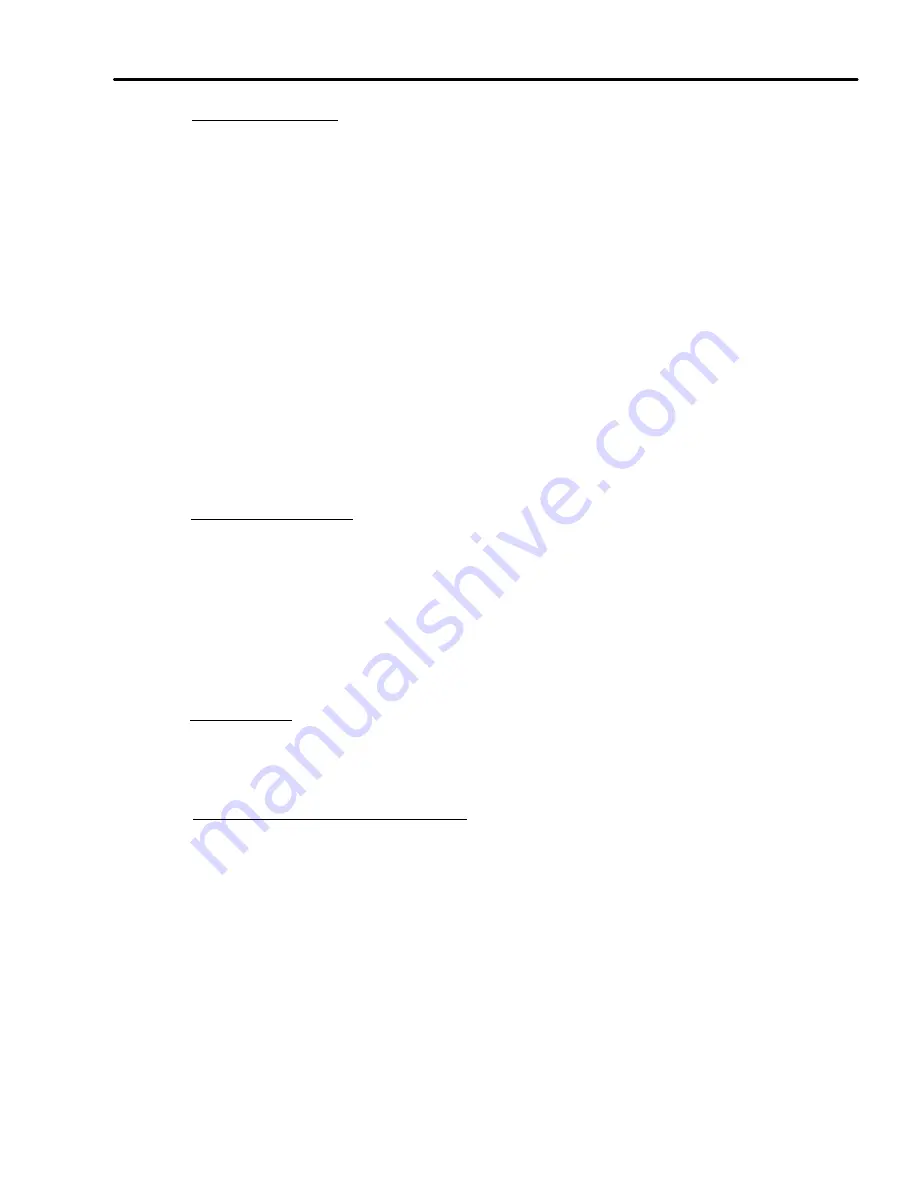
Inspection and Maintenance
Inspection and Maintenance Procedures
IMP–11
Cooling Water Pump
Check the pump for seal leakage either when running or stopped. Leakage is usually visible along the
pump shaft and/or from the drain port on the seal mounting flange. If there is unusual leakage, it is an
indication that foreign material has become lodged between the faces of the seal. This should be cor-
rected before further pump operation. If the leakage is profuse, it is an good indication that the seal is
worn and should be replaced.
Check the internal cleanliness of the mechanical seal cooling water circulating line. If this line gets
clogged, the seal can overheat and result in a pump failure. Also check the cleanliness of the abrasive
separator in the seal cooling line.
Whenever the pump is disassembled for any reason, the impeller-to-wear-ring clearance should be
checked. If the clearance exceeds twice the value recommended by the pump manufacturer, the wear
rings should be replaced and reworked to restore the manufacturer’s recommended clearance values.
This will restore pump efficiency insofar as this clearance is concerned.
Whenever the pump is disassembled, all parts of the pump, especially the impeller, shaft sleeve, and
wearing parts of the mechanical seal should be checked and replaced, if worn. Refer to the Cooling Water
System tab in the Service Manual.
False Start Drain Valve
Check for proper operation of the valve during startup and shut down. The valve should not be venting
while the turbine is operating. The valve should start to close at between 19 and 22 psig (1.34 and 1.52
bars) and fully close at between 29 and 32 psig (2.0 and 2.21 bars). Check the fuel oil and compressor
discharge piping and tubing connections for leakage of oil and air. Check the condition of the diaphragm
in the valve actuator annually and replace if worn.
FUEL GAS SYSTEM
General Notes
Fuel gas piping failures may cause a fire or explosion if an ignition source is present, or failure of the
machine to operate.
Fuel Gas Stop Ratio and Control Valve
Check for excessive gas leakage at the valve stems, packing leakoff and vent lines.
If it is suspected that the valve leaks, check the seating surfaces for damage or foreign material. Contact
between the valve and seat must be checked with the stem in place. Check the rod seals and wipers of
the hydraulic cylinders for leakage and replace them if worn. Check the gas precharge pressure of the
accumulator and correct it if required.
Check the trip relay for cleanliness and freedom of operation. A small amount of dirt can cause the relay
to stick. Disassemble and clean if necessary.
If the movable core on the LVDT (on the control and stop valve) appears to be misaligned with the sta-
tionary coil and is rubbing the coil, realign it.
Summary of Contents for MS6001B
Page 2: ...Gas Turbine Inspection and Maintenance GEK 107048 I 2 THIS PAGE INTENTIONALLY LEFT BLANK ...
Page 4: ...Inspection and Maintenance Note THIS PAGE INTENTIONALLY LEFT BLANK ...
Page 13: ...INSERT TAB INTRODUCTION ...
Page 14: ......
Page 25: ...INSERT TAB STANDARD PRACTICES ...
Page 26: ......
Page 87: ...INSERT TAB AUXILIARY CONTROLS SYSTEMS MAINTENANCE ...
Page 88: ......
Page 133: ...INSERT TAB SCHEDULED TURBINE MAINTENACE ...
Page 134: ......
Page 157: ...INSERT TAB COMBUSTION INSPECTION ...
Page 158: ......
Page 239: ...INSERT TAB HOT GAS PATH INSPECTION ...
Page 240: ......
Page 313: ...INSERT TAB MAJOR INSPECTION ...
Page 314: ......
Page 316: ...Inspection and Maintenance GEK 107048 Major Inspection 2 THIS PAGE INTENTIONALLY LEFT BLANK ...
Page 363: ...INSERT TAB MAINTENANCE FORMS ...
Page 364: ......