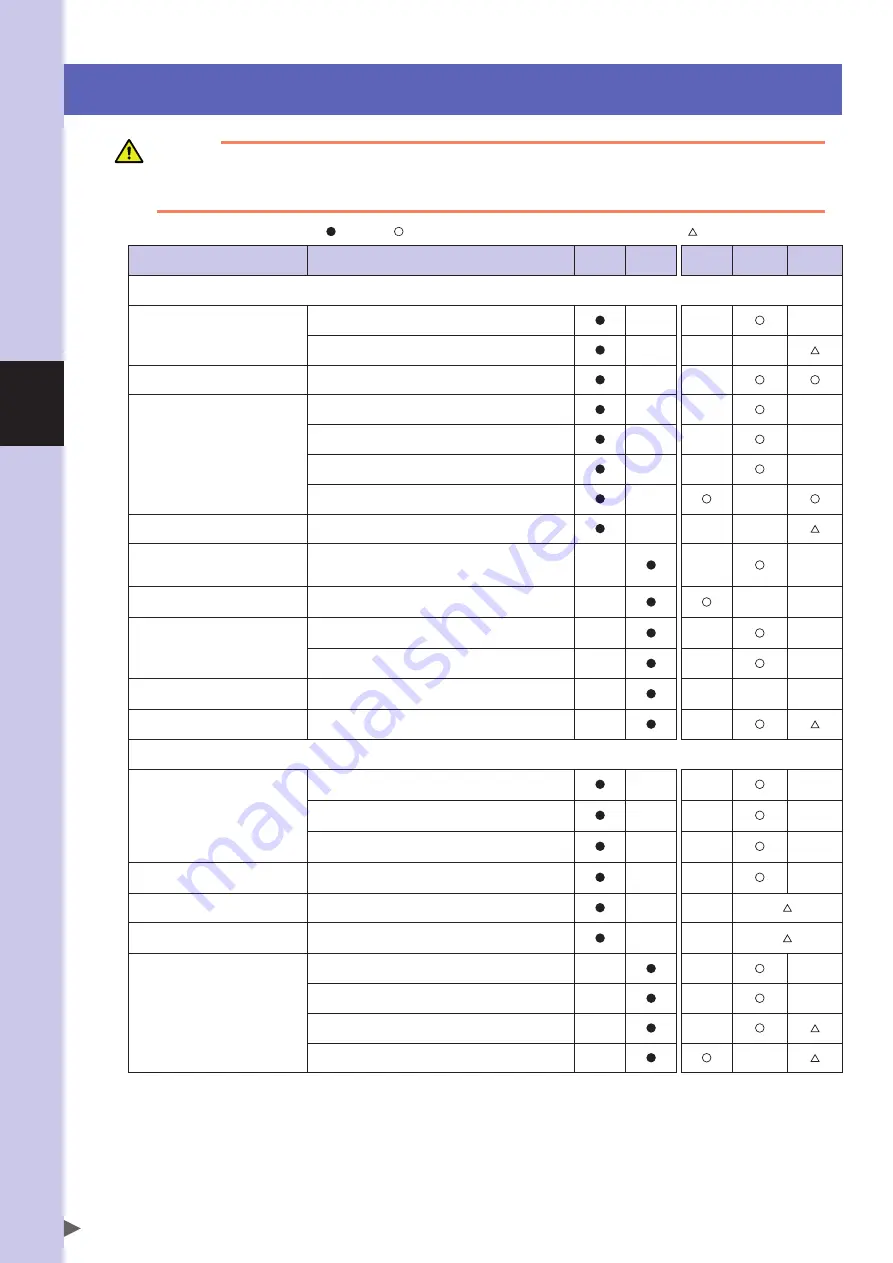
4
Per
iodic inspection
4-2
2. List of inspection items
WARNING
onLY qUALIFIEd EnGInEERS WHo HAvE RECEIvEd THE RoboT TRAInInG CoURSE CondUCTEd bY YoUR
dISTRIbUToR ARE ALLoWEd To InSpECT THE ITEmS nEEdInG THE CovER REmovAL WoRK WHILE REFERRInG
To THE SEpARATE mAInTEnAnCE mAnUAL FoR XG SERIES.
: Conduct. : Conduct if trouble is found as a result of inspection. : Contact your distributor.
Location
Contents
Daily
6-month
Cleaning Adjustment Replacement
■
Inspection with the controller turned off
Machine harness
Robot cable
• Check for scratch, dent, or excessive bend.
• Check for damage.
Cables prepared by user
• Check for scratch, dent, or excessive bend.
Regulator
Joint
Air tube
Solenoid valve
Air cylinder
• Check that the air pressure level is correct.
• Check for air leak.
• Check that the drain is discharged.
• Check the air filter for contamination or damage.
Exterior of robot
• Check for damage.
Major bolts and screws of robot
main body (those exposed to the
outside)
• Check for looseness. (*1)
Detection parts of X-axis, Y-axis,
and R-axis origin sensors
• Check for contamination.
Controller
• Check the terminal on the outside of the controller
for looseness.
• Check the connection connector for looseness. (*2)
Application of grease to Z-axis
spline and Z-axis ball screw (*3)
• Remove the old grease with a cloth rag and apply
Alvania grease S2 (Showa Shell).
Z-axis ball screw and ball spline
• Check for play.
■
Inspection with the controller turned on
Safeguard enclosure
• Check that the safeguard enclosure is located at its
specified position.
• Check that the emergency stop turns on when the
safeguard enclosure is open.
• Check that the warning label is affixed to the
entrance.
Emergency stop button
• Check that the emergency stop turns on when
pressed.
Robot operation
• Check for unusual operation, vibration, or noise.
Functional check of Z-axis brake
(*4)
• drop amount from the Z-axis rest state is 3 mm or
less.
Air cooling fan on the rear of the
controller
• Check that the fan rotates.
• Check for object blocking the fan.
• Check for noise during rotation. (*5)
• Check the fan cover for contamination.
*1: If any bolt or screw is loose, retighten it. (For details about tightening torque, see the table below.)
*2: For details, see "4. Robot cable connection" in Chapter 2.
*3: For detail about how to apply the grease, see the separate Maintenance Manual.
*4: When the emergency stop button is pressed outside the safeguard enclosure or when the controller power is turned off,
visually inspect the Z-axis brake.
*5: If any object is found through the visual inspection, remove it. If noise is heard even when no object is found, contact your
distributor.
Summary of Contents for R6YXG500
Page 1: ...ZX T Series Cat No I155E EN 03A R6Y XG series INSTALLATION MANUAL SCARA Robots XG Series...
Page 2: ......
Page 10: ......
Page 36: ......
Page 38: ......
Page 40: ......
Page 46: ......
Page 48: ......
Page 56: ......
Page 174: ......
Page 176: ......
Page 220: ......
Page 221: ...Chapter 4 Periodic inspection Contents 1 Overview 4 1 2 List of inspection items 4 2...
Page 222: ......
Page 226: ......
Page 227: ...Chapter 5 Harmonic drive replacement period Contents 1 Overview 5 1 2 Replacement period 5 2...
Page 228: ......
Page 232: ......
Page 238: ......
Page 240: ......
Page 244: ......
Page 246: ......
Page 323: ...8 Specifications 8 77 1 3 Robot inner wiring diagram Robot inner wiring diagram R6YXG500...