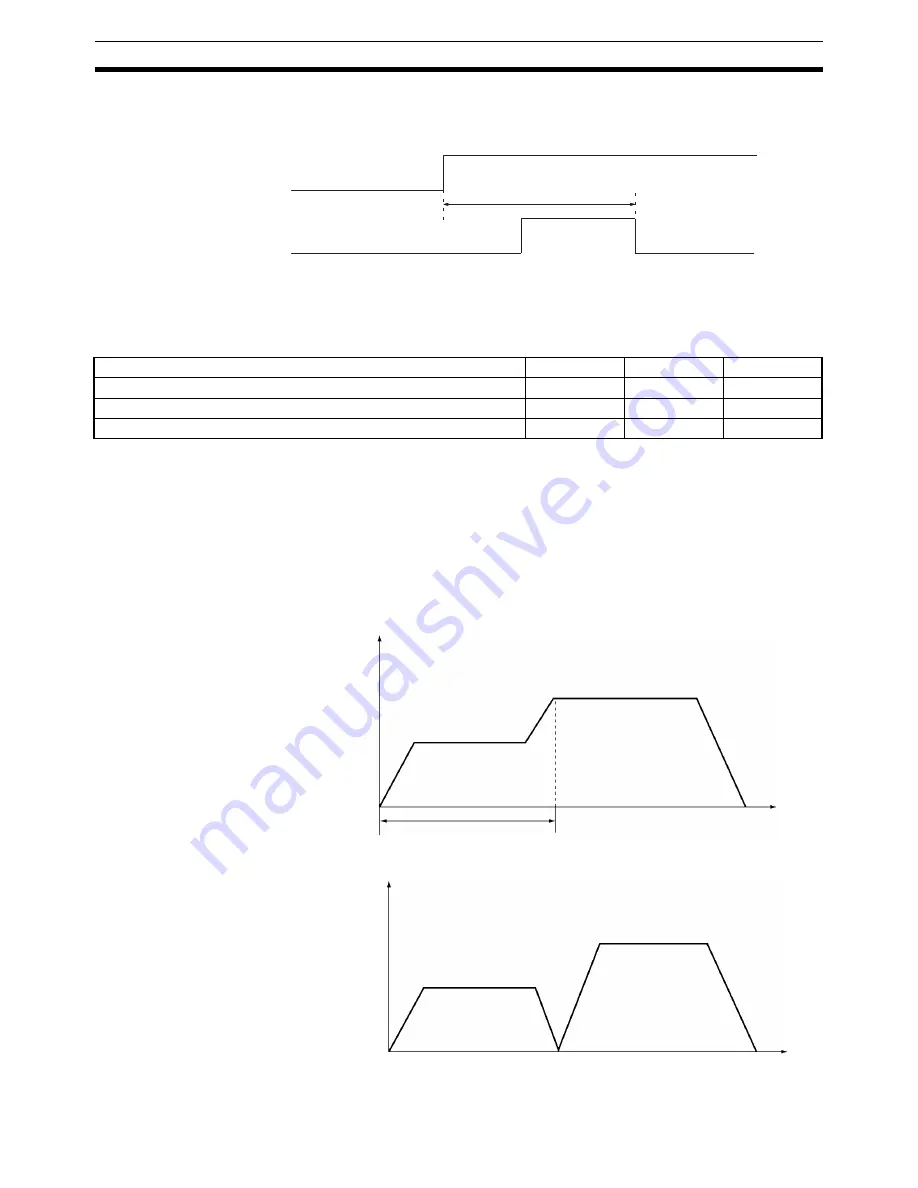
350
Performance Characteristics
Appendix A
Although the average data saving time is 300 ms, it may be as long as 33 s in some cases. If it is longer than
33 s, a flash memory error (error code 9300) will be generated, and the data saving operation will be inter-
rupted.
Effect on the Programmable Controller Cycle Time
The PLC’s cycle time increases if Units are added, or if the IOWR or IORD instructions are executed. The times
by which the cycle time will increase are shown in the following table.
Minimum Operation Time
The minimum operation time for the Position Control Unit is 10 ms. With memory operation, when a sequence
with a “continuous” completion code is executed and the positioning time for that sequence is shortened
according to the amount of movement and the target speed, the operation time required for the continuous
completion cannot be assured and positioning will be executed as if the completion code were “automatic.”
When using a sequence with a “continuous” completion code, be sure to adjust the target speed and target
position so that the operation time will be equal to or greater than the minimum operation time.
• Sequence operation time
≥
Minimum operation time
• Sequence operation time <
Minimum operation time
Operation
NC1
@
3
NC2
@
3
NC4
@
3
Time increase for each Unit mounted
0.29 ms
0.32 ms
0.41 ms
Time increase for each execution of the IOWR instruction (max. value)
0.7 ms
0.7 ms
0.6 ms
Time increase for each execution of the IORD instruction (max. value)
0.7 ms
0.7 ms
0.6 ms
SAVE DATA Bit
Data Transferring Flag
Data saving time
Speed
Sequence n
Sequence n+1
Sequence n operation time
Time
Speed
Sequence n
Sequence n+1
Time
Summary of Contents for CJ1W-C113 - REV 02-2008
Page 2: ...CJ1W NC113 213 413 133 233 433 Position Control Units Operation Manual Revised February 2008 ...
Page 3: ...iv ...
Page 13: ...xiv ...
Page 15: ...xvi ...
Page 19: ...xx ...
Page 27: ...xxviii Conformance to EC Directives 6 ...
Page 43: ...16 Control System Principles Section 1 7 ...
Page 47: ...20 Basic Procedures Section 2 ...
Page 139: ...112 Examples of Parameter Settings Section 4 9 ...
Page 173: ...146 Transferring Data with CX Position Section 5 7 ...
Page 223: ...196 Sample Program Section 7 7 ...
Page 259: ...232 Sample Program Section 8 10 ...
Page 293: ...266 Easy Backup Function Ver 2 0 or later Section 9 11 ...
Page 369: ...342 Reading Error Information with CX Position Section 11 8 ...
Page 385: ...358 Common Parameter Area Appendix C ...