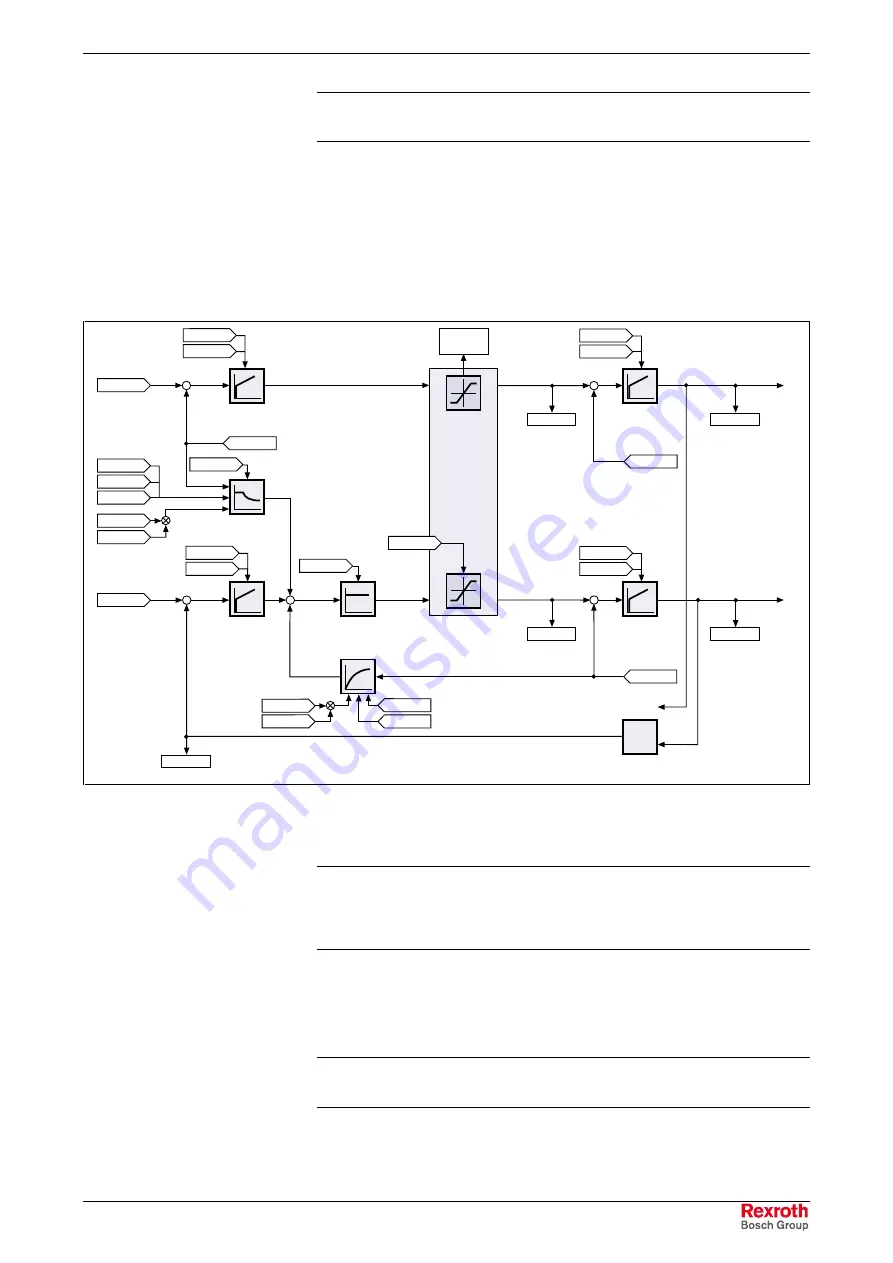
MPH-02, MPB-02, MPD-02
Drive Control
6-15
DOK-INDRV*-MP*-02VRS**-FK01-EN-P
Note:
Utilization of the reluctance effect allows increasing the
available torque in the base speed range.
Field-Oriented Closed-Loop Current Control of an
Asynchronous Machine
Field-oriented closed-loop control of the asynchronous machine differs
from closed-loop control of the synchronous machine in the additional
function blocks "flux feedforward" and "flux loop incl. flux model". The
figure below illustrates the control loop structure and the points at which
the individual parameters take effect.
-
-
-
-
S-0-0040
voltage
loop
P-0-4005
P-0-4045
P-0-4046
flux loop
P-0-0043
S-0-0107
S-0-0106
P-0-0063
P-0-0044
P-0-0064
P-0-0065
flux model
ï
U
act
ï
P-0-0530
-
+
S-0-0101
S-0-0100
P-0-4043
P-0-4041
P-0-4042
P-0-0038
P-0-0039
P-0-0528
P-0-0534
P-0-0533
P-0-0045
S-0-0107
S-0-0106
DF000128v01_en.fh7
n
act
I
d_cmd
current
limitation
I
q_act
I
d_act
I
q-loop
I
d-loop
U
q_act
U
d_act
P-0-4041
P-0-4042
flux
feedforward
P-0-0048
P-0-0536
velocity
loop
I
q_cmd
P-0-4039
P-0-0535
P-0-0532
I
d_cmd
1)
I
q_cmd
1)
n
cmd
1):
current command value after limitation
Fig. 6-14:
Simplified schematic diagram of the current control loop for an
asynchronous machine (incl. voltage loop and flux loop)
Note:
In the case of asynchronous motors, the field or rotor flux
control has a decisive influence on the torque generation and
dynamic response of the machine, particularly in the field
weakening range.
Due to high magnetization (rotor flux) the motor produces a higher torque.
In no-load operation the magnetization, however, produces loss which is
the reason why it is useful to reduce magnetization for less dynamic
applications.
Note:
For reducing magnetization a value between 50% and 100%
can be set in parameter
P-0-0532, Premagnetization factor
.
Flux Feedforward
Courtesy
of
CMA/Flodyne/Hydradyne
▪
Motion
Control
▪
Hydraulic
▪
Pneumatic
▪
Electrical
▪
Mechanical
▪
(800)
426-5480
▪
www.cmafh.com