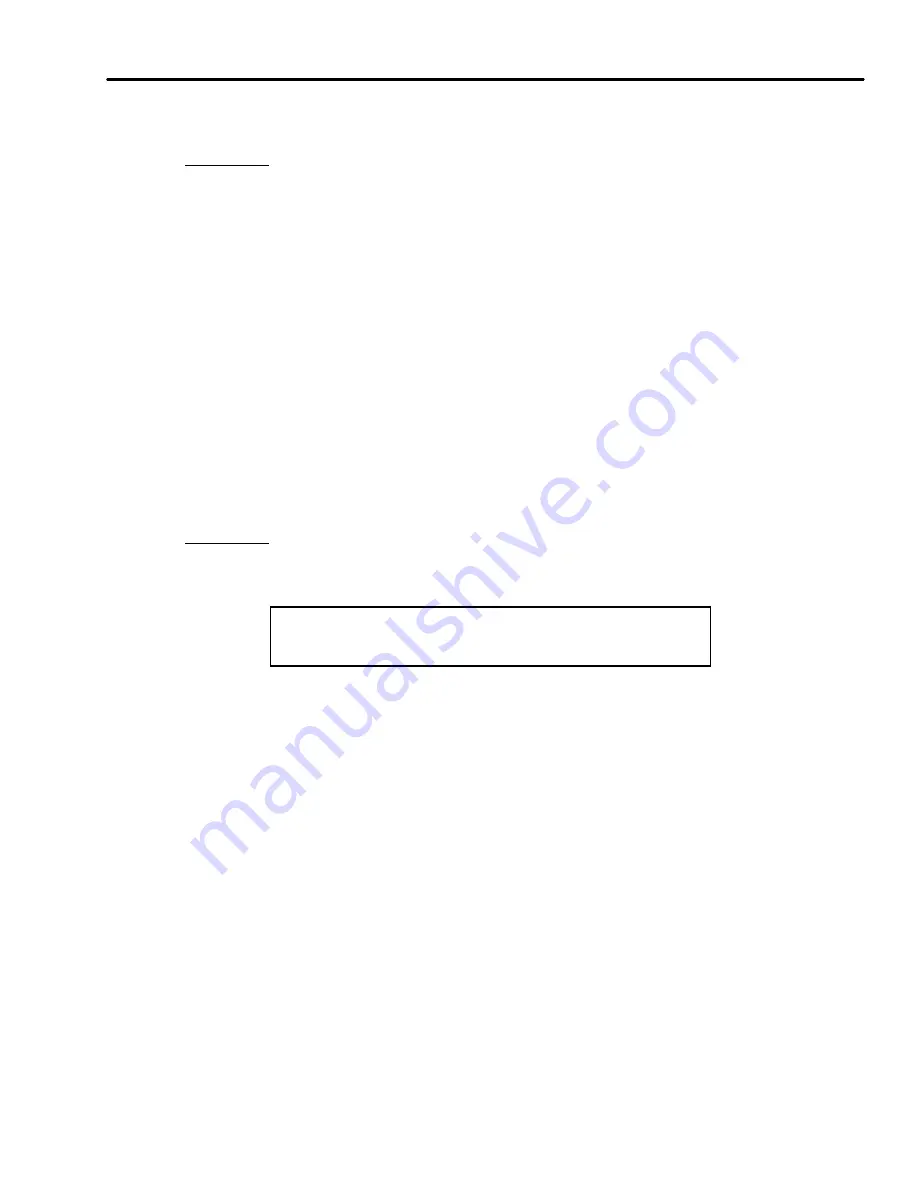
Combustion Inspection — Reassembly Procedures
Inspection and Maintenance — GEK 107048
CI-R-1
III. Reassembly Procedures For MS-6001B DLN-1 Combustion Systems
Operation 1 — How to Perform Transition Piece Preassembly Inspections and Checks
1. Prior to installation, inspect transition pieces for obvious handling or transportation damage; such
as deformed floating seals and pinched end seal slots and damaged inner brackets. Trial fit end
seals into transition piece end seal slots before installing transition piece into the unit.
2. Trial fit each support clamp (bullhorn) to its respective transition piece prior to installing into the
unit.
3. Check first stage nozzle segments for axial displacement (steps) between adjoining segments.
Displacement greater than 0.030 in. should be reseated with a 5 pound rawhide or nylon mallet.
Do not use metal hammer.
4. Check to insure that the first stage nozzle seal slots are free from damage such as nicks, burrs or
any other faults which would interfere with the proper assembly of the transition piece floating
seals to the first stage nozzle.
5. Check all helicoils for cross threading, elongation, stripping or insert backing out. Remove and
replace all damaged helicoils.
Operation 2 — How to Install Transition Pieces
CAUTION
Use new bolts and lockplates. Do not reuse hardware pre-
viously removed.
1. Install the transition piece guide pin, if removed, into the center mounting hole of the first-stage
nozzle retaining ring in the number five (5) position. See Figure CI-R.1.
Note:
The last transition piece to be installed can be in the 1, 9 or 10 location
dependent on which turbine casing access port was used at disassembly.
Install the transition pieces starting with number 5; then install 4, 6, 7,
3, 2, 8, 1, 9 and 10 last or as stated above number 1 or 9 last.
2. Slide number five (5) transition piece over the guide pin to support the transition piece. Insert the
floating seals into their respective slots in the first stage nozzle side wall. Prior to installation of
all bolts, lubricate threads with Fel Pro C-102. Assemble the support clamp to the transition piece
forward mounting bracket slots. Install the support clamp lockplates and bolts. Bolt the support
clamp to the compressor discharge casing. Do not tighten bolts or bend lockplates at this time.
See Figure CI-R.2.
3. Install the aft bracket bolts and lockplates and tighten to the first stage nozzle retaining ring. Prior
to torquing the bolts, check for proper floating seal engagement to the first stage nozzle slots.
Torquing aft bracket bolts with floating seal out of its slot will result in damage to seal. Torque
aft bracket bolts to 75–85 lb. ft. Do not bend lockplate tabs at this time.
Summary of Contents for MS6001B
Page 2: ...Gas Turbine Inspection and Maintenance GEK 107048 I 2 THIS PAGE INTENTIONALLY LEFT BLANK ...
Page 4: ...Inspection and Maintenance Note THIS PAGE INTENTIONALLY LEFT BLANK ...
Page 13: ...INSERT TAB INTRODUCTION ...
Page 14: ......
Page 25: ...INSERT TAB STANDARD PRACTICES ...
Page 26: ......
Page 87: ...INSERT TAB AUXILIARY CONTROLS SYSTEMS MAINTENANCE ...
Page 88: ......
Page 133: ...INSERT TAB SCHEDULED TURBINE MAINTENACE ...
Page 134: ......
Page 157: ...INSERT TAB COMBUSTION INSPECTION ...
Page 158: ......
Page 239: ...INSERT TAB HOT GAS PATH INSPECTION ...
Page 240: ......
Page 313: ...INSERT TAB MAJOR INSPECTION ...
Page 314: ......
Page 316: ...Inspection and Maintenance GEK 107048 Major Inspection 2 THIS PAGE INTENTIONALLY LEFT BLANK ...
Page 363: ...INSERT TAB MAINTENANCE FORMS ...
Page 364: ......