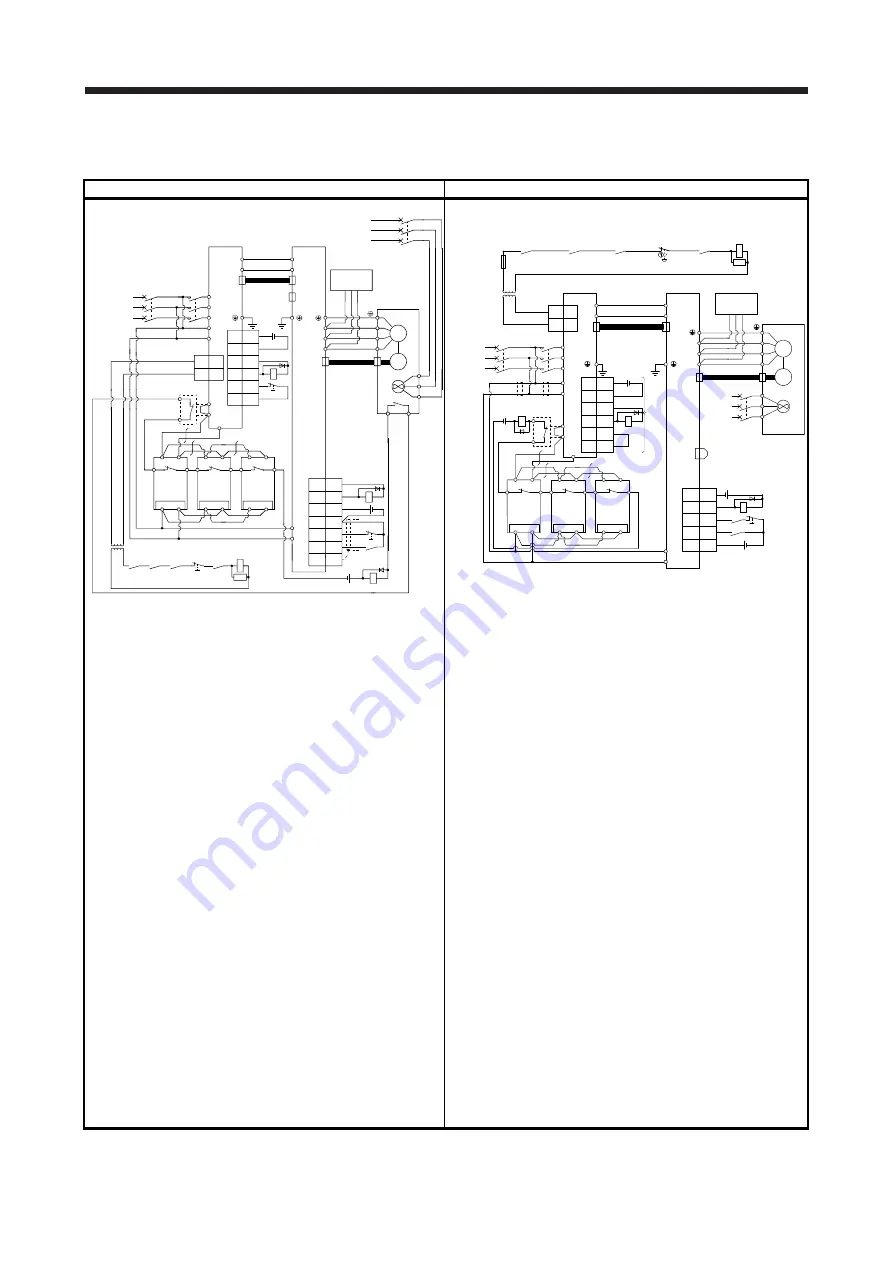
Part 5: Review on Replacement of MR-J3-DU_ with MR-J4-DU_
5 - 14
(2) 400 V class
(a) MR-J3-DU_A4/MR-J4-DU_A4
MR-J3-DU_A4 MR-J4-DU_A4
Emergency stop
(Note 3)
(EMG/EM1)
RA1
RA2
RA3
-ready
OFF/ON
MC
SK
MC
(Note 6)
NFB
(Note 3)
RA2
(Note 4)
Stepdown
L+
L-
transformer
L
1
L
2
L
3
L
11
L
21
1
MC1
2
MC2
3-phase
380 to 480 V AC
50/60 Hz
CN40
CN40A
CN2
BW
BV
BU
M
OHS2
V
U
W
CN40B
V
U
W
Servo motor
L+
L-
TE2-2
TE2-1
C
L
11
L
21
C
P
R400S400
CNP1
CN1
46
EMG
42
SON
DICOM
21
ALM
48
DOC O M
20
DICOM
SD
15
Plate
CN1
1
DICOM
5
6
DOC OM
DICOM
2
7
ALM
9
EM1
DOC OM
P
1
P
2
(Note 2)
24 V DC
24 V DC
(Note 5)
Power
supply
NFB
OHS1
24 V DC
RA3
(Note 3)
RA1
Converter unit
Drive unit
connector
Termination
MR-J3-TM
(Option)
cable
MR-J3CDL05M
External
dynamic brake
(Option)
Encoder
Cooling fan
Encoder cable
Servo
motor
thermal
relay
Converter
unit trouble
Servo motor
thermal relay
Operation
Drive
Power factor improving
DC reactor (Option)
unit trouble
Regenerative
G4
G3
option(Note 1)
C
P
Cooling fan
R400S400
Regenerative
G4
G3
C
P
option(Note 1)
Cooling fan
R400S400
Regenerative
G4
G3
option(Note 1)
Cooling fan
(Note 7)
MC
MCCB
RA2
L+
L-
L1
L2
L3
L11
L21
CN40
CN40A
M
V
U
W
V
U
W
TE2-2
L+
L-
TE2-1 (Note 15)
C
P1
P2
L11
L21
G4
G3
P
C
G4
G3
P
C
S400
R400
G4
G3
P
C
S400
R400
S400
R400
CN1
1
DICOM
5
DOCOM
6
DICOM
2
ALM
7
EM1
9
DOCOM
CN1
15
21
46
48
42
BW
BV
BU
MCCB
RA3
RA1
RA2
MC
SK
1
MC1
2
MC2
CNP1
(Note 3)
Step-down
transformer
RA3
CN8
Optional
thermal
Operation ready
OFF/ON
Drive unit
malfunction
Emergency stop
switch
(Note 5)
(Note 1)
Regenerative
option
MR-J3CDL05M
cable
Drive unit
3-phase
380 V AC to
480 V AC
(Note 12)
CN2
External
dynamic brake
(
optional
)
Encoder
Servo motor
(Note 4)
Power
supply
Power factor improving
DC reactor (
optional
)
(Note 2)
Cooling fan
(Note 1)
Regenerative
option
Cooling fan
(Note 1)
Regenerative
option
Cooling fan
(Note 8) Encoder cable
24 V DC
Cooling fan
(Note 7, 15)
24 V DC
(Note 11)
Short-circuit connector
(packed with the drive unit)
(Note 12)
(Note 9)
(Note 13)
(Note 10)
(Note 10)
Resistance regeneration
converter unit
Converter unit
malfunction
EM2
ALM
DICOM
DOCOM
SON
24 V DC
(Note 6)
Main circuit power supply
RA1
24 V DC
Note 1. For the MR-RB138-4. For the MR-RB138-4, three units are used as one
set (permissible wattage: 3900W).
Note 1. This is for MR-RB13V-4. For the MR-RB13V-4, three units are used as
one set (permissible regenerative power: 3900 W).
2. When using the Power factor improving DC reactor, disconnect the short
bar across P1 and P2.
2. P1 and P2 are connected by default. When using the power factor
improving DC reactor, connect P1 and P2 after removing the short bar
across them. Refer to "Part 8: section 7.3" for details.
3.
Make up a sequence that will concurrently turn off the Emergency stop
(EMG) of the drive unit and the Forced stop (EM1) of the converter unit,
and shut off the main circuit power supply by the external sequence.
3.
A step-down transformer is required when the coil voltage of the magnetic
contactor is 200 V class.
4. Stepdown transformer is required for coil voltage of magnetic contactor
more than 200V class.
4. For specifications of the cooling fan power supply, refer to "Servo Motor
Instruction Manual (Vol. 3)".
5. For specifications of cooling fan power supply, refer to "MR-J3-_A_ Servo
amplifier instruction manual".
5. Use a magnetic contactor with an operation delay time (interval between
current being applied to the coil until closure of contacts) of 80 ms or less.
The bus voltage decreases depending on the main circuit voltage and
operation pattern, which may cause the forced stop deceleration to shift to
the dynamic brake deceleration. When dynamic brake deceleration is not
required, slow the time to turn off the magnetic contactor.
6.
Be sure to use a magnetic contactor with an operation delay time of 80ms or
less. The operation delay time is the time interval between current being
applied to the coil until closure of contacts.
7. Use an external dynamic brake for the drive unit. Failure to do so will
cause an accident because the servo motor does not stop immediately
but coasts at an emergency stop and such conditions. Ensure the safety
in the entire system.
6. To prevent an unexpected restart of the drive unit, configure a circuit to
turn off EM2 in the drive unit when the main circuitpower is turned off.
7. Use an external dynamic brake for the drive unit. Failure to do so will
cause an accident because the servo motor does not stop immediately but
coasts at an alarm occurrence for which the servo motor does not
decelerate to stop. Ensure the safety in the entire equipment. For alarms
for which the servo motor does not decelerate to stop and for wiring of the
external dynamic brake, refer to "MR-CV_/MR-CR55K_/MR-J4-DU_(-RJ)
instruction manual".
8. For the encoder cable, use of the option cable is recommended. For
selecting cables, refer to "Servo Motor Instruction Manual (Vol. 3)".
9. This diagram shows sink I/O interface. For source I/O interface, refer to
"MR-CV_/MR-CR55K_/MR-J4-DU_(-RJ) instruction manual".
10. Install an overcurrent protection device (molded-case circuit breaker or
fuse) to protect the branch circuit. (Refer to section 7.3.)
11. When not using the STO function, attach the short-circuit connector
supplied with the drive unit.
12. Do not connect the servo motor of a wrong axis to U, V, W, or CN2 of the
drive unit. Otherwise, a malfunction may occur.
13. For connecting servo motor power wires, refer to "Servo Motor Instruction
Manual (Vol. 3)".
14. For the MR-J4-DU30K_4(-RJ) and MR-J4-DU37K_4(-RJ), the terminal
block is TE2.
15. The external dynamic brake cannot be used for compliance with SEMI-F47
standard. Do not assign DB. Failure to do so will cause the drive unit to
become servo-off when an instantaneous power failure occurs.
Summary of Contents for Melservo MR-J3-100B
Page 17: ...8 MEMO ...
Page 18: ...Part 1 Summary of MR J3 MR J3W Replacement 1 1 Part 1 Summary of MR J3 MR J3W Replacement ...
Page 145: ...Part 3 Review on Replacement of MR J3 _B_ with MR J4 _B_ 3 48 MEMO ...
Page 195: ...Part 4 Replacement of MR J3W _B with MR J4W2 _B 4 50 MEMO ...
Page 277: ...Part 5 Review on Replacement of MR J3 DU_ with MR J4 DU_ 5 82 MEMO ...
Page 278: ...Part 6 Common Reference Material 6 1 Part 6 Common Reference Material ...
Page 418: ...Part 7 Review on Replacement of Motor 7 1 Part 7 Review on Replacement of Motor ...
Page 564: ...Part 9 Startup Procedure Manual 9 1 Part 9 Startup Procedure Manual ...
Page 567: ...Part 9 Startup Procedure Manual 9 4 MEMO ...
Page 589: ...L NA 03127ENG C ...