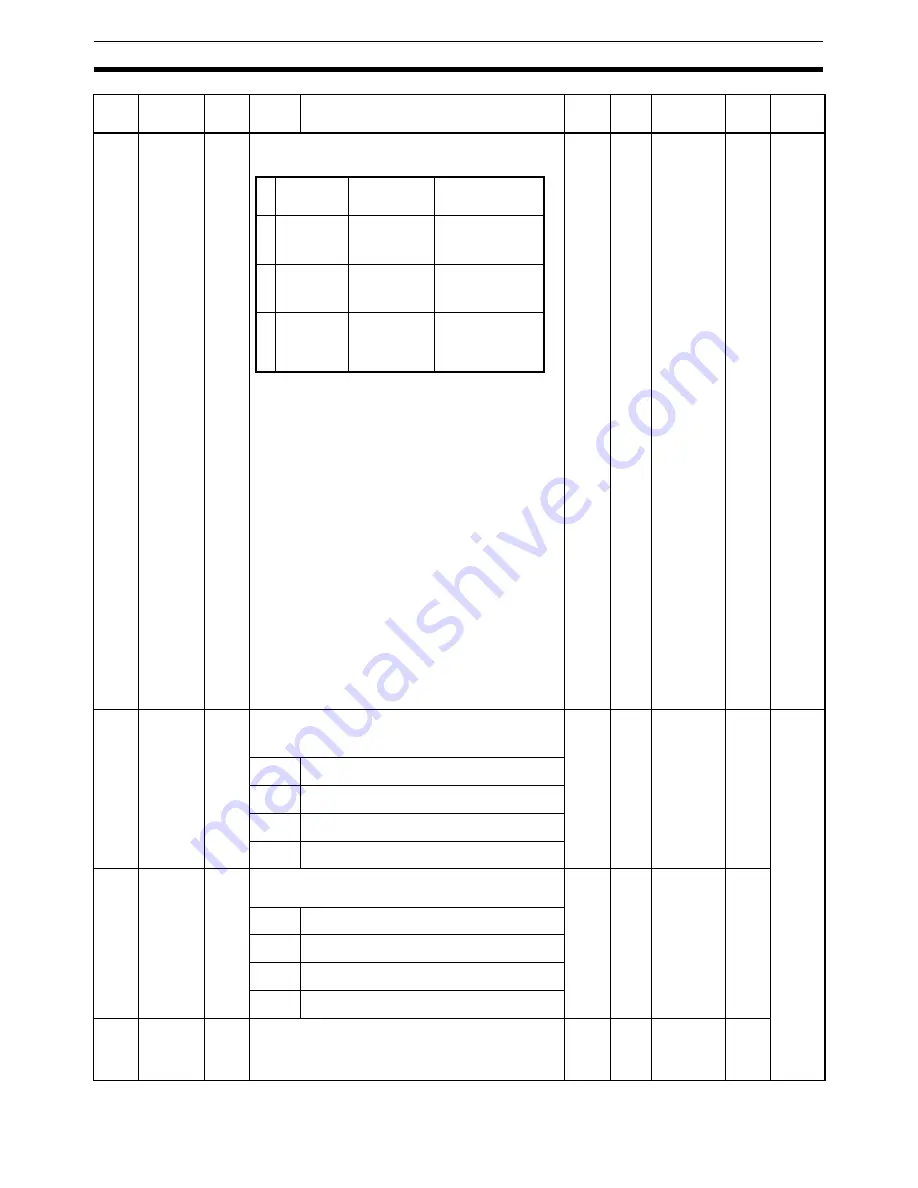
546
List of Parameters
Appendix B
Pn066
Stop Selec-
tion for
Drive Prohi-
bition
Input
2
Sets the deceleration stop operation to be performed after the For-
ward Drive Prohibit Input (POT) or Reverse Drive Prohibit Input
(NOT) is enabled.
Note 1.
The positioning command generation process (positioning
operation) within the Servo Drive will be forcibly stopped
once it enters the deceleration mode. Also, when the
deceleration mode is activated during speed control or
torque control, it will switch to position control. If a posi-
tioning operation command is received during decelera-
tion, the internal positioning command generation process
will be retained, and after deceleration is complete, posi-
tioning operation will be activated.
Note 2.
When the Servomotor rotation speed is 30 r/min or less
(stopped), the deceleration mode will not be activated
even if the drive prohibit input is enabled.
Note 3.
When the parameter is set to 2 and an operation com-
mand in the drive prohibited direction is received after
stopping, a command warning (warning code 95h) will be
issued. When the parameter is set to 0 or 1, the operation
command in the prohibited direction after stopping will be
accepted, but the Servomotor will not operate and the
position deviation will accumulate because the torque
command is 0. Take measures such as issuing a com-
mand in the reverse direction from the host controller.
Note 4.
When the parameter is set to 2, MECHATROLINK-II com-
munications are interrupted, and either Forward or
Reverse Drive Prohibit Input (POT or NOT) is turned ON,
receiving an operation command (jog operation or normal
mode autotuning) via RS232 will cause a Drive Prohibit
Input Error (alarm code 38). A Drive Prohibit Input Error
(alarm code 38) will also occur if either POT or NOT is
turned ON while operating on an operation command
received via RS232.
0
---
0 to 2
Offline
P067
Stop Selec-
tion with
Main Power
OFF
2
Sets the operation to be performed during deceleration and after
stopping after the main power supply is turned OFF with the Und-
ervoltage Alarm Selection (Pn065) set to 0. The deviation counter
will be reset when the power OFF is detected.
0
---
0 to 7
Online
Settings
can be
changed
when the
axes are
stopped
(Busy
Flag for
each axis
= 0).
0 and 4
Use dynamic brake to decelerate and remain stopped
with dynamic brake.
1 and 5
Use free-run to decelerate and remain stopped with
dynamic brake.
2 and 6
Use dynamic brake to decelerate, but free the motor
when stopped.
3 and 7
Use free-run to decelerate, and free the motor when
stopped.
Pn068
Stop Selec-
tion for
Alarm Gen-
eration
2
Sets the deceleration process and stop status after an alarm is
issued by the protective function. The deviation counter will be
reset when an alarm is issued.
0
---
0 to 3
Online
0
Use dynamic brake to decelerate and remain stopped
with dynamic brake.
1
Use free-run to decelerate and remain stopped with
dynamic brake.
2
Use dynamic brake to decelerate, but free the motor
when stopped.
3
Use free-run to decelerate, and free the motor when
stopped.
Pn069
Stop Selec-
tion with
Servo OFF
2
Sets the operational conditions to apply during deceleration and
after stopping when the Servo is turned OFF.
The relationship between set values, operation, and deviation
counter processing for this parameter is the same as for the Stop
Selection with Main Power OFF (Pn067).
0
---
0 to 7
Online
Param-
eter
No.
Parameter
name
Param-
eter
size
Setting
Explanation
Default
setting
Unit
Setting
range
Enable
setting
Details
During
deceleration
After stopping
(30 r/min or
less)
Deviation counter
0
Dynamic
brake
Disables torque
command in
drive prohibited
direction
Cleared while decel-
erating with dynamic
brake. Retained after
stopping.
1
Disables
torque
Disables torque
command in
drive prohibited
direction
Cleared while decel-
erating. Retained
after stopping.
2
Emergency
Stop Torque
(Pn06E)
Servo locked
Retained while decel-
erating, cleared upon
completion of decel-
eration, and retained
after stopping.
Summary of Contents for CJ1W-NC271 - 12-2009
Page 2: ......
Page 4: ...iv ...
Page 6: ...vi ...
Page 22: ...xxii ...
Page 58: ...30 Starting Operation Section 2 2 ...
Page 244: ...216 Axis Operating Input Memory Areas Section 4 8 ...
Page 264: ...236 Transferring Servo Parameters Section 5 3 ...
Page 396: ...368 Linear Interpolation Section 9 7 ...
Page 648: ...620 List of Error Codes Appendix D ...
Page 674: ...646 Additional Functions for the CJ1W NCF71 MA Appendix F ...
Page 684: ...656 Index ...
Page 686: ...658 Revision History ...