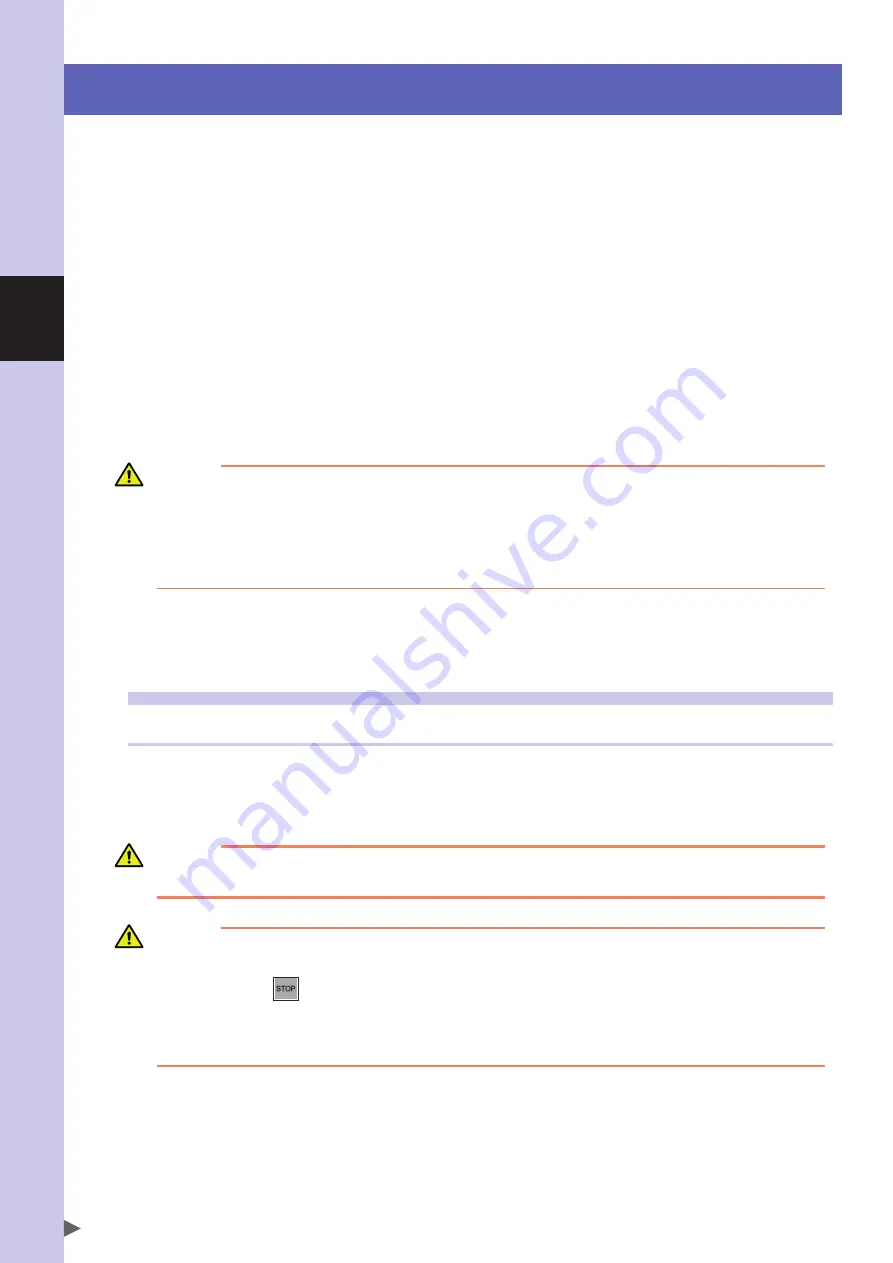
3
Robot settings
3-2
2. Adjusting the origin
All models of the XG series robots use an absolute type position detector. The origin position (zero pulse point) can be
determined by absolute reset. Once absolute reset is performed, you do not have to repeat absolute reset when turning
the power on next time. However, absolute reset is required if any of the following cases occur. The robot is shipped
from the factory in condition "3." (below), so please perform absolute reset after installing the robot. For more details
on absolute reset, refer to "Absolute Reset" in Chapter 4 of the "omRon Robot Controller User's manual".
1.
Absolute-related error occurred on the axis.
2.
Power drop was detected in the absolute battery for the driver installed inside the robot controller.
3.
Cable connecting the robot unit to the controller was disconnected. (This is the status when shipped from the factory.)
4.
Robot generation was changed.
5.
Parameters were initialized.
6.
Axis parameters "Origin shift", "Origin method", "Origin direction" or "Motor direction" were changed.
7.
motor was replaced. (motor wiring connector was removed.)
8.
data in the ALL data file (extension: ALL) or parameter file (extension: pRm) was written into the controller by way of the
RS-232C.
The following sections explain how to perform absolute reset.
CAUTION
• If any of the above cases occur after installing the robot, absolute reset must be performed again. To perform absolute reset, move the
robot arms back to their origin positions where the robot does not interfere with peripheral equipment after the setup is complete.
• After performing absolute reset, move the robot to a known point to check whether the origin position is correctly set. When doing
this check, move the robot at the slowest possible speed.
• The standard coordinate and point data must be reset when the origin position is changed.
• make point data setting after changing the origin position. After changing the origin position, do not use the previous point data.
There are three absolute reset methods for the XG series: the sensor method, mark method and stroke end method. The
X-axis, Y-axis and R-axis use the sensor method as the initial setting, while the Z-axis uses the stroke end method.
2.1
Absolute reset method
2.1.1 Sensor method (X-axis, Y-axis and R-axis)
In the sensor method, the target axis is automatically operated for the absolute reset, and the absolute reset is performed
at the position where the proximity sensor provided on the target axis detects the detection area (dog). The absolute
reset in the sensor method can be executed with the programming box (pbEX/pb), RS-232C communication, and
dedicated input.
WARNING
SERIoUS InJURY mIGHT oCCUR FRom pHYSICAL ConTACT WITH THE RoboT dURInG opERATIon. nEvER EnTER
WITHIn THE RoboT movEmEnT RAnGE dURInG AbSoLUTE RESET.
CAUTION
The origin cannot be detected in any axis which is not positioned on the plus side from the origin (see the Fig. stated in step 6 of "2.3.1
Sensor method (X-axis, Y-axis, and R-axis)" in this Chapter) before starting the absolute reset operation. (Factory setting at shipment.)
In this case, press the
key to interrupt the absolute reset operation, move the target axis to the plus side of the origin, and
reperform the origin return operation. If the absolute reset operation is not interrupted, the robot will continue the operation and may
collide with the mechanical stopper or a peripheral device. Since a mechanical stopper is not provided in the R-axis, the wiring and
piping installed on the end effecter may be wound up by the operation.
Summary of Contents for R6YXG500
Page 1: ...ZX T Series Cat No I155E EN 03A R6Y XG series INSTALLATION MANUAL SCARA Robots XG Series...
Page 2: ......
Page 10: ......
Page 36: ......
Page 38: ......
Page 40: ......
Page 46: ......
Page 48: ......
Page 56: ......
Page 174: ......
Page 176: ......
Page 220: ......
Page 221: ...Chapter 4 Periodic inspection Contents 1 Overview 4 1 2 List of inspection items 4 2...
Page 222: ......
Page 226: ......
Page 227: ...Chapter 5 Harmonic drive replacement period Contents 1 Overview 5 1 2 Replacement period 5 2...
Page 228: ......
Page 232: ......
Page 238: ......
Page 240: ......
Page 244: ......
Page 246: ......
Page 323: ...8 Specifications 8 77 1 3 Robot inner wiring diagram Robot inner wiring diagram R6YXG500...