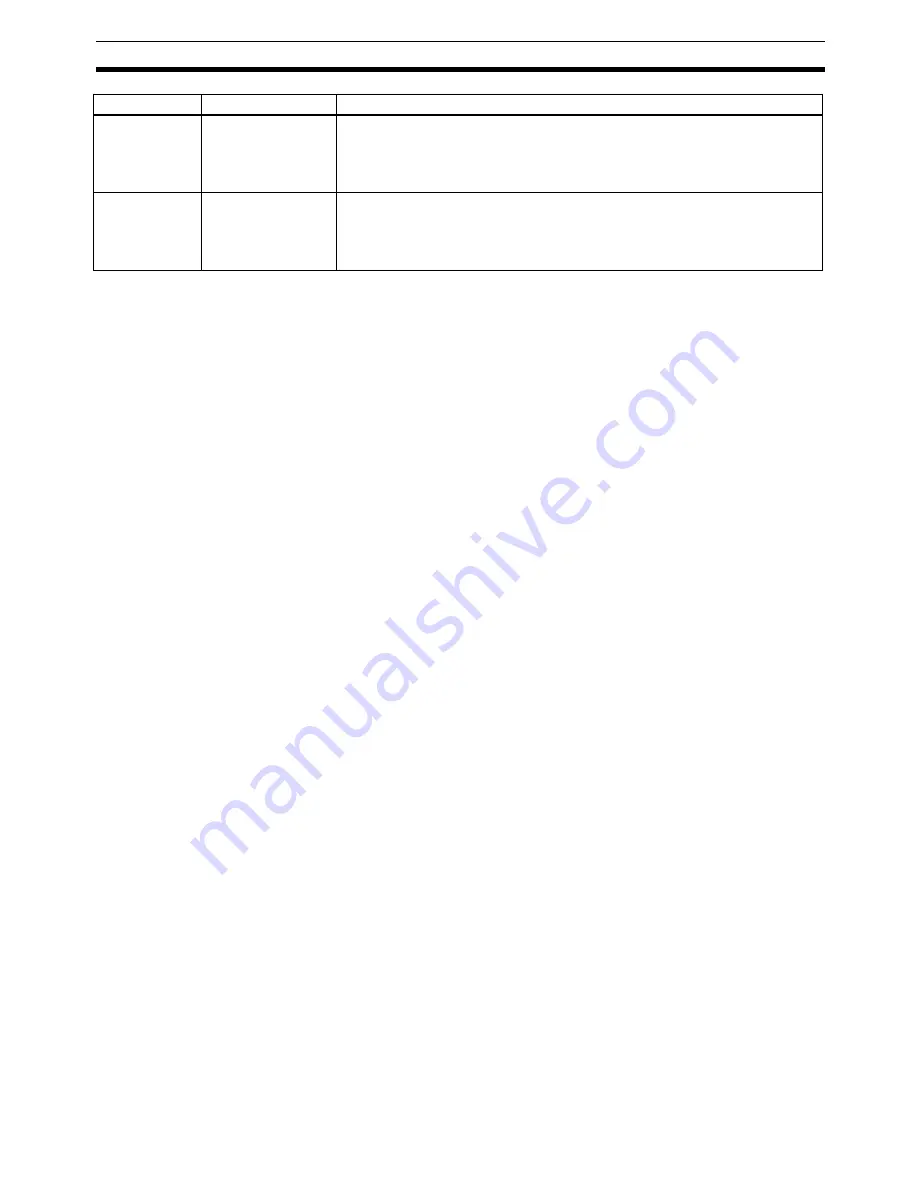
469
Application Examples
Section 11-3
The setting value in D1002 and D1003 is used as the speed command value
in position and speed control. In torque control, it is used as the speed limit
value.
The PCU's speed command value for speed control and the speed limit value
for torque control (option command value 1) are set as a percentage of the
Servomotor's momentary maximum rotation speed (units: 0.001%), so they
are calculated as follows in this program.
Use the following equation as a template and change the equation in this pro-
gram when the Servomotor's momentary maximum rotation speed, encoder
resolution, or electronic gear ratio are different.
Speed command value for speed control and speed limit value for torque
control = Speed command value (command units/s)
×
60 (s) / (Servomotor
momentary maximum rotation speed (r/min)
×
Encoder resolution (pulses/
rotation)
×
4/Electronic gear ratio)/0.001%
An R88M-W10030L W-series Servomotor is used in this sample program. In
this case,
Momentary maximum rotation speed:5,000 r/min
Encoder resolution:
2,048 pulses/rotation
The electronic gear ratio is contained in Servo Parameters (Pn202/Pn203)
and the default setting is 4 (Pn202 = 4 and Pn203 = 1).
Consequently, the units calculation is as follows:
Speed command value for speed control and speed limit value for torque
control
= Speed command value (command units/s)
×
60/ (5,000
×
2,048
×
4/4)
×
100,000
= Speed command value (command units/s)
×
6,000,000 / 10,240,000
In this program, the fraction is reduced to 1,200/2,048 to prevent the multipli-
cation or division from overflowing.
Note
When torque control is being performed, option command value 1 is used as
the speed limit value, so set parameter Pn002.1 (Speed command input
change) to 1 to select option command value 1.
If the Servo Unlock function is executed during speed control or torque con-
trol, this program will output the Servo Unlock command after executing an
Emergency Stop (see the output circuit for W305.06).
In addition, the feedback speed and torque command are monitored in this
program with the PCU's Expanded Monitoring function.
Since the speed and torque units used for monitoring depend on the control
mode (position control, speed control, or torque control), the monitoring units
are converted in this program and output to D1020 to D1021 and D1022 to
D1023. Refer to
4-8-6 Expanded Monitoring
for details on the monitoring units
used in each control mode.
D1010
Axis 1 Acceleration
Constant
This word contains the acceleration constant for positioning.
If CIO 0500.14 is ON when positioning is started, the contents of this word are
written to the Servo Parameter to change the acceleration rate.
Set in units of “
×
10,000 command units/s
2
.”
D1011
Axis 1 Deceleration
Constant
This word contains the deceleration constant for positioning.
If CIO 0500.15 is ON when positioning is started, the contents of this word are
written to the Servo Parameter to change the deceleration rate.
Set in units of “
×
10,000 command units/s
2
.”
Word/bit
Function
Explanation
Summary of Contents for CJ1W-NC271 - 12-2009
Page 2: ......
Page 4: ...iv ...
Page 6: ...vi ...
Page 22: ...xxii ...
Page 58: ...30 Starting Operation Section 2 2 ...
Page 244: ...216 Axis Operating Input Memory Areas Section 4 8 ...
Page 264: ...236 Transferring Servo Parameters Section 5 3 ...
Page 396: ...368 Linear Interpolation Section 9 7 ...
Page 648: ...620 List of Error Codes Appendix D ...
Page 674: ...646 Additional Functions for the CJ1W NCF71 MA Appendix F ...
Page 684: ...656 Index ...
Page 686: ...658 Revision History ...