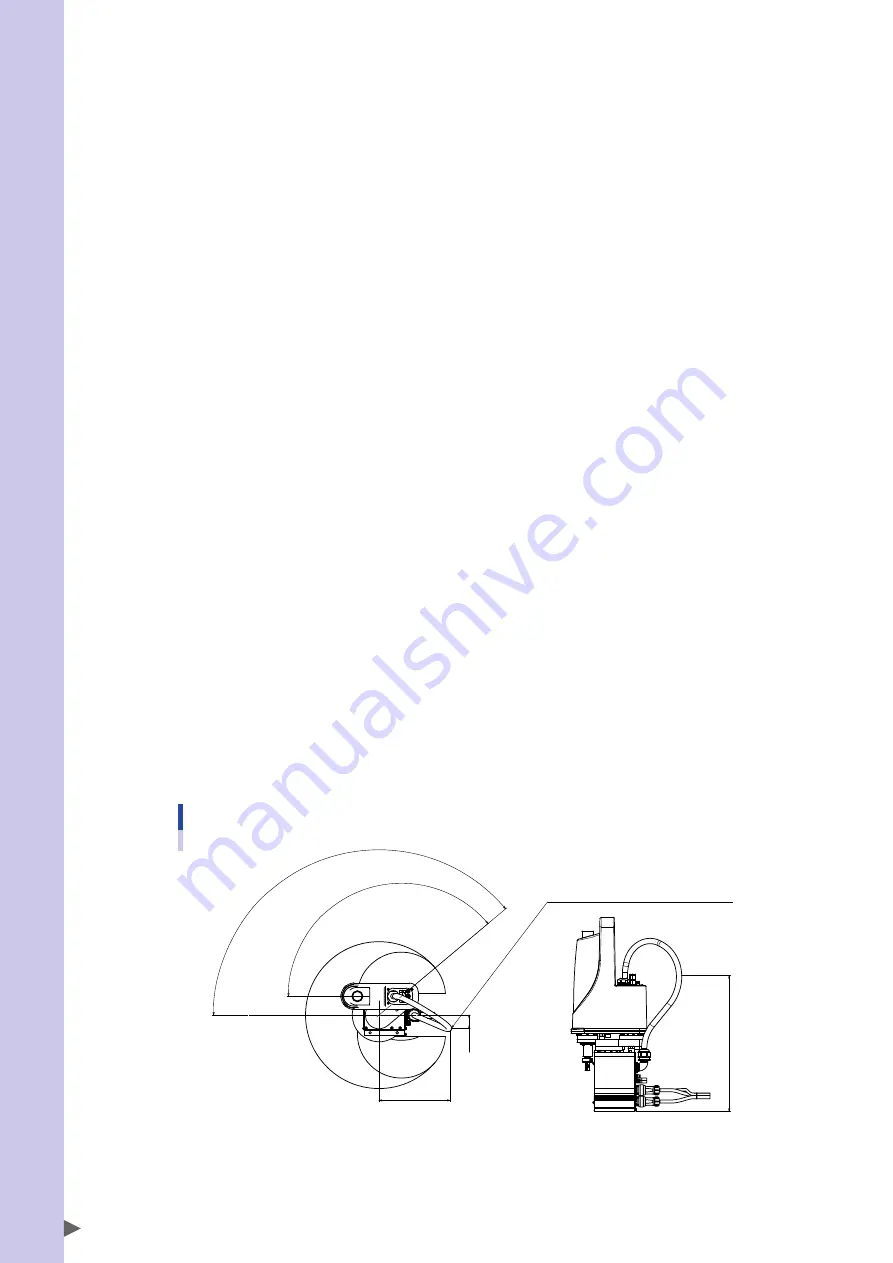
Intr
oduction
ii
2.
Repetitive positioning accuracy
"Repetitive positioning accuracy" is not guaranteed under the following conditions.
[1] Factors related to absolute accuracy
• If the accuracy between the coordinate positions (command positions) inside the robot controller and the real space
positions (moving positions) is required.
[2] Motion pattern factors
• If a motion approaching to the teaching point from a different direction is included during repetitive operation.
• If the power is turned off or the robot is stopped before completing the motion or the moving speed is changed even when
approaching to the teaching point from the same direction.
• If the robot is moved to the teaching point using a hand system different from the hand system (right-handed or left-handed
system) used for the teaching.
[3] Temperature factors
• If the ambient temperature environment changes significantly.
• If the temperature of the robot main body changes.
[4] Load variation factors
• If load conditions vary during operation (the load varies depending on whether or not the workpiece is present, etc.).
3.
If the X-axis, Y-axis or R-axis rotation angle is small.
If the X-axis, Y-axis or R-axis rotation angle is smaller than 5° so that it moves in almost the same position, an oil film is difficult
to be formed on the joint support bearing, possibly leading to damage to the bearing. In this type of operation, add a movement so
that the joint moves through 90° or more, about 5 times a day.
4.
Do not remove the Z-axis upper-end mechanical stopper
Removing or moving the upper-end mechanical stopper attached to the Z-axis spline can damage the Z-axis ball screw. Never
remove or move it.
5.
If the Z-axis spline vibrates.
The Z-axis spline of the R6YXGL250, R6YXGL350, R6YXGL400, R6YXGL500, R6YXGL600, R6YXGS300 and R6YXGS400
tends to vibrate in a Z-axis operation speed range of 20% to 40%. If the Z-axis spline vibrates, operate it beyond this operation
speed range.
6.
If the machine harness projects toward the base rear side.
In the R6YXGL250, R6YXGL350, R6YXGL400, R6YXGL500 and R6YXGL600, the machine harness may project toward the
base rear side according to the arm position.
The projection amount by arm position is described in "1.2 External view and dimensions" in Chapter 8. So, refer to this section
for further information.
Z
X
Y
→
Y+
↓
X+
Projection of the machine harness toward the base rear side (Example: R6YXGL250)
θx
(C
CW
is
the
plu
s di
recti
on.)
θy
(C
CW
is t
he p
lus direc
tion.)
Harness projection amount Y to the base rear
side and positions X and Z with respect to
the arm positions θx and θy
Summary of Contents for R6YXG500
Page 1: ...ZX T Series Cat No I155E EN 03A R6Y XG series INSTALLATION MANUAL SCARA Robots XG Series...
Page 2: ......
Page 10: ......
Page 36: ......
Page 38: ......
Page 40: ......
Page 46: ......
Page 48: ......
Page 56: ......
Page 174: ......
Page 176: ......
Page 220: ......
Page 221: ...Chapter 4 Periodic inspection Contents 1 Overview 4 1 2 List of inspection items 4 2...
Page 222: ......
Page 226: ......
Page 227: ...Chapter 5 Harmonic drive replacement period Contents 1 Overview 5 1 2 Replacement period 5 2...
Page 228: ......
Page 232: ......
Page 238: ......
Page 240: ......
Page 244: ......
Page 246: ......
Page 323: ...8 Specifications 8 77 1 3 Robot inner wiring diagram Robot inner wiring diagram R6YXG500...