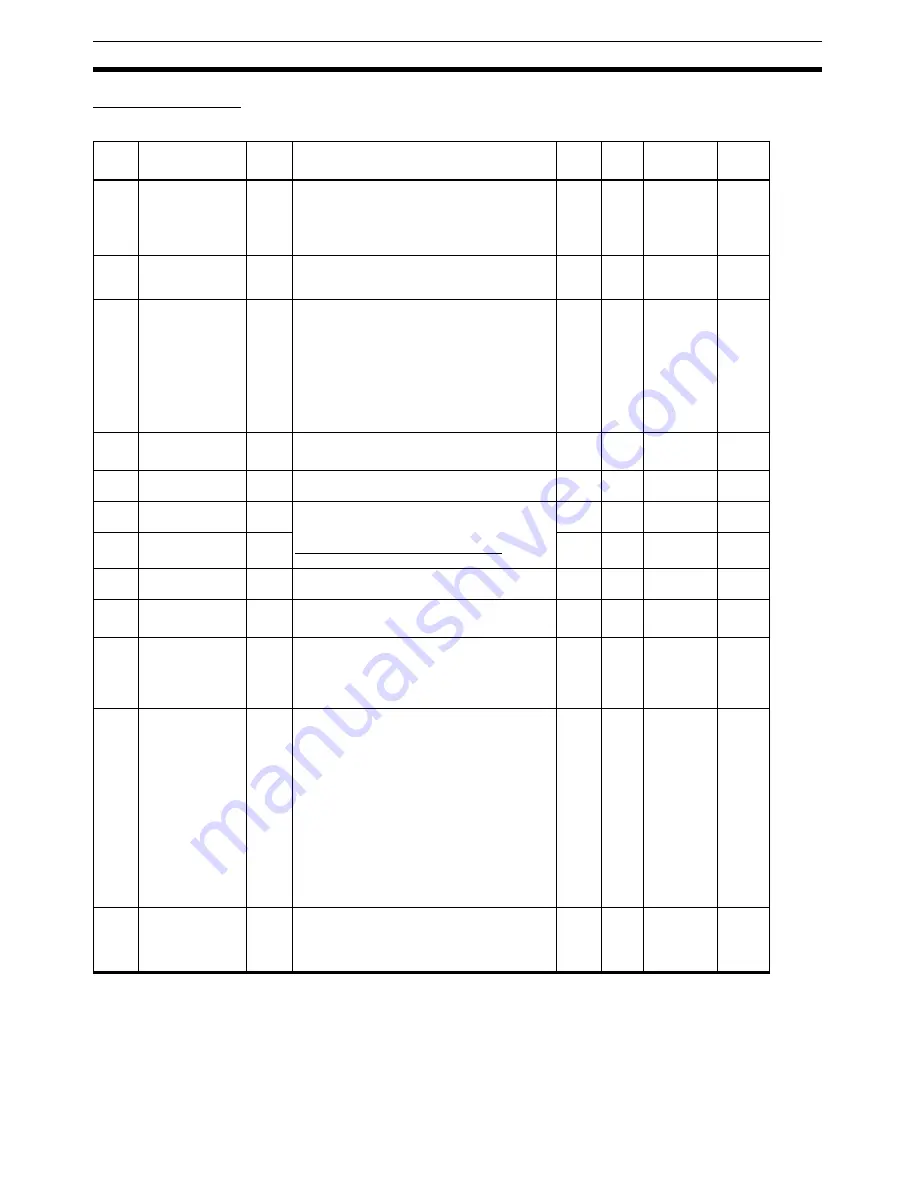
106
Servo Parameter Area
Section 4-5
Parameter Tables
Basic Parameters
Param-
eter
No.
Parameter name
Param-
eter
size
Explanation
Default
setting
Unit
Setting
range
Data
attribute
000
(000)
Rotation Direction
Switching
2
Set the relation between the command direction and
the motor rotation direction.
0: With a forward rotation command, the motor rotates
CW as viewed from the axis end.
1: With a forward rotation command, the motor rotates
CCW as viewed from the axis end.
1
-
0 to 1
C
001
(001)
Control Mode Selec-
tion
2
Select the Servo Drive CONTROL mode.
0 to 5: Switch function
6: Full closing control
0
-
0 to 6
R
002
(002)
Realtime Autotuning
Mode Selection
2
Set the OPERATION mode for realtime autotuning.
0: Disabled
1: Emphasizes stability
2: Emphasizes positioning
3: If there is an unbalanced load on the vertical axis or
the like.
4: When friction is large.
5: If there is an unbalanced load on the vertical axis or
the like and friction is too large.
6: When the realtime autotuning is customized.
1
-
0 to 6
B
003
(003)
Realtime Autotuning
Machine Rigidity Set-
ting
2
Set the machine rigidity for executing realtime autotun-
ing.
11/13
-
0 to 31
B
004
(004)
Inertia Ratio
2
Set the load inertia as a percentage of the motor rotor
inertia.
250
%
0 to 10000
B
009
(009)
Electronic Gear
Ratio Numerator
4
Set the electronic gear ratio.
If Pn009 = 0, the encoder resolution is set as the
numerator.
Electronic Gear Ratio Numerator (Pn009)
Electronic Gear Ratio Denominator (Pn010)
1
-
0 to 2
30
C
010
(00A)
Electronic Gear
Ratio Denominator
4
1
-
1 to 2
30
C
013
(00D)
No. 1 Torque Limit
2
Set the No. 1 limit value for the output torque of the
motor.
500
%
0 to 500
B
014
(00E)
Error Counter Over-
flow Level
4
Set the range of the error counter overflow level. Detec-
tion of error counter overflow level error is disabled if
the set value is 0.
100000
Com-
mand
unit
0 to 2
27
A
015
(00F)
Operation Switch
when Using Absolute
Encoder
2
Select the absolute encoder usage method.
0: Used as absolute encoder.
1: Used as an incremental encoder.
2: Used as absolute encoder.
(Multi-rotation counter overflows are ignored.)
1
-
0 to 2
C
016
(010)
Regeneration Resis-
tor Selection
2
Select the Regeneration Resistor used.
0: Use the Built-in Resistor.
Triggering of regeneration overload protection
(Alarm No.18) depends on the Built-in Resistor (with
approx. 1% duty).
1: Use an External Resistor.
The regeneration processing circuit operates and
regeneration overload protection (Alarm No.18) is
triggered when the operating rate of the Regenera-
tion Resistor exceeds 10%.
2: Use an External Resistor.
Regeneration overload protection (Alarm No.18)
does not operate.
3: No Regeneration Resistor
All regeneration power is processed with built-in
capacitors.
0/3
-
0 to 3
C
017
(011)
External Regenera-
tion Resistor Setting
2
Select the type of load ratio calculation for the External
Regeneration Resistor.
0: Regeneration load ratio is 100% when operating
rate of the External Regeneration Resistor is 10%.
1 to 4: Reserved
0
-
0 to 4
C
Summary of Contents for CJ1W-NC271 - 12-2009
Page 2: ......
Page 4: ...iv ...
Page 6: ...vi ...
Page 22: ...xxii ...
Page 58: ...30 Starting Operation Section 2 2 ...
Page 244: ...216 Axis Operating Input Memory Areas Section 4 8 ...
Page 264: ...236 Transferring Servo Parameters Section 5 3 ...
Page 396: ...368 Linear Interpolation Section 9 7 ...
Page 648: ...620 List of Error Codes Appendix D ...
Page 674: ...646 Additional Functions for the CJ1W NCF71 MA Appendix F ...
Page 684: ...656 Index ...
Page 686: ...658 Revision History ...