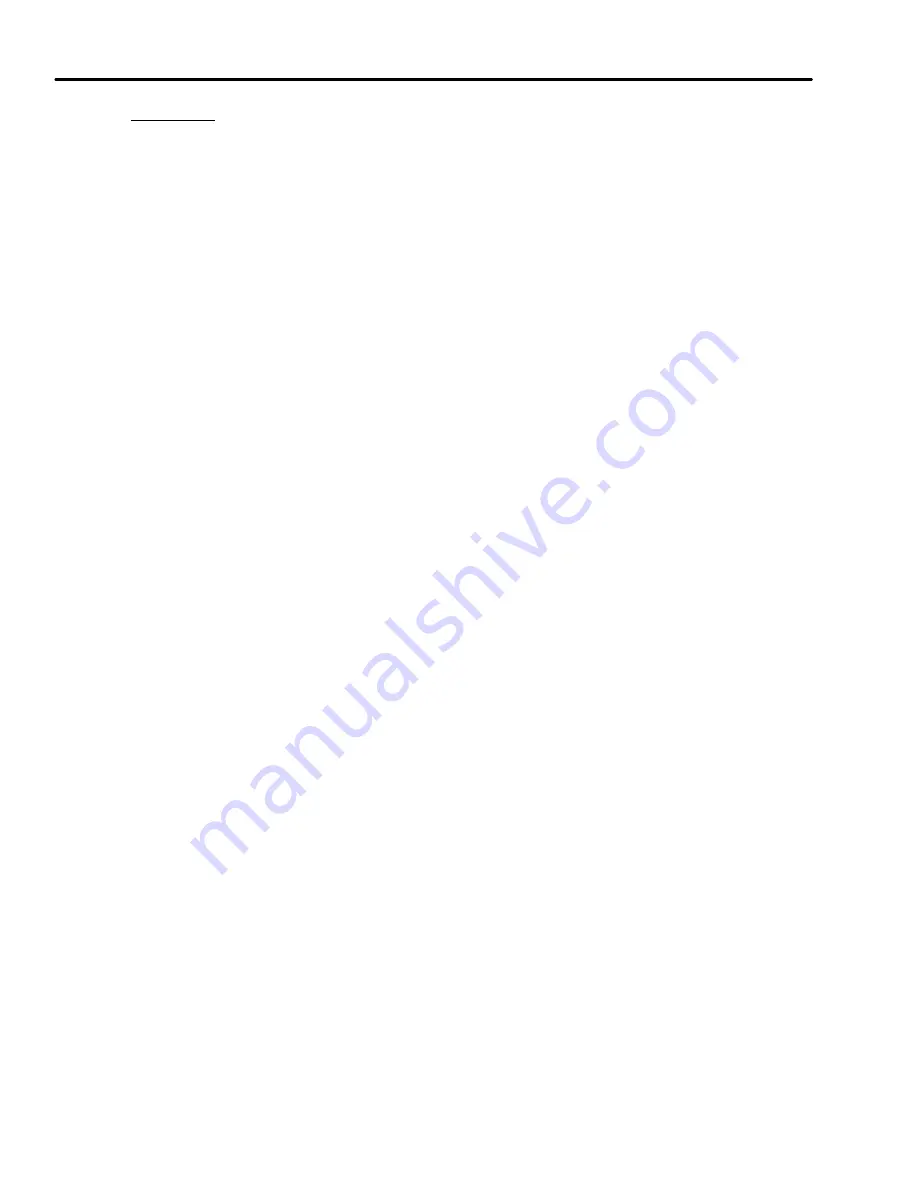
Inspection and Maintenance — GEK 107048
Major Inspection — Disassembly Procedures
MI-D-6
Operation 7 — How to Place Mechanical Support Jacks Under Unit Casings and Inlet Bellmouth
Note:
The base floorplate underneath the compressor and turbine flanges has
removable floorplate cutouts at each location for a mechanical support
jack.
If the base has a transaxial “I” beam, using steel shims, pack the shims
solidly beneath the I-beam and the concrete pad at each mechanical
support jack location. Place the mechanical support jacks on top of the
I-beam at each location to support the unit casing. See Figure MI-D.1.
Before removal of any top casings, screw jacks must be placed at all ver-
tical flanges as shown in Figure MI-D.1. Jacks should be located on the
machine centerline and be perpendicular to the foundation.
Dial indicators are required at each jacking location and are to be
mounted separately from the jacks.
1. Remove the turbine compartment floorplate covers provided beneath the vertical flange joints to
gain access to the concrete foundation.
2. Install a mechanical support jack at the bottom centerline flange of the forward compressor inlet
bellmouth. Snug the jack up fingertight. Setup dial indicator to read upward casing deflection and
set indicator to zero. See Figure MI-D.1 position number 1.
3. Install a mechanical support jack between the jacking platform and the concrete base located be-
neath the turbine casing to exhaust frame flange and tighten the jack to the jacking platform.
Install a second mechanical jack and dial indicator at the bottom centerline flange of turbine cas-
ing to exhaust frame on the jacking platform. Snug the jack and zero the dial indicator. See Figure
MI-D.1 position number 2.
4. Install mechanical jack and dial indicator at the bottom centerline of the compressor discharge to
turbine casing flange. Snug the jack and zero the dial indicator. See Figure MI-D.1 position num-
ber 3.
5. Install mechanical jack and dial indicator at the bottom centerline of the aft or compressor casing
to compressor discharge casing flange. Snug the jack and zero dial indicator. See Figure MI-D.1
position number 4.
6. Install mechanical jack and dial indicator at the bottom centerline of the forward compressor case
to aft compressor case flange. Snug the jack and zero the dial indicator. See Figure MI-D.1 position
number 5.
Note:
If the compressor casing is a single casing (combined forward and aft
casing) then the mechanical jack at position number 5 is not required.
7. Jack the forward inlet bell flange (position 1) to 0.006
±
0.001 in. Record all dial indicator readings
at all jacking locations. Recheck all jacks for snugness.
Note:
If upon reaching a flange to be jacked, the dial indicator reading al-
ready exceeds the value to be jacked to, then only snug the jack to the
flange and record all dial indicator readings.
Summary of Contents for MS6001B
Page 2: ...Gas Turbine Inspection and Maintenance GEK 107048 I 2 THIS PAGE INTENTIONALLY LEFT BLANK ...
Page 4: ...Inspection and Maintenance Note THIS PAGE INTENTIONALLY LEFT BLANK ...
Page 13: ...INSERT TAB INTRODUCTION ...
Page 14: ......
Page 25: ...INSERT TAB STANDARD PRACTICES ...
Page 26: ......
Page 87: ...INSERT TAB AUXILIARY CONTROLS SYSTEMS MAINTENANCE ...
Page 88: ......
Page 133: ...INSERT TAB SCHEDULED TURBINE MAINTENACE ...
Page 134: ......
Page 157: ...INSERT TAB COMBUSTION INSPECTION ...
Page 158: ......
Page 239: ...INSERT TAB HOT GAS PATH INSPECTION ...
Page 240: ......
Page 313: ...INSERT TAB MAJOR INSPECTION ...
Page 314: ......
Page 316: ...Inspection and Maintenance GEK 107048 Major Inspection 2 THIS PAGE INTENTIONALLY LEFT BLANK ...
Page 363: ...INSERT TAB MAINTENANCE FORMS ...
Page 364: ......