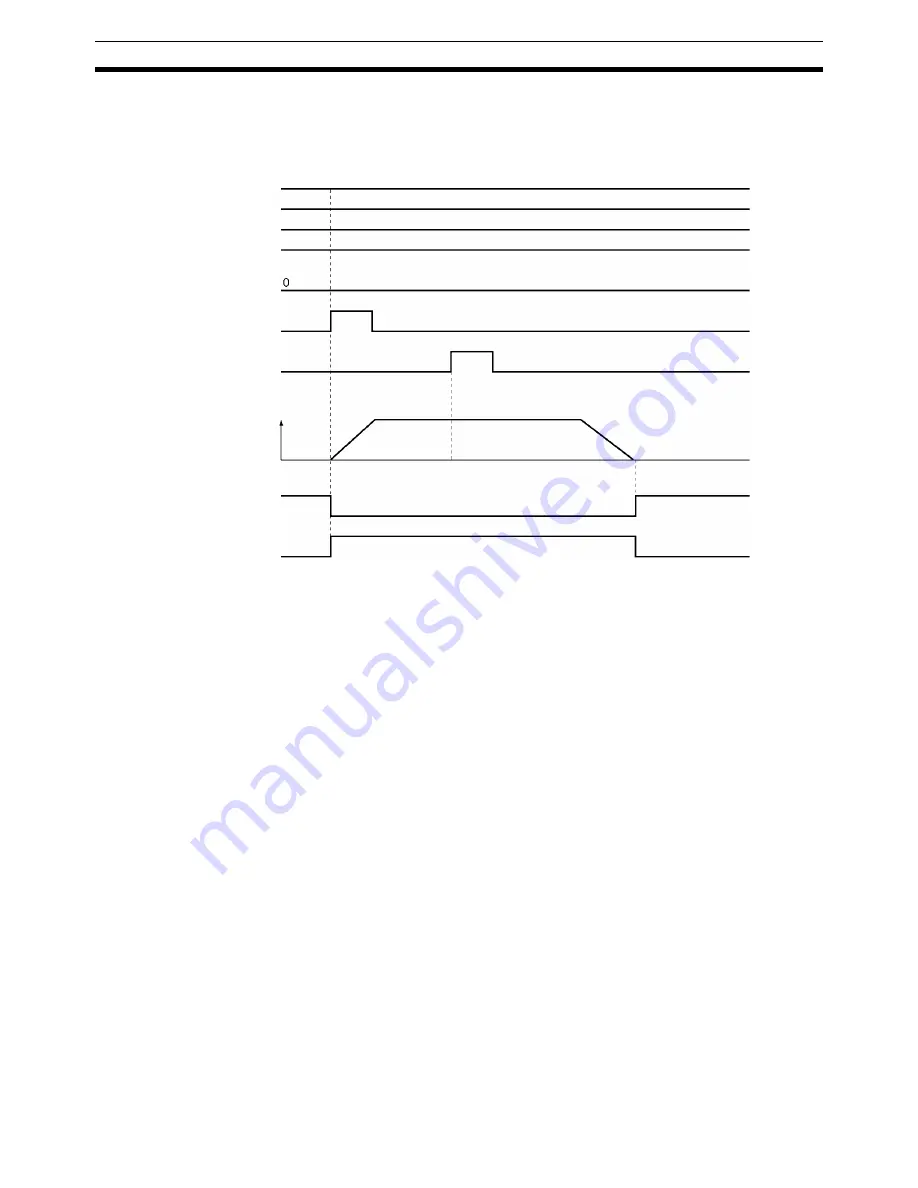
242
Forced Interrupt
Section 9-4
9-3-6
Timing Chart
The following timing chart illustrates interrupt feeding under direct operation,
using the X axis for a 4-axis PCU as an example. There is a movement of
10,000 pulses in the direction of travel.
9-4
Forced Interrupt
FORCED INTERRUPT is a command which is only enabled during memory
operation. It is used for taking emergency evasive action from the current
operation under memory operation.
Outline of Operation
When a sequence number with the forced interrupt operation set is specified
and the FORCED INTERRUPT Bit is turned ON, the pulse output of the mem-
ory operation currently being executed is stopped (without deceleration) and
positioning is executed from the specified sequence number. There is no need
to turn ON the Sequence Number Enable Bit.
The forced interrupt operation will depend on the startup method at the time of
the interrupt. For operation started with INDEPENDENT START, operation will
follow terminating completion. For any other kind of startup method, operation
will be determined by the completion code in the positioning sequence.
Note
A sequence number error (error code 8101) will be generated in the following
cases.
• If forced interrupt is executed at power up or restart, or after execution of
origin search, origin return, or present position preset.
• If forced interrupt is executed at bank end.
Procedure for Using Forced Interrupt
1,2,3...
1.
Set the forced interrupt action in the positioning sequence and transfer it to
the PCU.
2.
When a forced interrupt is required, specify the sequence number set in (1)
and FORCED INTERRUPT from OFF to ON.
Position
(I+8, I+9)
Speed
(I+10, I+11)
Direction designation
(word n, bit 10)
Interrupt feed
(word n, bit 5)
Speed
Pulse output
Positioning Completed
Flag (word n+8, bit 05)
Busy Flag
(word n+8, bit 13)
Time
10,000 pulses
2710 Hex (10000) (Interrupt feeding in the direction of travel)
3E8 Hex (1000)
X-axis interrupt input
signal (input to PCU)
Summary of Contents for CJ1W-C113 - REV 02-2008
Page 2: ...CJ1W NC113 213 413 133 233 433 Position Control Units Operation Manual Revised February 2008 ...
Page 3: ...iv ...
Page 13: ...xiv ...
Page 15: ...xvi ...
Page 19: ...xx ...
Page 27: ...xxviii Conformance to EC Directives 6 ...
Page 43: ...16 Control System Principles Section 1 7 ...
Page 47: ...20 Basic Procedures Section 2 ...
Page 139: ...112 Examples of Parameter Settings Section 4 9 ...
Page 173: ...146 Transferring Data with CX Position Section 5 7 ...
Page 223: ...196 Sample Program Section 7 7 ...
Page 259: ...232 Sample Program Section 8 10 ...
Page 293: ...266 Easy Backup Function Ver 2 0 or later Section 9 11 ...
Page 369: ...342 Reading Error Information with CX Position Section 11 8 ...
Page 385: ...358 Common Parameter Area Appendix C ...