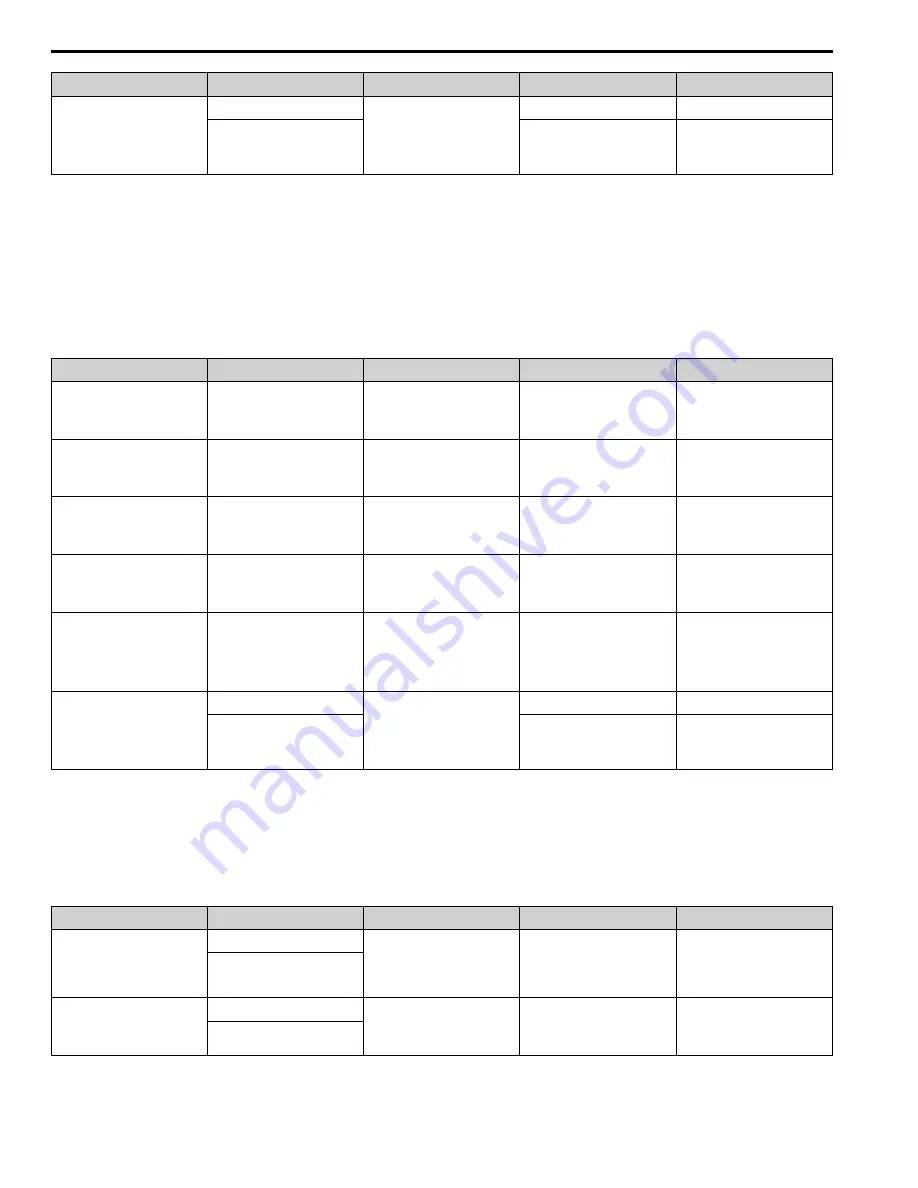
12.2 A: Initialization Parameters
652
YASKAWA
SIEPC71061737B GA800 Drive Technical Reference
Adjustment description
Parameter Number
Possible Solutions
Default
Recommended Setting
•
Increase torque at low speeds
•
Prevent shock during start up
E1-08 [Mid Point A Voltage]
•
If the torque is not sufficient at
low speeds, increase the setting
value.
•
If there is a large shock during
start up, decrease the setting
value.
15.0 V
13.0 V to 16.0 V
E1-10 [Minimum Output Voltage]
9.0 V
7.0 V to 10.0 V
*1
The default setting changes when the settings for
C6-01 [Normal / Heavy Duty Selection]
and
o2-04 [Drive Model (KVA) Selection]
change.
*2
The default setting changes when the settings for
A1-02 [Control Method Selection]
and
E1-03 [V/f Pattern Selection]
change.
*3
This is the setting for 200 V class drives. Multiply the voltage by 2 for 400 V class drives.
Open Loop Vector Control Method
Do not adjust parameter
C4-01 [Torque Compensation Gain]
. Keep this parameter at its default setting.
If you cannot get speed accuracy during regeneration, set
C3-04 = 1 [Slip Compensation at Regen = Enabled Above
6Hz]
. If you cannot get speed accuracy at high speeds, set
C3-05 = 1 [Output Voltage Limit Selection = Enabled]
.
Table 12.16 Adjustment of Drive Control (Open Loop Vector Control Method)
Adjustment description
Parameter Number
Possible Solutions
Default
Recommended Setting
•
Torque, increase speed response
•
Prevent hunting and oscillation
at middle-range speeds (10 Hz
to 40 Hz)
n2-01 [Automatic Freq Regulator
Gain]
•
If torque and speed response are
slow, decrease the setting value.
•
If there is hunting or oscillation,
increase the setting value.
1.00
0.50 - 2.00
•
Torque, increase speed response
•
Prevent hunting and oscillation
C4-02 [Torque Compensation
Delay Time]
•
If torque and speed response are
slow, decrease the setting value.
•
If there is hunting or oscillation,
increase the setting value.
20 ms
20 ms to 100 ms
•
Increase speed response
•
Increase speed stability
C3-02 [Slip Compensation Delay
Time]
•
When speed response is slow,
decrease the setting value.
•
If speed is not stable, increase
the setting value.
200 ms
100 ms to 500 ms
•
Improve speed accuracy
C3-01 [Slip Compensation Gain]
•
If speed is too slow, increase the
setting value.
•
If speed is too fast, decrease the
setting value.
1.0
0.5 - 1.5
•
Increasing motor excitation
sound
•
Prevent hunting and oscillation
at low-range speeds (10 Hz to
or lower)
C6-02 [Carrier Frequency
Selection]
•
If there is a loud motor
excitation sound, increase the
setting value.
•
If there is hunting or oscillation
at low speeds, decrease the
setting value.
1 - F
•
Increase torque and speed
response at low speeds
•
Prevent shock during start up
E1-08 [Mid Point A Voltage]
•
If the torque and speed response
are slow, increase the setting
value.
•
If there is a large shock during
start up, decrease the setting
value.
11.0 V
12.0 V to 13.0 V
E1-10 [Minimum Output Voltage]
2.0 V
2.0 V to 3.0 V
*1
If the value for
C4-02 [Torque Compensation Delay Time]
is high, the current can increase during start up. Adjust and check the current
during start up.
*2
The default setting changes when the settings for
C6-01 [Normal / Heavy Duty Selection]
and
o2-04 [Drive Model (KVA) Selection]
change.
*3
This is the setting for 200 V class drives. Multiply the voltage by 2 for 400 V class drives.
Closed Loop Vector Control Method
Table 12.17 Adjustment of Drive Control (Closed Loop Vector Control Method)
Adjustment description
Parameter Number
Possible Solutions
Default
Recommended Setting
•
Torque, increase speed response
•
Prevent hunting and oscillation
C5-01 [ASR Proportional Gain 1]
•
If the torque and speed response
are slow, increase the setting
value.
•
If there is hunting or oscillation,
decrease the setting value.
20.00
10.00 - 50.00
C5-03 [ASR Proportional Gain 2]
•
Torque, increase speed response
•
Prevent hunting and oscillation
C5-02 [ASR Integral Time 1]
•
If torque and speed response are
slow, decrease the setting value.
•
If there is hunting or oscillation,
increase the setting value.
0.500 s
0.300 s to 1.000 s
C5-04 [ASR Integral Time 2]
Содержание GA800 Series
Страница 2: ...This Page Intentionally Blank 2 YASKAWA SIEPC71061737B GA800 Drive Technical Reference...
Страница 20: ...i 3 Warranty Information 20 YASKAWA SIEPC71061737B GA800 Drive Technical Reference...
Страница 30: ...1 3 Features and Advantages of Control Methods 30 YASKAWA SIEPC71061737B GA800 Drive Technical Reference...
Страница 58: ...2 9 Installation Methods 58 YASKAWA SIEPC71061737B GA800 Drive Technical Reference...
Страница 144: ...4 4 Start up Procedures 144 YASKAWA SIEPC71061737B GA800 Drive Technical Reference Figure 4 8 Basic Steps before Startup...
Страница 268: ...5 6 Safe Disable Input 268 YASKAWA SIEPC71061737B GA800 Drive Technical Reference...
Страница 306: ...6 3 MEMOBUS Modbus Communications 306 YASKAWA SIEPC71061737B GA800 Drive Technical Reference...
Страница 370: ...7 10 Troubleshooting Without Fault Display 370 YASKAWA SIEPC71061737B GA800 Drive Technical Reference...
Страница 426: ...8 7 Storage Guidelines 426 YASKAWA SIEPC71061737B GA800 Drive Technical Reference...