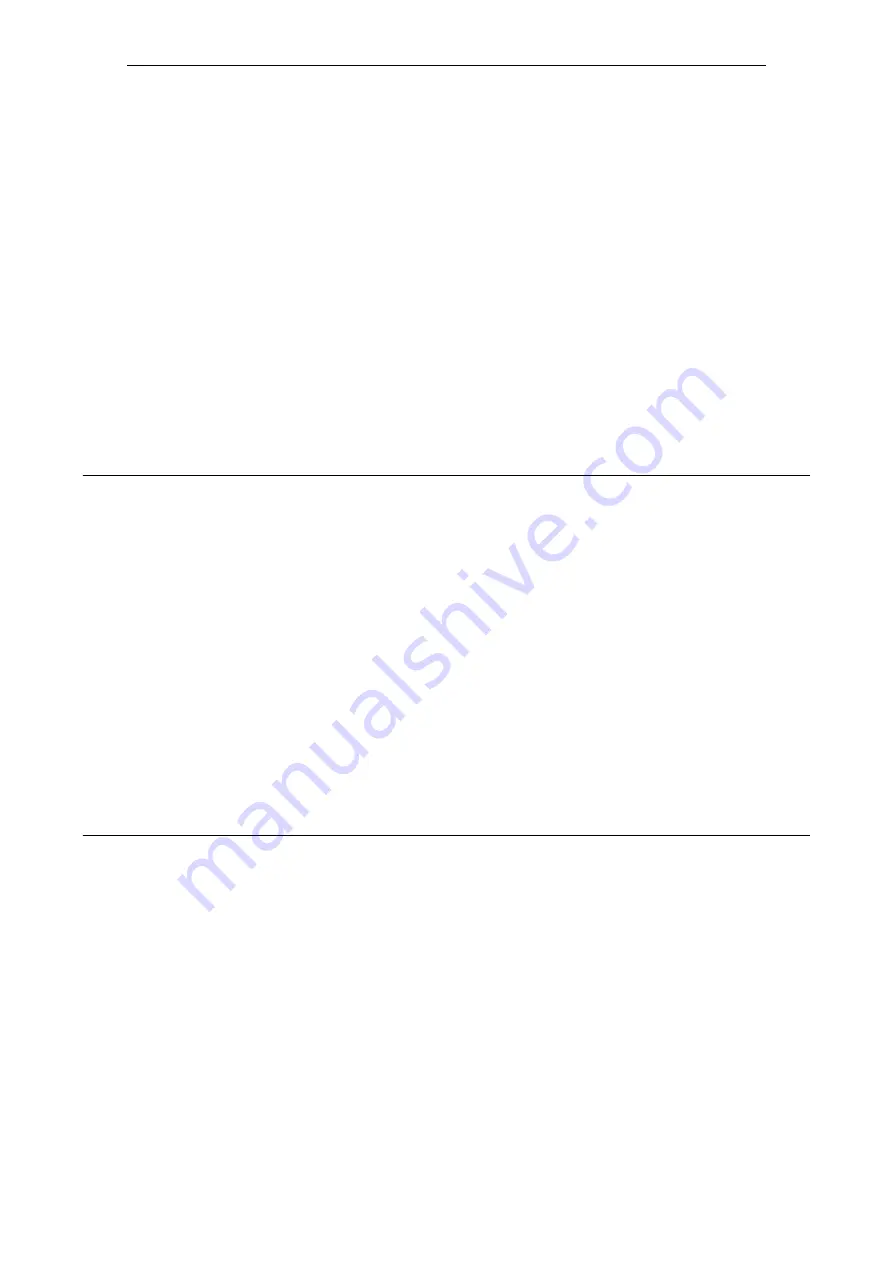
Faults and Alarms
List of faults and alarms
3-572
Siemens AG 2004 All Rights Reserved
SINAMICS G List Manual, Edition 12.2004
Cause:
Only for vector drives (refer to p0107):
It was detected that the motor was stalled for a time longer than that entered into p2178.
Fault value (r0949, decimal):
1: Stall detection using r1408.11 (refer to p1744)
2: Stall detection using r1408.12 (refer to p1745)
See also: p1744, p2178
Remedy:
For closed-loop speed and torque control with speed encoder:
- check the speed signal (interrupted cable, polarity, pulse number).
If there is no fault, then the fault tolerance can be increased (p1744).
For closed-loop speed and torque control without speed encoder:
- check whether the drive stalls due to the load if the speed setpoint is still zero. If yes, then increase the current
setpoint using p1610.
- if the motor excitation (magnetizing) time (r0346) was significantly reduced, then it should be increased again.
- check the current limits (p0640, r0067). If these are too low, then the drive cannot be magnetized.
If there is no fault, then the fault tolerance (p1745) or the delay time (p2178) can be increased.
Reaction upon N:
NONE
Acknowledge
upon N:
NONE
Reaction upon A:
NONE
Acknowledge
upon A:
NONE
A07903
Drive: Motor speed deviation
Reaction:
NONE
Acknowledge:
NONE
Cause:
The absolute value of the speed difference from the two setpoints (p2151, p2154) and the speed actual value (r2169)
exceeds the tolerance threshold (p2163) longer than tolerated (p2164, p2166).
The alarm is only enabled for p2149.0 = 1.
Possible causes could be:
- the load torque is greater than the torque setpoint.
- when accelerating, the torque/current/power limit is reached. If the limits are not sufficient, then it is possible that
the drive has been dimensioned too small.
- the speed controller is inhibited (refer to p0856; refer to Kp/Tn adaptation of the speed controller).
- for closed-loop torque control, the speed setpoint does not track the speed actual value.
- for active Vdc controller.
The signal is not generated if the ramp-function generator tracking prevents the setpoint and actual speed from drift-
ing (moving) apart.
Only for vector drives:
For V/f control, the overload condition is detected as the Imax controller is active.
See also: p2149
Remedy:
- increase p2163 and/or p2166.
- increase the torque/current/power limits.
- enable the speed controller.
- for closed-loop torque control: The speed setpoint should track the speed actual value.
A07910 (N)
Drive: Motor overtemperature
Reaction:
NONE
Acknowledge:
NONE
Cause:
KTY:
The motor temperature has exceeded the alarm threshold (p00604).
VECTOR: The response parameterized in p0610 becomes active.
PTC:
The response threshold of 1650 Ohm was exceeded.
Alarm value (r2124, decimal):
1: No output current reduction.
2: Output current reduction active.
See also: p0604, p0610
Remedy:
- check the motor load.
- check the motor ambient temperature.