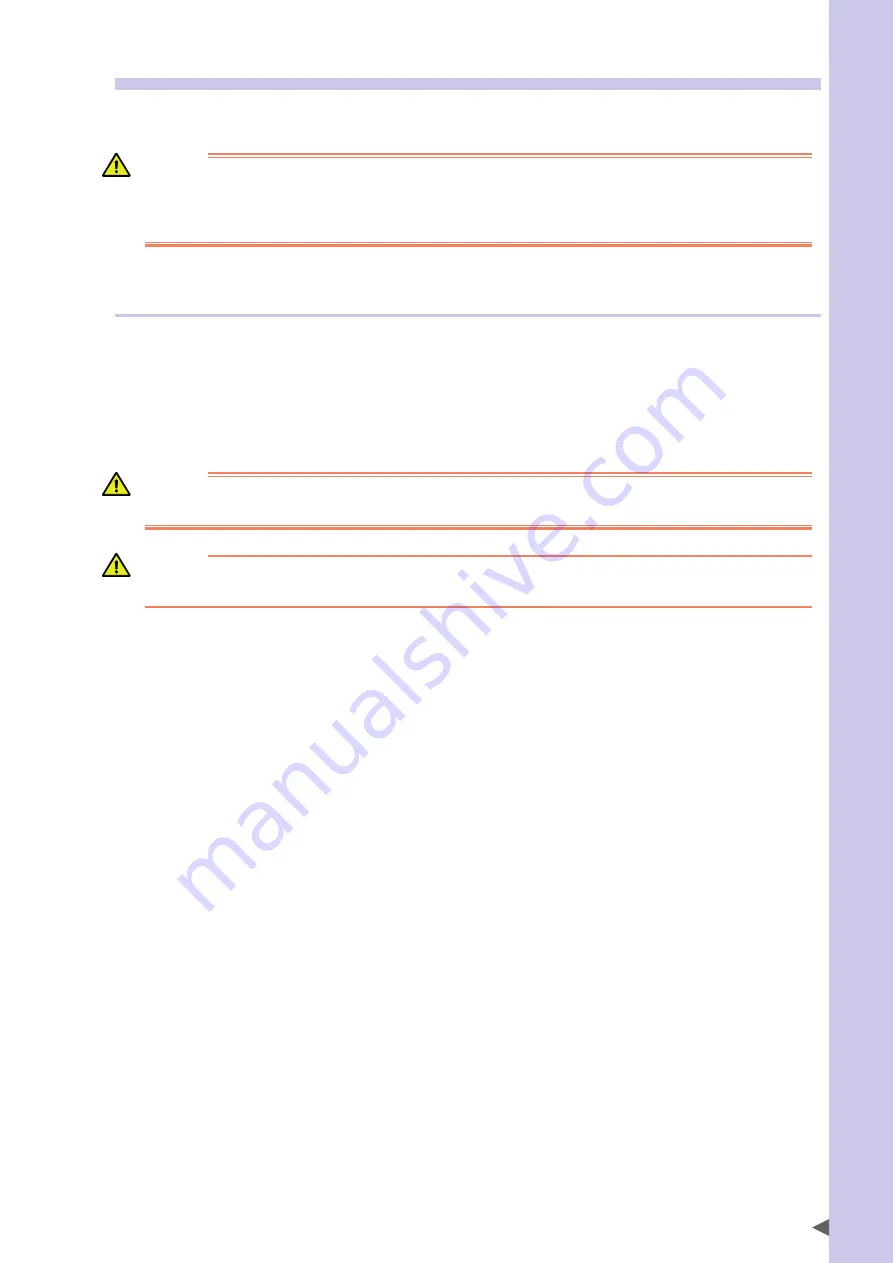
Safety Instr
uctions
S-15
4.5 Operation
When operating a robot, ignoring safety measures and checks may lead to serious accidents. Always take the following
safety measures and checks to ensure safe operation.
DANGER
CHECK THE FoLLoWInG poInTS bEFoRE STARTInG RoboT opERATIon.
• no onE IS WITHIn THE RoboT SAFETY EnCLoSURE.
• THE pRoGRAmmInG UnIT IS In THE SpECIFIEd LoCATIon.
• THE RoboT And pERIpHERAL EqUIpmEnT ARE In Good CondITIon.
4.5.1 Trial operation
After installing, adjusting, inspecting, maintaining or repairing the robot, perform trial operation using the following
procedures.
1.
If a safety enclosure has not yet been provided right after installing the robot:
Then rope off or chain off the movement range around the robot in place of the safety enclosure and observe the following points.
See “7.1 Movement range” in “Safety instructions” for details on the robot’s movement range.
DANGER
pLACE A "RoboT IS movInG - KEEp AWAY!" SIGn To KEEp THE opERAToR oR oTHER pERSonnEL FRom EnTERInG
WITHIn THE movEmEnT RAnGE oF THE RoboT.
WARNING
• USE STURdY, STAbLE poSTS WHICH WILL noT FALL ovER EASILY.
• THE RopE oR CHAIn SHoULd bE EASILY vISIbLE To EvERYonE ARoUnd THE RoboT.
2.
Check the following points before turning on the controller.
• Is the robot securely and correctly installed?
• Are the electrical connections to the robot wired correctly?
• Are items such as air pressure correctly supplied?
• Is the robot correctly connected to peripheral equipment?
• Have safety measures (safety enclosure, etc.) been taken?
• does the installation environment meet the specified standards?
3.
After the controller is turned on, check the following points from outside the safety enclosure.
• does the robot start, stop and enter the selected operation mode as intended?
• does each axis move as intended within the soft limits?
• does the end effector move as intended?
• Are the correct signals being sent to the end effector and peripheral equipment?
• does emergency stop function?
• Are teaching and playback functions normal?
• Are the safety enclosure and interlocks functioning as intended?
Summary of Contents for R6YXG500
Page 1: ...ZX T Series Cat No I155E EN 03A R6Y XG series INSTALLATION MANUAL SCARA Robots XG Series...
Page 2: ......
Page 10: ......
Page 36: ......
Page 38: ......
Page 40: ......
Page 46: ......
Page 48: ......
Page 56: ......
Page 174: ......
Page 176: ......
Page 220: ......
Page 221: ...Chapter 4 Periodic inspection Contents 1 Overview 4 1 2 List of inspection items 4 2...
Page 222: ......
Page 226: ......
Page 227: ...Chapter 5 Harmonic drive replacement period Contents 1 Overview 5 1 2 Replacement period 5 2...
Page 228: ......
Page 232: ......
Page 238: ......
Page 240: ......
Page 244: ......
Page 246: ......
Page 323: ...8 Specifications 8 77 1 3 Robot inner wiring diagram Robot inner wiring diagram R6YXG500...