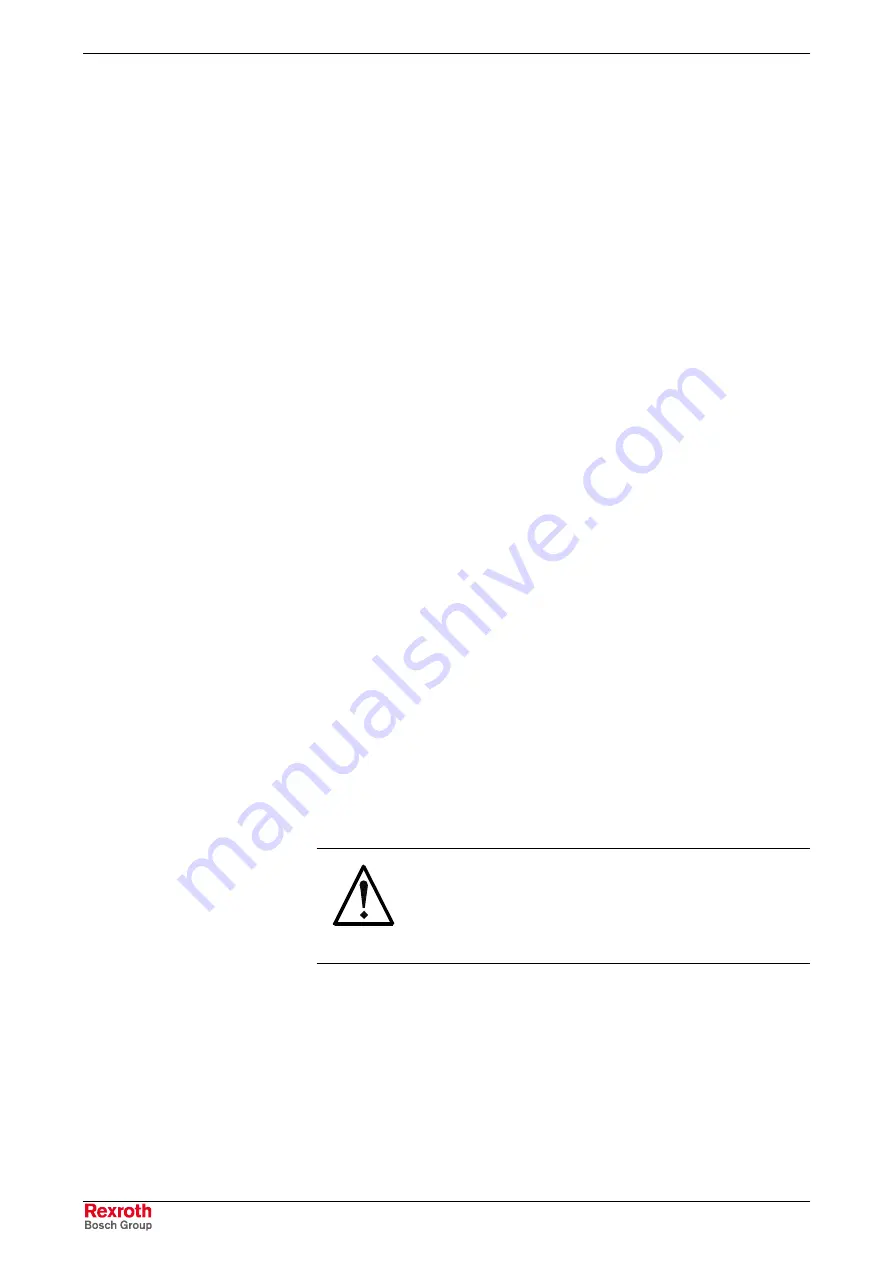
8-52
Drive Functions
MPH-02, MPB-02, MPD-02
DOK-INDRV*-MP*-02VRS**-FK01-EN-P
The correction values are determined once during initial commissioning. If
encoder correction has been activated with the drive in operation
(respective bits of P-0-0341), the signal shape errors of the encoder track
are compensated by adding a correction value. The correction values are
generated from the table values of parameter P-0-0342. If there hasn’t
been any encoder selected, the encoder correction is deactivated!
According to experience the encoder correction can be effectively used
for encoders with the following characteristics:
•
rotary
encoders
→
up to approx. 1000 cycles/revolution
•
linear
encoders
→
division periods up to approx. 0.1mm
Observe the following basic principles for application:
•
If the encoder correction shouldn’t cause any improvement, this
function has to be deactivated (relieving the processor!).
•
If the constant speed of a drive is to be improved, the encoder
correction has to be applied to the motor encoder.
•
If the positioning precision is to be improved, the encoder correction
has to be applied to the position control encoder.
Notes on Commissioning
Before starting the command C3500 make the following preparations for
the respective drive:
•
Determine the encoder to be corrected in
P-0-0341, Control word for
encoder correction
.
•
Determine the velocity that mustn’t be exceeded for acquiring the
encoder signals.
•
Estimate the travel range of the axis for a motion time of at least 4 s
with the maximum acquisition velocity and make sure that the travel
range is sufficient (start position, direction of motion).
•
Activate the "velocity control" mode.
During initial commissioning the encoder correction has to be carried out
once:
•
activate drive ("AF") and start
P-0-0340, C3500 Command Determine
encoder correction values
•
input velocity command values of approx. 75% of calculated maximum
value
CAUTION
Property damage caused by errors when
controlling motors and moving parts!
⇒
Make sure that the travel range of the axis is
sufficient! Activate axis end position switches and set
them to collision-safe positions!
•
Observe the status of command execution and with the end of the
command execution set the velocity command value to zero.
•
Check the effectiveness of the encoder correction, e.g. by checking
the amplitude of the speed deviation, if, as in the case of the
acquisition of the encoder signals with activated and deactivated
encoder correction, the same distance is traveled in the same way.
With active encoder correction the amplitude has to be distinctly
smaller!
If necessary, repeat the command C3500 with modified acquisition
velocity!
Activation/Deactivation
Notes on Application
Preparation
Carrying Out Encoder Correction
Courtesy
of
CMA/Flodyne/Hydradyne
▪
Motion
Control
▪
Hydraulic
▪
Pneumatic
▪
Electrical
▪
Mechanical
▪
(800)
426-5480
▪
www.cmafh.com