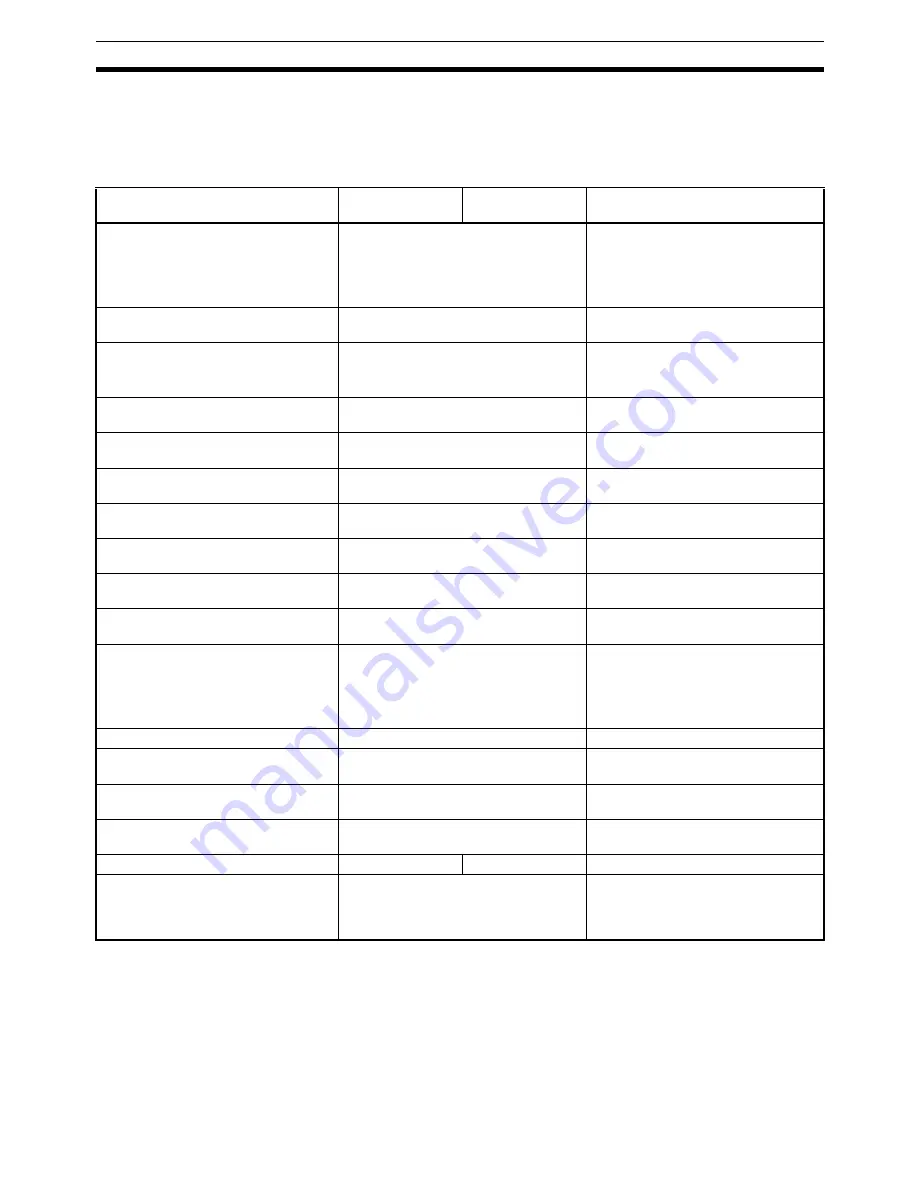
13
Comparison with Existing Models
Section 1-6
1-6
Comparison with Existing Models
The differences between the CJ1W-NC4
@
3/2
@
3/1
@
3 Position Control Units
and CS1W-NC4
@
3/2
@
3/1
@
3 and C200HW-NC413/213/113 Position Control
Units are given in the following table.
Item
CJ1W-NC4
@
3/
2
@
3/1
@
3
CS1W-NC4
@
3/
2
@
3/1
@
3
C200HW-NC413/213/113
Unit number allocation
Allocate unit numbers in the range 0 to
95.
1-axis and 2-axis PCUs: One unit num-
ber allocated
4-axis PCUs: 2 unit numbers allocated
Allocate unit numbers in the range 0 to
15.
1-axis and 2-axis PCUs: One unit
number allocated
4-axis PCUs: 2 unit numbers allocated
Pulse output type
2 types: open collector output and line
driver output
Open collector output only
Format of data exchanged between
PLC and PCU
Binary format (hexadecimal)
Example: Present position is output to
the PLC in 32-bit signed binary format.
BCD format
Example: Present position is output to
the PLC in BCD format.
Position designation range
–1,073,741,823 to 1,073,741,823
pulses
–9,999,999 to 9,999,999 pulses
Present position range
–2,147,483,647 to 2,147,483,647
pulses
–9,999,999 to 9,999,999 pulses
Zone range
–1,073,741,823 to 1,073,741,823
pulses
–9,999,999 to 9,999,999 pulses
Speed designation range
1 to 500,000 pps, set in pps units
1 to 500,000 pps, set in units of the
smallest multiplication factor specified
CPU Unit scan timeover for END
refresh
0.5 ms max. per PCU
2.6 to 4.5 ms per PCU
CPU Unit scan timeover due to IOWR/
IORD instruction
1 ms max. per instruction
2.4 to 62 ms per instruction
Time between startup instruction from
the ladder program and pulse output
2 ms max. (at optimum conditions)
7.51 ms max. (at optimum conditions)
Operating data area
The following 3 areas can be specified:
DM Area words allocated to Special I/O
Units, user-specified DM Area words,
and user-specified EM Area words.
The following 2 areas can be speci-
fied: User-specified DM Area words
and user-specified EM Area words.
(The DM Area words allocated to Spe-
cial I/O Units cannot be specified.)
Corresponding EM banks
Banks 0 to C
Bank 0 only
Clearing error codes
Possible
Not possible (only cleared to 0 when
startup instruction is made)
Parameter setting
Settings only required for the axes being
used.
Settings required for all axes.
Mounting on C200H Slave Rack
(remote I/O)
Not possible
Possible
External I/O connector
40 pins
48 pins
48 pins
Support Software
CX-Position
(Conversion of parameters and data
created using the SYSMAC-NCT possi-
ble.)
SYSMAC-NCT
Summary of Contents for CJ1W-C113 - REV 02-2008
Page 2: ...CJ1W NC113 213 413 133 233 433 Position Control Units Operation Manual Revised February 2008 ...
Page 3: ...iv ...
Page 13: ...xiv ...
Page 15: ...xvi ...
Page 19: ...xx ...
Page 27: ...xxviii Conformance to EC Directives 6 ...
Page 43: ...16 Control System Principles Section 1 7 ...
Page 47: ...20 Basic Procedures Section 2 ...
Page 139: ...112 Examples of Parameter Settings Section 4 9 ...
Page 173: ...146 Transferring Data with CX Position Section 5 7 ...
Page 223: ...196 Sample Program Section 7 7 ...
Page 259: ...232 Sample Program Section 8 10 ...
Page 293: ...266 Easy Backup Function Ver 2 0 or later Section 9 11 ...
Page 369: ...342 Reading Error Information with CX Position Section 11 8 ...
Page 385: ...358 Common Parameter Area Appendix C ...