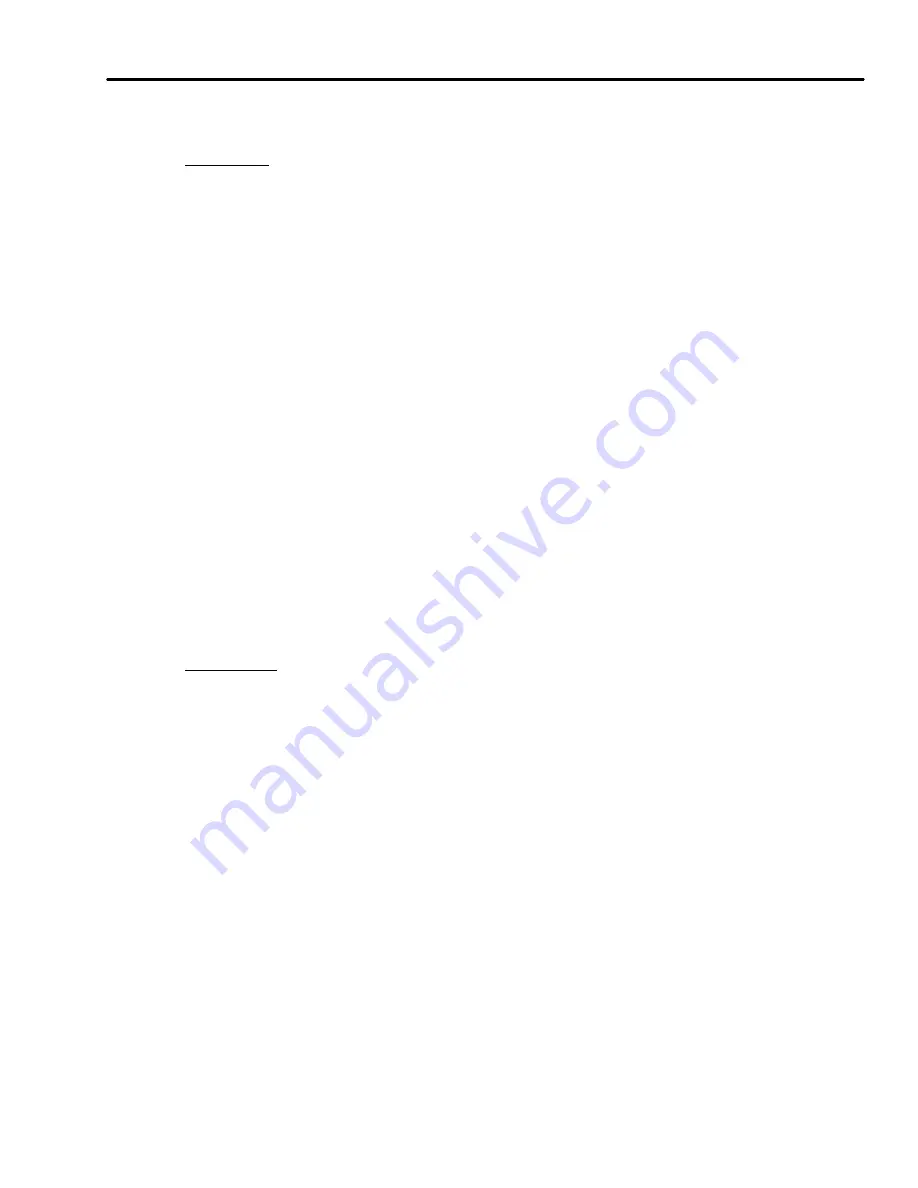
Major Inspection — Reassembly Procedures
Inspection and Maintenance — GEK 107048
MI-R-7
6. Bolt up the inlet guide vane control ring and release the lower inlet guide vane support plate bolts.
Operation 9 — How to Install Forward Compressor Casing
1. Clean and deburr mating joints.
2. Rig to lift the forward casing and install guide pins.
3. Check to insure the compressor is clean and free of all foreign matter.
4. Apply joint compound on the surface of the horizontal joints only and only for a distance of one
inch on both sides of the four way joints. Refer to the Standard Practices section for recommended
solvents, sealers, and cleaners.
5. Carefully lower the casing into position being careful not to swing the casing into the rotor or
adjacent vertical flanges. Insure no foreign objects enter the compressor during this operation.
6. Apply anti-seize compound to the vertical joint dowels and install the dowels between the inlet
and compressor casing flanges.
7. Apply anti-seize compound to the bolting, remove the guide pins and install all bolting to horizon-
tal and vertical flanges.
8. Torque the horizontal joint bolts starting at the mid point of the joint, working alternately left and
right, forward and aft, until all bolting is tight.
9. Torque all vertical joint bolts starting at the four way joint and working alternately left and right,
to top vertical centerline.
Operation 10 — How to Install Exhaust Frame
1. Assemble new gasket to the horizontal joints of the exhaust frame.
2. Using the spreader bar rig the outer upper lugs to an overhead crane, rig to lift the exhaust frame
by attaching one end of the wire rope sling to one of the lower lugs on the spreader bar and passing
the other end through the lifting lugs on the exhaust frame and attach the end to the lug on the
other side of the spreader bar. Repeat rigging hookup for the other side.
3. Apply a very light coating of anti-seize compound to the exhaust frame vertical flange. Lift the
exhaust frame and clean and deburr the joints.
4. Position the exhaust frame over the unit and move the trolley hoist to its forward stop on the rail
beam. Rig and transfer the exhaust frame to the trolley hoist.
5. Install guide pins and using the trolley hoist lower the exhaust frame into sure the exhaust cone
baffle engages its mating upper half slot.
6. Apply anti-seize compound to the bolting and install all the inner vertical and horizontal joint
bolts.
7. Install the outer horizontal joint bolting and the vertical bolting between the turbine casing and
exhaust frame.
Summary of Contents for MS6001B
Page 2: ...Gas Turbine Inspection and Maintenance GEK 107048 I 2 THIS PAGE INTENTIONALLY LEFT BLANK ...
Page 4: ...Inspection and Maintenance Note THIS PAGE INTENTIONALLY LEFT BLANK ...
Page 13: ...INSERT TAB INTRODUCTION ...
Page 14: ......
Page 25: ...INSERT TAB STANDARD PRACTICES ...
Page 26: ......
Page 87: ...INSERT TAB AUXILIARY CONTROLS SYSTEMS MAINTENANCE ...
Page 88: ......
Page 133: ...INSERT TAB SCHEDULED TURBINE MAINTENACE ...
Page 134: ......
Page 157: ...INSERT TAB COMBUSTION INSPECTION ...
Page 158: ......
Page 239: ...INSERT TAB HOT GAS PATH INSPECTION ...
Page 240: ......
Page 313: ...INSERT TAB MAJOR INSPECTION ...
Page 314: ......
Page 316: ...Inspection and Maintenance GEK 107048 Major Inspection 2 THIS PAGE INTENTIONALLY LEFT BLANK ...
Page 363: ...INSERT TAB MAINTENANCE FORMS ...
Page 364: ......