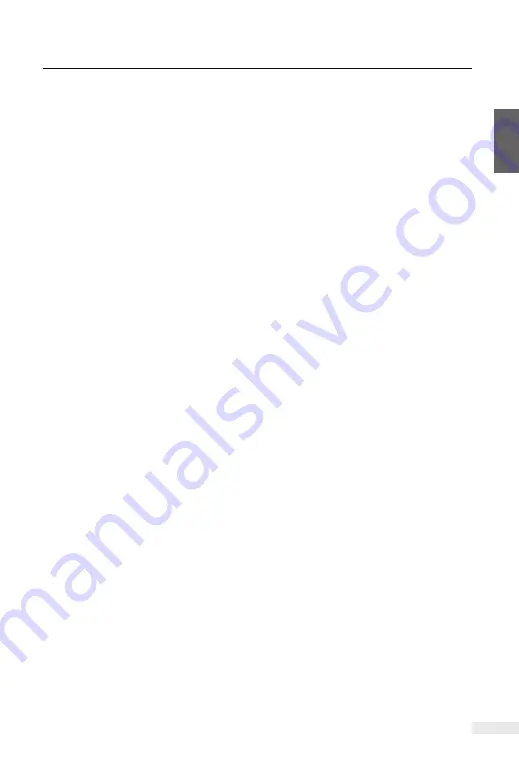
-9-
1.2 Use Considerations
1.2.1 Motor Insulation Inspection
When the motor is used for the first time or when the motor is reused after being
kept, or when periodical inspection is performed, insulation inspection shall be
conducted with motor so as to avoid damaging the inverter because of the
insulation failure of the motor windings. The motor wires must be disconnected
from the inverter during the insulation inspection. It is recommended to use the
500V mega meter, and the insulating resistance measured shall be 5M
Ω
at least.
1.2.2 Motor Thermal Protection
If the motor rating does not match that of the inverter, especially when the rated
power of the inverter is higher than that of the motor, adjust motor protection
parameters in the inverter or install thermal relay to protect motor.
1.2.3 Operating with the Frequency Higher than Grid Power Frequency
Output frequency of is 0.00Hz
~
500Hz. If
is required to operate above
50.00Hz, please take the endurance of mechanical devices into consideration.
product
1.2.4 Mechanical Vibrations
Inverter may encounter mechanical resonance point of the load device at certain
output frequencies which can be avoided by setting the skip frequency paramet
-
ers of the inverter.
1.2.5 Motor Heat and Noise
Since output voltage of inverter is PWM wave and contains a certain amount of
harmonics, so that the temperature, noise and vibration of the motor will be
higher than those when the inverter runs at grid power frequency.
1.2.6 Voltage-sensitive device or capacitor on output side of the AC drive
Do not install the capacitor for improving power factor or lightning protection
voltage-sensitive resistor on the output side of the AC drive because the output
of the AC drive is PWM wave. Otherwise, the AC drive may suffer transient
overcurrent or even be damaged.
1.2.7 Contactor at the I/O terminal of the AC drive
When a contactor is installed between the input side of the AC drive and the pow
-
er supply, the AC drive must not be started or stopped by switching the contactor
on or off. If the AC drive has to be operated by the contactor, ensure that the time
interval between switching is at least one hour since frequent charge and discha
-
rge will shorten the service life of the capacitor inside the AC drive
;
Chapter 1 Safety and Attentions
C
h
a
p
te
r
1
Summary of Contents for 2S-0.4G-B
Page 6: ...Safety and Attentions Chapter 1 1 1 Safety Matters 6 1 2 Use Considerations 9...
Page 80: ...Function Parameter Table 5 1 Functional group 78 Chapter 5...
Page 126: ...Function Parameter Table Chapter 6...
Page 245: ......
Page 249: ......
Page 255: ......