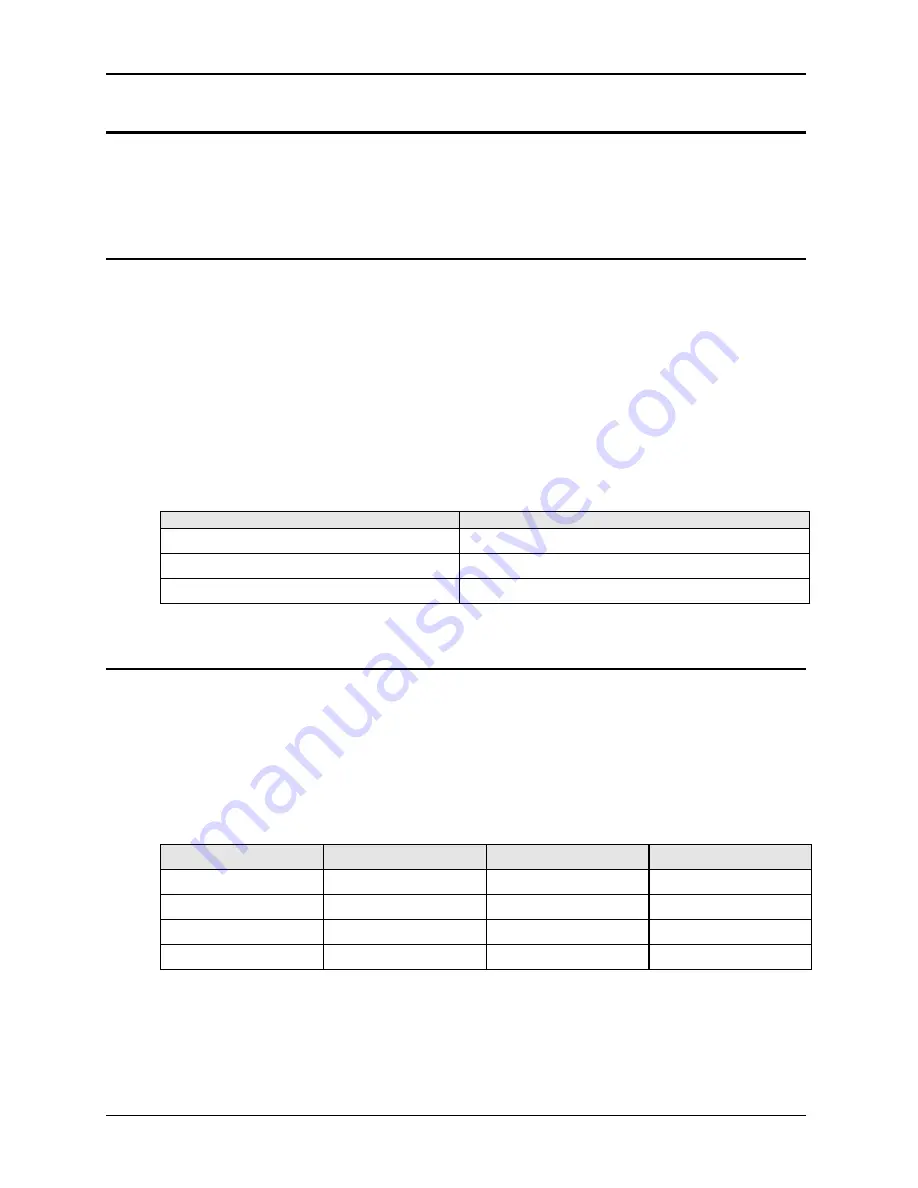
User Manual
120
i Series / iX Series
6.6 Non-Routine Calibration
The non-routine calibration involves removing the top cover from the power source. Remove the
line power from the power source before removing the top cover. Most of the adjustments are on
the Current Limit Assembly. One adjustment is on I/O Board Assembly. Refer to Figure 6-3 for
the location of the adjustments.
6.6.1 Power Source Gain Adjustment:
To make this adjustment the top cover must be removed and voltages must be monitored at
various test points. The test point used depends upon the phase to be adjusted. Refer to Table
6-4 for the test point. The adjustment is R14 on the Current Limit Board. Refer to Figure 6-3 for
the location R14 on the Current Limit Board.
On the Phase A/CPU board, monitor TP31 with respect to TP1. P300 VDC. Adjust
R14 on the Current Limit Board so that the voltage at TP31 is 13.0 VDC. Program -300 VDC.
Check voltage at TP31. If it is greater than 13.0 VDC, adjust R14 for 13.0 VDC. If it is less than
13.0 VDC, do nothing.
For multiphase power systems with one controller, 15003iX, the adjustment for Phase B and C
must be made to R14 on the Current Limit Board for the power source of the respective phase.
PHASE
TEST POINT (Controller in Phase A Power Source)
A
TP31 to TP1 CPU/Phase A
B
TP5 to TP1A Phase B/C
C
TP6 to TP1A Phase B/C
Table 6-4: Gain Adjustments
6.6.2 Current Limit Calibration:
Program the output to the 150 VAC range and the current limit to IPROG in Table 6-5. Program
the output to the constant current mode (CC). Apply full load for the 150 volt range to the output.
Adjust R38 on the Current Limit Board for an output current of ISET in Table 6-5.
If the current is less than the set value, observe the Front Panel Overload Indicator for each
power source. Adjust R38 on the Current Limit Board of the Power Sources with the Indicator
illuminated. Adjust R38 just to the point the output current is on 103% above the programmed
value.
MODEL
IPROG
ISET
R LOAD (ohms)
5001, 15003
30
31.0
4.5, 5KW
10001, 30003
90
63.0
2.25, 10KW
15001
90
93.0
1.5, 15KW
3001, 9003
18
18.6
8, 3KW
Table 6-5: Current Limit Calibration
Repeat this adjustment for the Phase B and Phase C power sources of a 15003 power system.
Summary of Contents for 10001i
Page 2: ......
Page 3: ......
Page 6: ...ii This page intentionally left blank...
Page 38: ...User Manual 24 i Series iX Series Figure 3 5 Rear Panel View for the 3001i 3001iX...
Page 39: ...User Manual i Series iX Series 25 Figure 3 6 Rear Panel View for the 5001i 5001iX...
Page 43: ...User Manual i Series iX Series 29 Figure 3 8 Functional Test Setup...
Page 44: ...User Manual 30 i Series iX Series Figure 3 9 Single Phase 10000 VA System 10001iX i...
Page 46: ...User Manual 32 i Series iX Series Figure 3 11 Single Phase 15000 VA System 15001iX i...
Page 48: ...User Manual 34 i Series iX Series Figure 3 13 Connection With MODE Option...
Page 118: ...User Manual 104 i Series iX Series Figure 5 2 Power Source Module Block Diagram...
Page 121: ...User Manual i Series iX Series 107 Figure 5 3 5001i Internal Layout...
Page 122: ...User Manual 108 i Series iX Series Figure 5 4 Logic Board LED s...
Page 124: ...User Manual 110 i Series iX Series Figure 5 5 AC Power Stage Layout...
Page 125: ...User Manual i Series iX Series 111 Figure 5 6 AC Control Logic Block Diagram...
Page 138: ...User Manual 124 i Series iX Series Figure 6 3 Adjustment Location...
Page 152: ...User Manual 138 i Series iX Series Figure 9 4 Voltage Modulation...
Page 219: ...User Manual i Series iX Series 205 Figure 9 36 Example Connection With 5001iX and EOS 1...
Page 221: ...User Manual i Series iX Series 207 Figure 9 38 15003iX CTS EOS3 LR3...
Page 222: ...User Manual 208 i Series iX Series Figure 9 39 15003iX 3 EOS3...
Page 233: ...User Manual i Series iX Series 219 Figure 9 41 Example Connection With MODE iX...
Page 240: ...User Manual 226 i Series iX Series Figure 9 42 Example Connections With OMNI 1 18i...
Page 241: ...User Manual i Series iX Series 227 Figure 9 43 Example Connections With OMNI 3 18i...