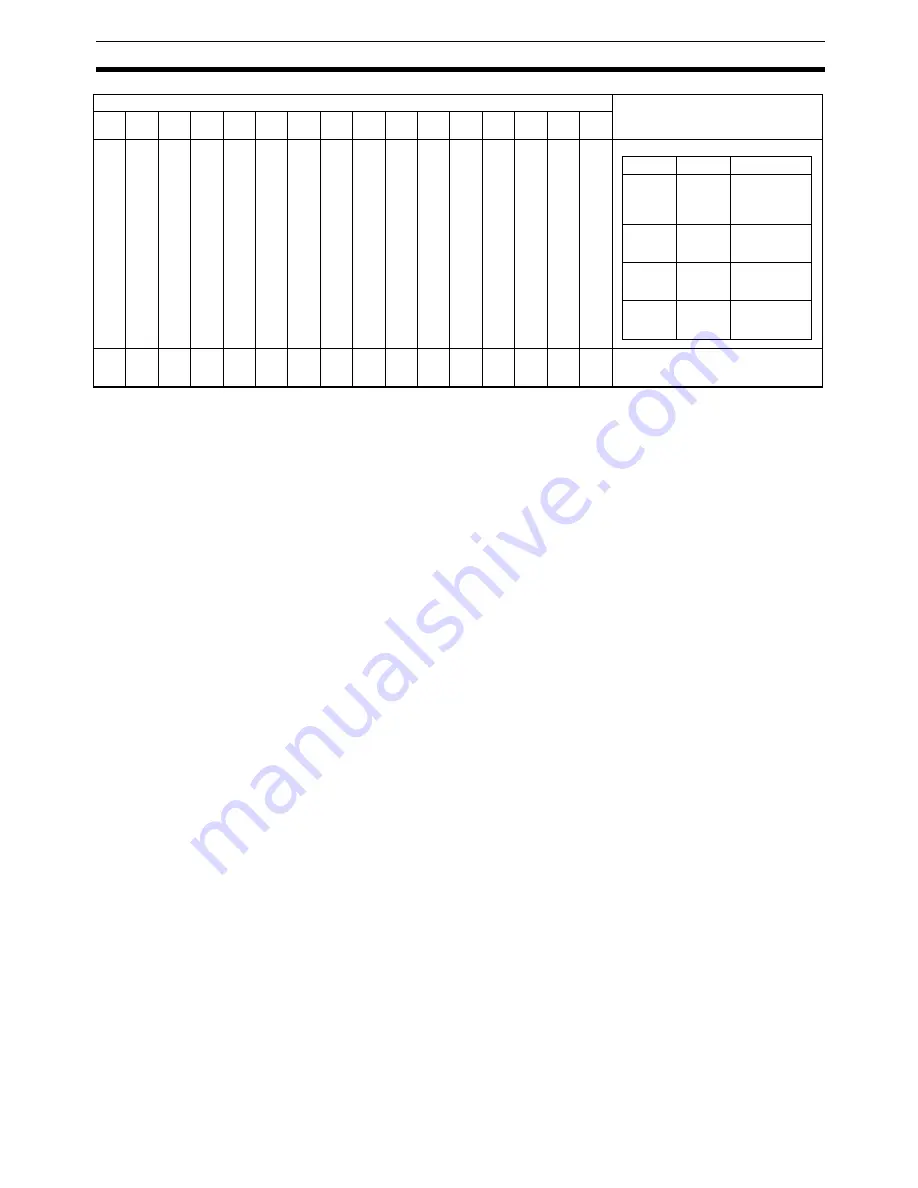
521
List of Parameters
Appendix B
Note
The reversal mode 3 setting for the origin search operation, the origin detection method, and the origin
search preset can be used only with Position Control Units with unit version 2.0 or later. They cannot be
used with Position Control Units with unit version 1.3 or earlier.
Servo Parameter Area
The Servo Parameters listed here can be used when the PCU is used with either an R88D-KN
@
-ML2 G5-
series Servo Drive, an R88D-GN
@
-ML2 G-series Servo Drive, OMRON R88D-WT
@
W-series Servo Drive
equipped with a FNY-NS115 MECHATROLINK-II I/F Unit, an W-series Servo Drive with built-in MECHA-
TROLINK-II communications (R88D-WN
@
-ML2), or a SMARTSTEP Junior Servo Drive with Built-in MECHA-
TROLINK-II Communications (R7D-ZN
@
-ML2).
For further details on each of the parameters, refer to the operation manuals for OMRON G5-series Servo
Drives, G-series Servo Drives, W-series Servo Drives and Yaskawa JUSP-NS115 MECHATROLINK-II I/F Unit.
G5-series Servo Drive (R88D-KN
@
-ML2 with Built-in MECHATROLINK-II
Communications)
This shows a list of Servo Parameters that can be used by the Position Control Unit of a G5-series Servo Drive
(R88D-KN
@
-ML2) with built-in MECHATROLINK-II communications.
For details on each parameter, refer to the user’s manual of the respective G5-series Servo Drives.
• Some parameters are enabled by turning the power supply OFF and then ON again. (Those parameters
are indicated in the table.)
After changing these parameters, turn OFF the power supply, confirm that the power supply indicator has
gone OFF, and then turn ON the power supply again.
• Do not change the parameters marked "Reserved for manufacturer use" and "Reserved".
Do not change the set values marked “Not used” and “Reserved”.
• For details about the data attributes, refer to the information below.
A: Enabled at all time.
B: Changes are prohibited during motor operation and issuing of commands.
The timing will fluctuate if a change is made during motor operation and issuing of commands.
C: Enabled after a power reset or executing the CONFIG command in MECHATROLINK-II communication.
R: Power reset.
Note that this is not enabled by the CONFIG command in MECHATROLINK-II communication.
1862 1876 188A 189E 18B2 18C6 18DA 18EE 1902 1916 192A 193E 1952 1966 197A 198E
Operation mode selection
Bit
Function
Settings
00 to 03
Encoder
type
0: Incremental
encoder
1: Absolute
encoder
04 to 07
Reserved
by the
system.
0
08 to 11
Reserved
by the
system.
0
12 to 15
Reserved
by the
system.
0
1863
to
1873
1877
to
1887
188B
to
189B
189F
to
18AF
18B3
to
18C3
18C7
to
18D7
18DB
to
18EB
18EF
to
18FF
1903
to
1913
1917
to
1927
192B
to
193B
193F
to
194F
1953
to
1963
1967
to
1977
197B
to
198B
198F
to
199F
0000 (Reserved by the system.)
PCU's internal address (hexadecimal)
Data
Axis
1
Axis
2
Axis
3
Axis
4
Axis
5
Axis
6
Axis
7
Axis
8
Axis
9
Axis
10
Axis
11
Axis
12
Axis
13
Axis
14
Axis
15
Axis
16
Summary of Contents for CJ1W-NC271 - 12-2009
Page 2: ......
Page 4: ...iv ...
Page 6: ...vi ...
Page 22: ...xxii ...
Page 58: ...30 Starting Operation Section 2 2 ...
Page 244: ...216 Axis Operating Input Memory Areas Section 4 8 ...
Page 264: ...236 Transferring Servo Parameters Section 5 3 ...
Page 396: ...368 Linear Interpolation Section 9 7 ...
Page 648: ...620 List of Error Codes Appendix D ...
Page 674: ...646 Additional Functions for the CJ1W NCF71 MA Appendix F ...
Page 684: ...656 Index ...
Page 686: ...658 Revision History ...