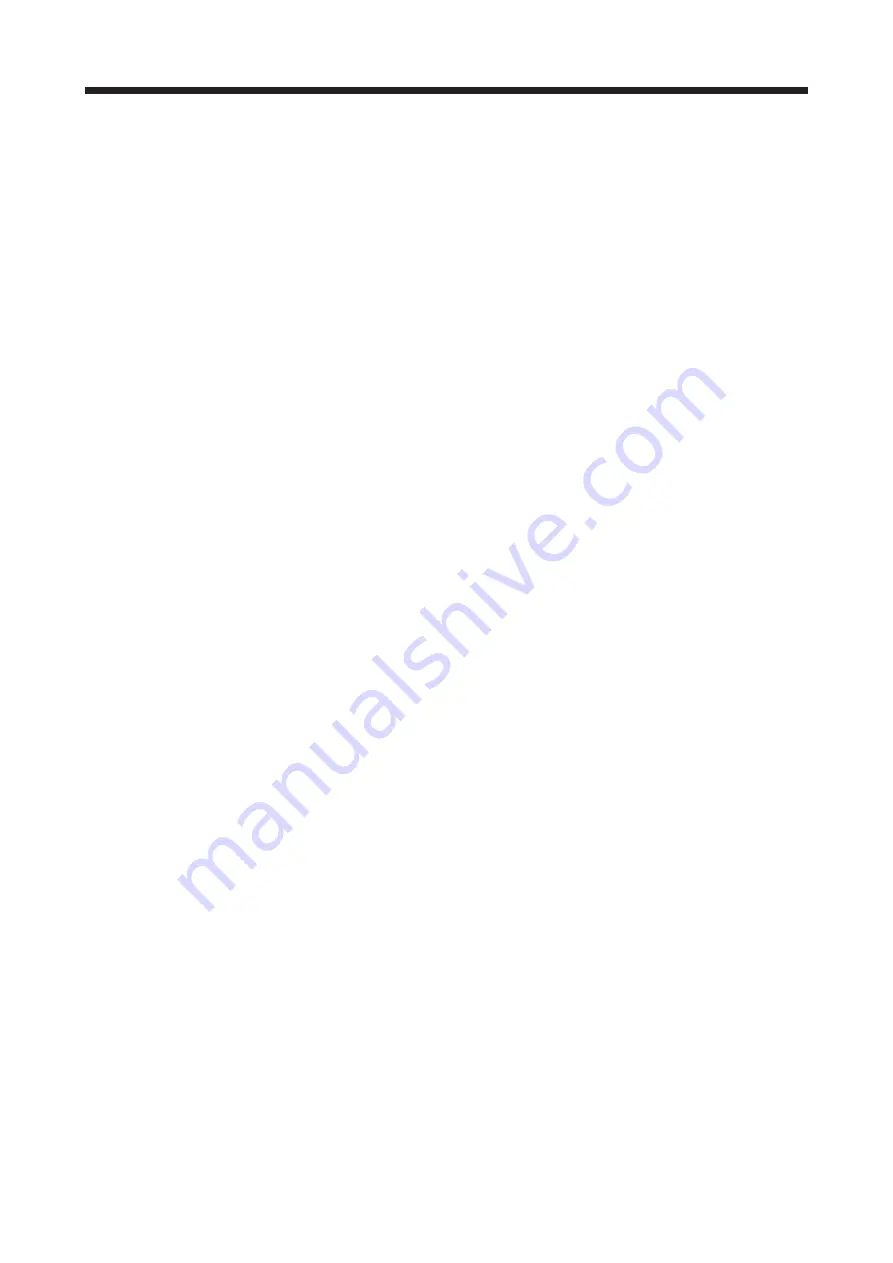
Part 5: Review on Replacement of MR-J3-DU_ with MR-J4-DU_
5 - 71
Note 1. For the power supply specifications, refer to "Part 6: Common Reference Material".
2. Use a magnetic contactor with an operation delay time (interval between current being applied to the coil until closure of
contacts) of 80 ms or less. Depending on the main circuit voltage and operation pattern, bus voltage decreases, and that may
cause the forced stop deceleration to shift to the dynamic brake deceleration. When dynamic brake deceleration is not
required, slow the time to turn off the magnetic contactor.
3. P1 and P2 are connected by default. When using the power factor improving DC reactor, connect P1 and P2 after removing
the short bar across them. Refer to "Part 8: Chapter 7" for details.
4. Connect P/+ and N/- terminals of the brake unit to a correct destination. Incorrect connection destination results in the
converter unit and brake unit malfunction.
5. For 400 V class, a step-down transformer is required.
6. Contact rating: 1a contact, 110 V AC, 5 A/220 V AC, 3 A
Normal condition: TH1-TH2 is not conducting. Abnormal condition: TH1-TH2 is conducting.
7. Contact rating: 230 V AC, 0.3 A/30 V DC, 0.3 A
Normal condition: B-C is conducting./A-C is not conducting. Abnormal condition: B-C is not conducting./A-C is conducting.
8. Install an overcurrent protection device (molded-case circuit breaker or fuse) to protect the branch circuit. (Refer to section
7.3.)
9. Do not connect more than one cable to each L+ and L- terminals of TE2-1 of the converter unit.
10.
Always connect BUE and SD terminals. (factory-wired)
11. Connect MSG and SD terminals of the brake unit to a correct destination. Incorrect connection destination results in the
converter unit and brake unit malfunction.
12. For connecting L+ and L- terminals of the converter unit to the terminal block, use the cable indicated in (4) in this section.
13. Configure a circuit to turn off EM2 in the drive unit when the main circuit power is turned off to prevent an unexpected restart of
the drive unit.
14. The wiring is for MR-J4-DU_B_(-RJ). The connection for the interface of MR-J4-DU_(-RJ) is the same as in the case of MR-J4-
_(-RJ). Refer to each servo amplifier instruction manual.
Summary of Contents for Melservo MR-J3-100B
Page 17: ...8 MEMO ...
Page 18: ...Part 1 Summary of MR J3 MR J3W Replacement 1 1 Part 1 Summary of MR J3 MR J3W Replacement ...
Page 145: ...Part 3 Review on Replacement of MR J3 _B_ with MR J4 _B_ 3 48 MEMO ...
Page 195: ...Part 4 Replacement of MR J3W _B with MR J4W2 _B 4 50 MEMO ...
Page 277: ...Part 5 Review on Replacement of MR J3 DU_ with MR J4 DU_ 5 82 MEMO ...
Page 278: ...Part 6 Common Reference Material 6 1 Part 6 Common Reference Material ...
Page 418: ...Part 7 Review on Replacement of Motor 7 1 Part 7 Review on Replacement of Motor ...
Page 564: ...Part 9 Startup Procedure Manual 9 1 Part 9 Startup Procedure Manual ...
Page 567: ...Part 9 Startup Procedure Manual 9 4 MEMO ...
Page 589: ...L NA 03127ENG C ...