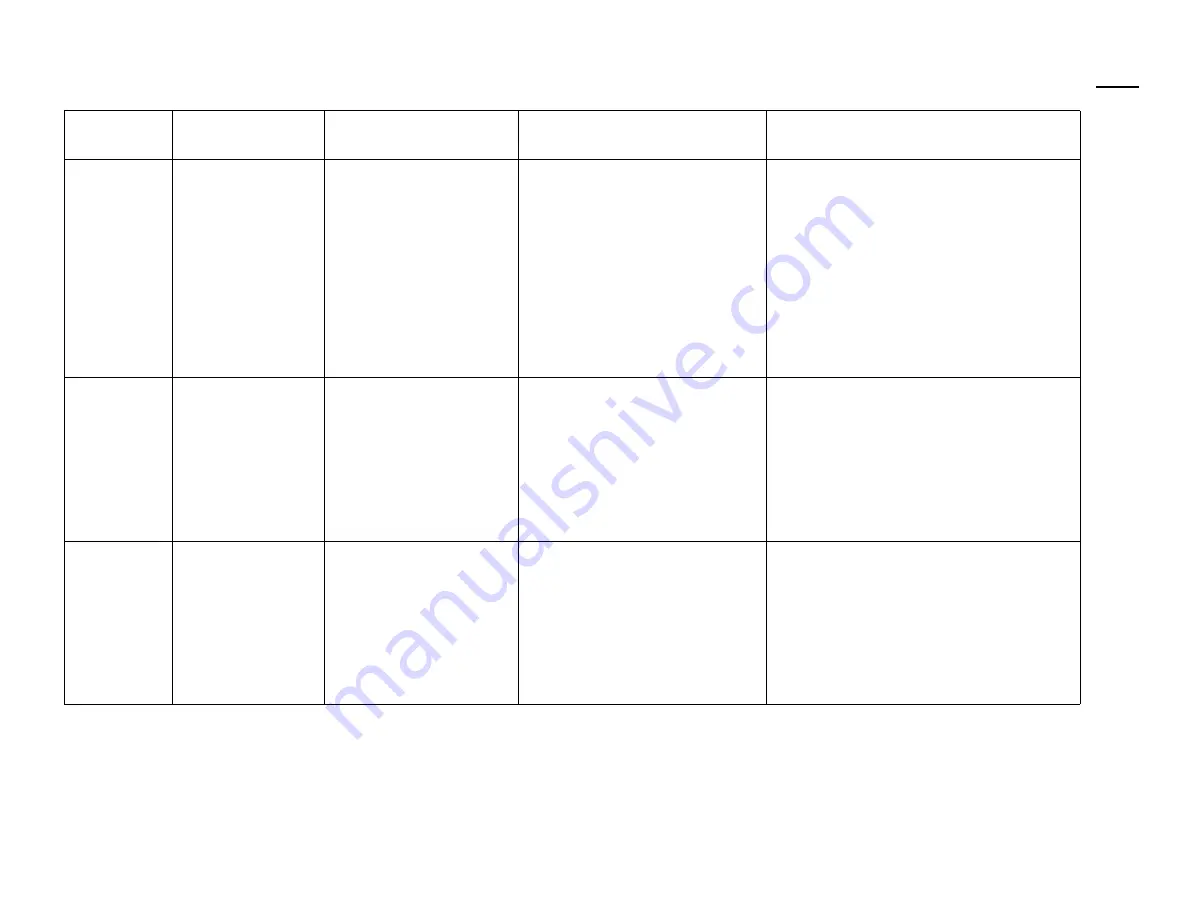
A13
9
14
AF
12
-1
8
Tro
u
blesho
o
ting Cal
ibr
a
tio
n a
n
d Result
E
rro
rs
Comm
on Er
ro
r Me
ss
ages
and
C
o
rr
ec
tiv
e
Act
ion
s
0x02680002
4
CC Sample Obstruction
Error
Sample ID:
Rack ID:
Rack Position:
CAU:
CC Sample Obstruction
Message ID:
0x02680002
Subsystem:
RASched
Sample ID:
Rack ID:
Position:
This error occurs when an obstruction is
detected on a second aspirate attempt
of the same sample.
•
Check specified sample for clots. Remove clots
and rerun.
•
Check sample volume.
•
If Nesting cup used, make sure rack is reserved.
Refer to
Assigning or Reassigning Reserved
•
If multiple obstruction errors occur, flush probe.
Refer to
Flush the Sample and Reagent Probe
•
Check tubing from top of probe to ODC sensor
for crimps. If crimped, tubing will need to be
replaced.
0x02680003
4
Sample tube did not
vent correctly. Remove
cap and reload tube.
Sample ID:
sample id
Rack:
rack id
Position:
rack position
CC Sample Probe
CAU:
CC Sample Tube Excess
Vacuum Error
Message ID:
0x02680003
Subsystem:
RASched
Sample ID:
sample id
Rack ID:
rack id
Rack Position:
rack position
Probe detected excessive vacuum in
thick stopper closed tube on second
attempt. Sample is aborted.
•
Uncap tube and rerun.
•
If occurs consistently for many samples, check
cap piercer for broken blade. Refer to
CTS Blade/Wick (1-Blade Thick CTS Option)
or
Replace CTS Blade (1-Blade Narrow CTS Option)
to inspect the blade.
•
Perform CC ODC Alignment.
0x02680004
4
Sample tube did not
vent correctly. Remove
cap and reload tube.
Sample ID:
sample id
Rack:
rack id
Position:
rack position
CC Sample Probe
CAU:
CC Sample Tube Excess
Pressure Error
Message ID:
0x02680004
Subsystem:
RASched
Sample ID:
sample id
Rack ID:
rack id
Rack Position:
rack position
Probe detected excessive pressure in
thick stopper closed tube on second
attempt. Sample is aborted.
•
Uncap tube and rerun.
•
If occurs consistently for many samples, check
cap piercer for broken blade. Refer to
CTS Blade/Wick (1-Blade Thick CTS Option)
or
Replace CTS Blade (1-Blade Narrow CTS Option)
to inspect the blade.
•
Perform CC ODC Alignment.
Table 12.10
Error Messages and Corrective Actions
(Continued)
ID
Class #
Pop-up
Event Log
Description
Corrective Action
Содержание UniCel DxC 600
Страница 4: ...A13914AF iv Revision History ...
Страница 26: ...A13914AF xxvi Safety Notice Documentation Symbols ...
Страница 36: ...A13914AF xxxvi Introduction How to Use this Manual ...
Страница 68: ...A13914AF 1 32 System Description Main Screen and Program Structure Figure 1 20 Program Structure QC Setup ...
Страница 71: ...A13914AF 1 35 System Description Main Screen and Program Structure 1 Figure 1 23 Program Structure Utils ...
Страница 132: ...A13914AF 3 34 System Setup Options Auto Generation of Control ...
Страница 190: ...A13914AF 5 26 Quality Control Review Archived Data ...
Страница 364: ...A13914AF 9 128 Maintenance As Needed As Required Maintenance ...
Страница 384: ...A13914AF 10 20 System Status and Commands Unload All ...
Страница 407: ......
Страница 490: ...A13914AF Glossary 10 Glossary ...
Страница 497: ......