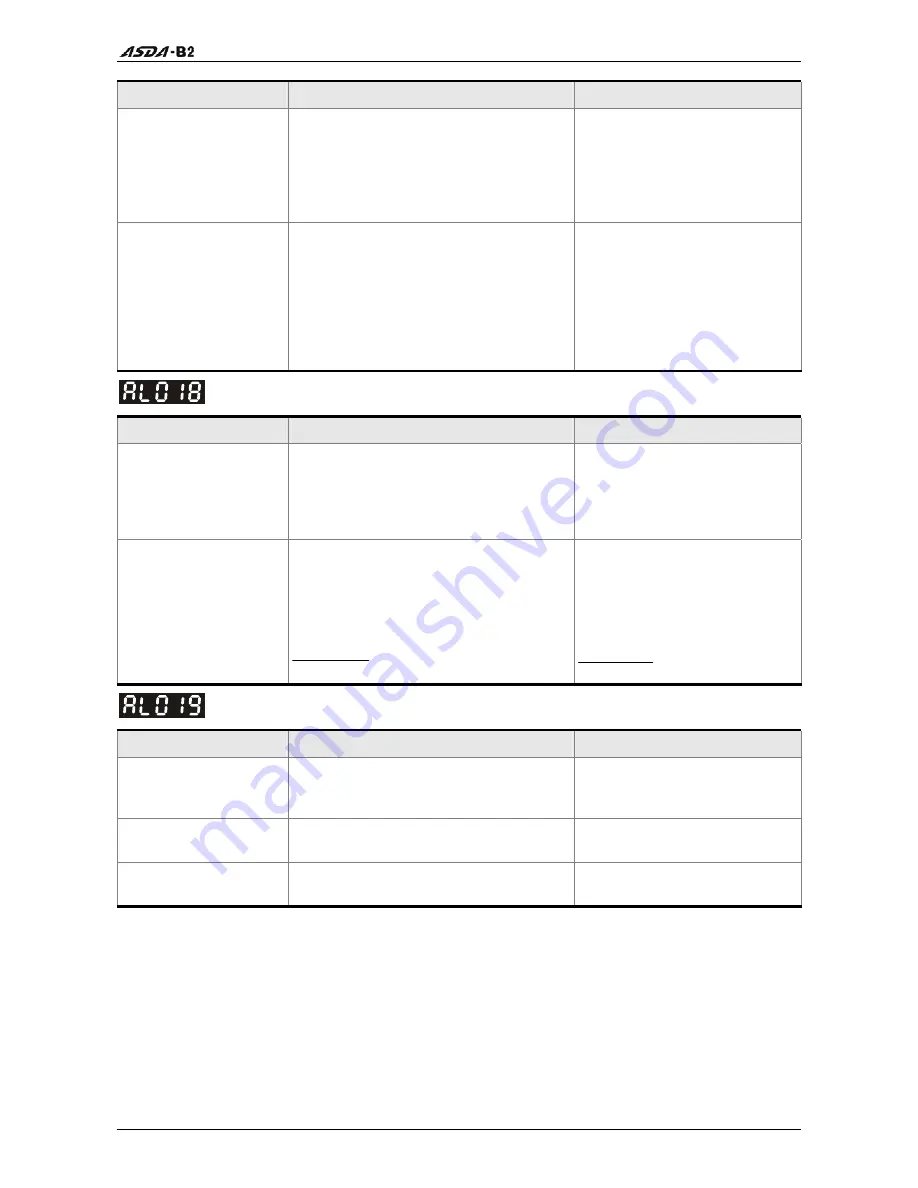
Chapter 10 Troubleshooting
Revision June 2010
10-7
Potential Cause
Checking Method
Corrective Actions
The setting value of
hidden parameter is in
error.
Press SHIFT key on the drive keypad
and examine if E100X is displayed on
LED display.
If this fault occurs when
resetting the parameter
settings, it indicates that the
servo drive type is not set
correctly. Correctly set the
servo drive type again.
Data in EE-PROM is
damaged.
Press SHIFT key on the drive keypad
and examine if E0001 is displayed on
LED display.
If this fault occurs when power
is applied to the drive, it
indicates that the data in EE-
RPM is damaged or there is no
data in EE-PROM. Please
contact your distributor for
assistance or contact with
Delta.
: Encoder output error
Potential Cause
Checking Method
Corrective Actions
Encoder itself or the
wiring of encoder is in
error.
Check if the recent fault records (P4-
00 ~ P4-05) display on the drive
keypad in accordance with the fault
codes AL011, AL024, AL025 and
AL026.
Perform the corrective actions
as described in AL011, AL024,
AL025 and AL026.
The output frequency
for pulse output may
exceed the limit of its
allowable setting
value.
Check if the following conditions
occur:
Condition 1: Motor speed is above the
value set by P1-76.
Condition 2:
6
10
19.8
4
46
1
P
60
Speed
Motor
×
>
×
−
×
Correctly set P1-76 and P1-46.
1.
Ensure that the motor speed
is below the value set by P1-
76.
2.
6
10
19.8
4
46
1
P
60
Speed
Motor
×
<
×
−
×
: Serial communication error
Potential Cause
Checking Method
Corrective Actions
Communication
parameter setting is
defective.
Check the communication parameter
setting.
Correctly set parameter
setting.
Communication
address is incorrect.
Check the communication address.
Correctly set communication
address.
Communication value
is incorrect.
Check the communication value.
Correctly set communication
value.
Summary of Contents for ASD-B2-0121-B
Page 1: ......
Page 13: ...Table of Contents xii Revision June 2010 This page intentionally left blank...
Page 17: ...Chapter 1 Unpacking Check and Model Explanation 1 4 Revision June 2010 ECMA Series Servo Motor...
Page 87: ...Chapter 4 Display and Operation 4 12 Revision June 2010 This page intentionally left blank...
Page 131: ...Chapter 6 Control Modes of Operation 6 22 Revision June 2010 Time Domain...
Page 267: ...Chapter 8 MODBUS Communications 8 18 Revision June 2010 This page intentionally left blank...
Page 271: ...Chapter 9 Maintenance and Inspection 9 4 Revision June 2010 This page intentionally left blank...
Page 291: ...Chapter 11 Specifications 11 8 Revision June 2010 11 3 Servo Motor Speed Torque Curves...