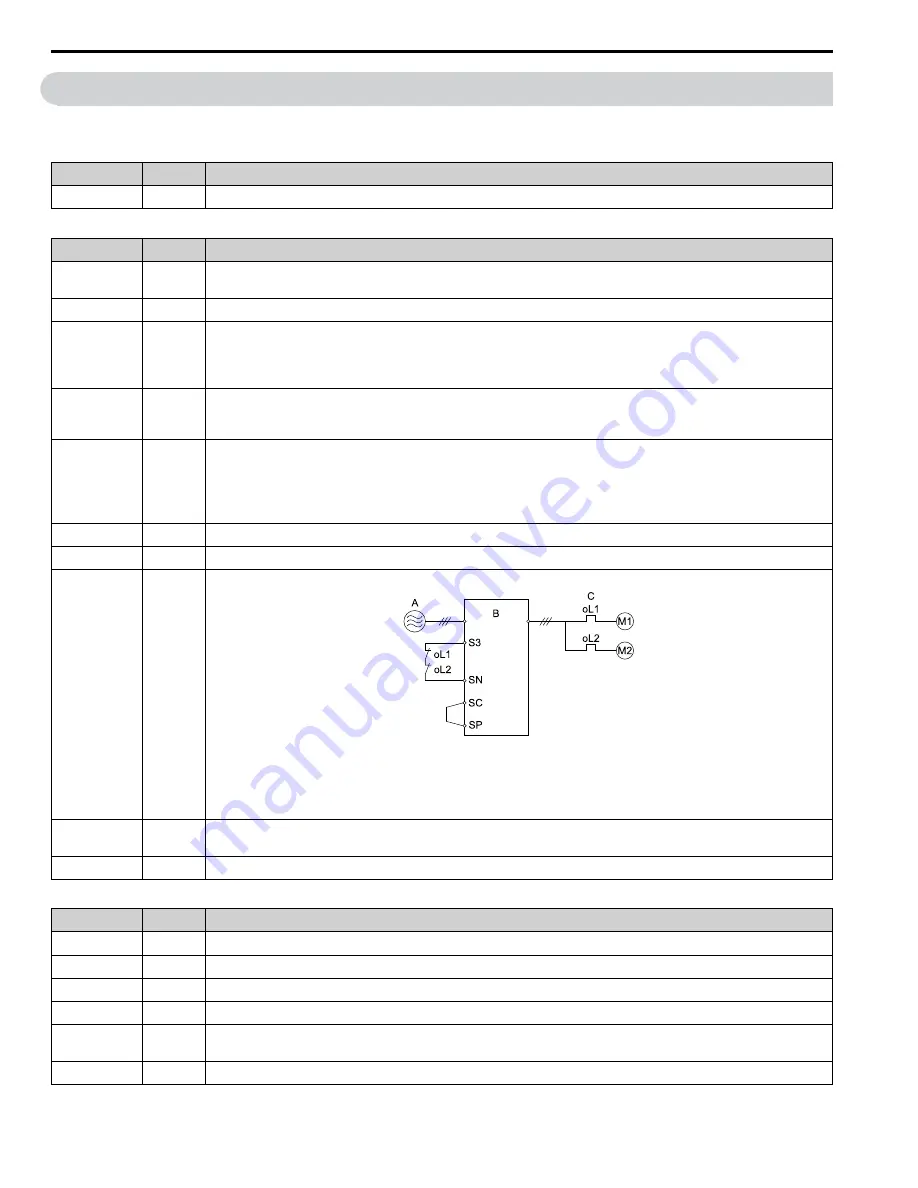
128
YASKAWA
SIEPC71061737B GA800 Drive Technical Reference
3.17
Wiring Checklist
Wire the drive, examine these items, then do a test run.
Table 3.23 Power Supply Voltage
Checked
No.
Item to Check
1
The power supply voltage must be within the input voltage specification range of the drive.
Table 3.24 Main Circuit Wiring
Checked
No.
Item to Check
1
•
Put the power supply through a molded-case circuit breaker (MCCB) before it gets to the drive input.
•
Is an appropriate MCCB connected?
2
Correctly wire the power supply to drive terminals R/L1, S/L2, and T/L3.
3
Correctly wire the drive and motor together.
The motor lines and drive output terminals U/T1, V/T2, and W/T3 must align to make the correct phase order.
Note:
If the phase order is incorrect, the drive will rotate in the opposite direction.
4
Use 600 V heat resistant indoor PVC wire for the power supply and motor lines.
Note:
Wire gauge recommendations assume use of 600 V class 2 heat-resistant indoor PVC wire.
5
Use the correct wire gauges for the main circuit.
Note:
•
When the wiring distance between the drive and the motor is long, use this formula for the voltage drop in the wire:
Motor rated voltage (V) × 0.02 ≥ √3 × wire resistance (Ω/km) × wiring distance (m) × motor rated current (A) × 10
-3
•
When the cable between the drive and motor is longer than 50 m (164 ft), use parameter
C6-02 [Carrier Frequency Selection]
to decrease the
carrier frequency.
6
Correctly ground the drive.
7
Tighten main circuit and grounding terminal screws of the drive to their specified torques.
8
When operating more than one motor from one drive, set up overload protection circuits.
A - Power supply
B - Drive
C - oL1, oL2: Thermal
overload relay
Note:
Set
H1-03 = 25 [Terminal S3 Function Selection = External Fault (NC-Always-Coast)]
.
9
When you use a braking resistor or a braking resistor unit, install an electromagnetic contactor (MC).
Correctly install the resistor and make sure that overload protection uses the MC to shut off the power supply.
10
Make sure that phase advancing capacitors, input noise filters, or ELCBs, GFCIs, RCM/RCDs are NOT installed on the output side of the drive.
Table 3.25 Control Circuit Wiring
Checked
No.
Item to Check
1
Use twisted-pair cable for all drive control circuit wiring.
2
Ground the shields of shielded wiring to the terminal E (G).
3
For 3-Wire sequence, set parameters for MFDI terminals, and wire control circuits.
4
Are the option cards installed correctly?
5
Examine the drive for other wiring errors.
Only use a multimeter to check wiring.
6
Tighten the control circuit terminal screws of the drive to their specified torques.
Содержание GA800 Series
Страница 2: ...This Page Intentionally Blank 2 YASKAWA SIEPC71061737B GA800 Drive Technical Reference...
Страница 20: ...i 3 Warranty Information 20 YASKAWA SIEPC71061737B GA800 Drive Technical Reference...
Страница 30: ...1 3 Features and Advantages of Control Methods 30 YASKAWA SIEPC71061737B GA800 Drive Technical Reference...
Страница 58: ...2 9 Installation Methods 58 YASKAWA SIEPC71061737B GA800 Drive Technical Reference...
Страница 144: ...4 4 Start up Procedures 144 YASKAWA SIEPC71061737B GA800 Drive Technical Reference Figure 4 8 Basic Steps before Startup...
Страница 268: ...5 6 Safe Disable Input 268 YASKAWA SIEPC71061737B GA800 Drive Technical Reference...
Страница 306: ...6 3 MEMOBUS Modbus Communications 306 YASKAWA SIEPC71061737B GA800 Drive Technical Reference...
Страница 370: ...7 10 Troubleshooting Without Fault Display 370 YASKAWA SIEPC71061737B GA800 Drive Technical Reference...
Страница 426: ...8 7 Storage Guidelines 426 YASKAWA SIEPC71061737B GA800 Drive Technical Reference...