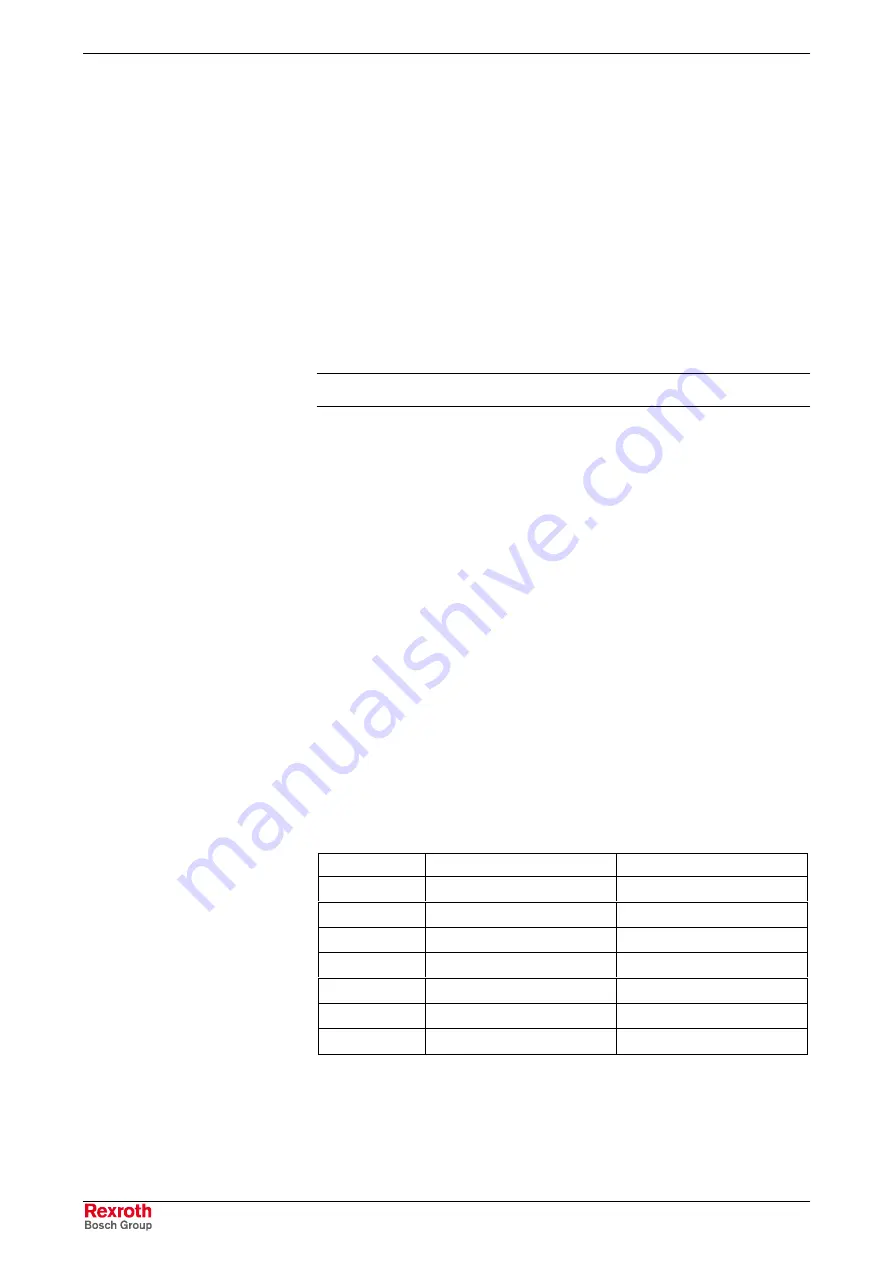
10-74
Handling, Diagnostic and Service Functions
MPH-02, MPB-02, MPD-02
DOK-INDRV*-MP*-02VRS**-FK01-EN-P
10.11 Serial Communication
Overview of Serial Communication
The serial interface of the drive controller is used as a universal medium
of communication for different services. It can be used for master
communication (in addition to SERCOS), for reading and writing
parameters, for replacing the firmware, for locating errors and for other
services. The physical standards used are RS232 and RS485.
Two protocols are supported for serial communication:
•
ASCII-based
protocol
•
SIS protocol (Rexroth-standard serial binary protocol)
Note:
The protocol is automatically recognized by the drive!
The following functions are made possible via the serial interface:
•
reading and writing parameters via terminal or commissioning tool
(DriveTop) in parallel with the existing master communication
•
connecting a control terminal (BTV04)
•
downloading firmware via the "Dolfi" program
The maximum baud rate is 115 kB.
Pertinent Parameters
•
P-0-4021, Baud rate RS-232/485
•
P-0-4022, Drive address of serial interface
•
P-0-4050, Delay answer RS-232/485
•
P-0-4095, RS-232/485 Parity
General Information on the Parameter Structure
All parameters of the drive controller are stored in a uniform parameter
structure. Each parameter consists of 7 elements. The table below
describes the individual elements and the possibilities of access. The
following sections will also refer to the parameter structure below.
Element No.
Data block element
Possibility of access
1
IDN
read
2
name
read
3
attribute
read
4
unit
read
5
min. input value
read
6
max. input value
read
7
operating data
read / write
Fig. 10-35: Parameter structure
Courtesy
of
CMA/Flodyne/Hydradyne
▪
Motion
Control
▪
Hydraulic
▪
Pneumatic
▪
Electrical
▪
Mechanical
▪
(800)
426-5480
▪
www.cmafh.com