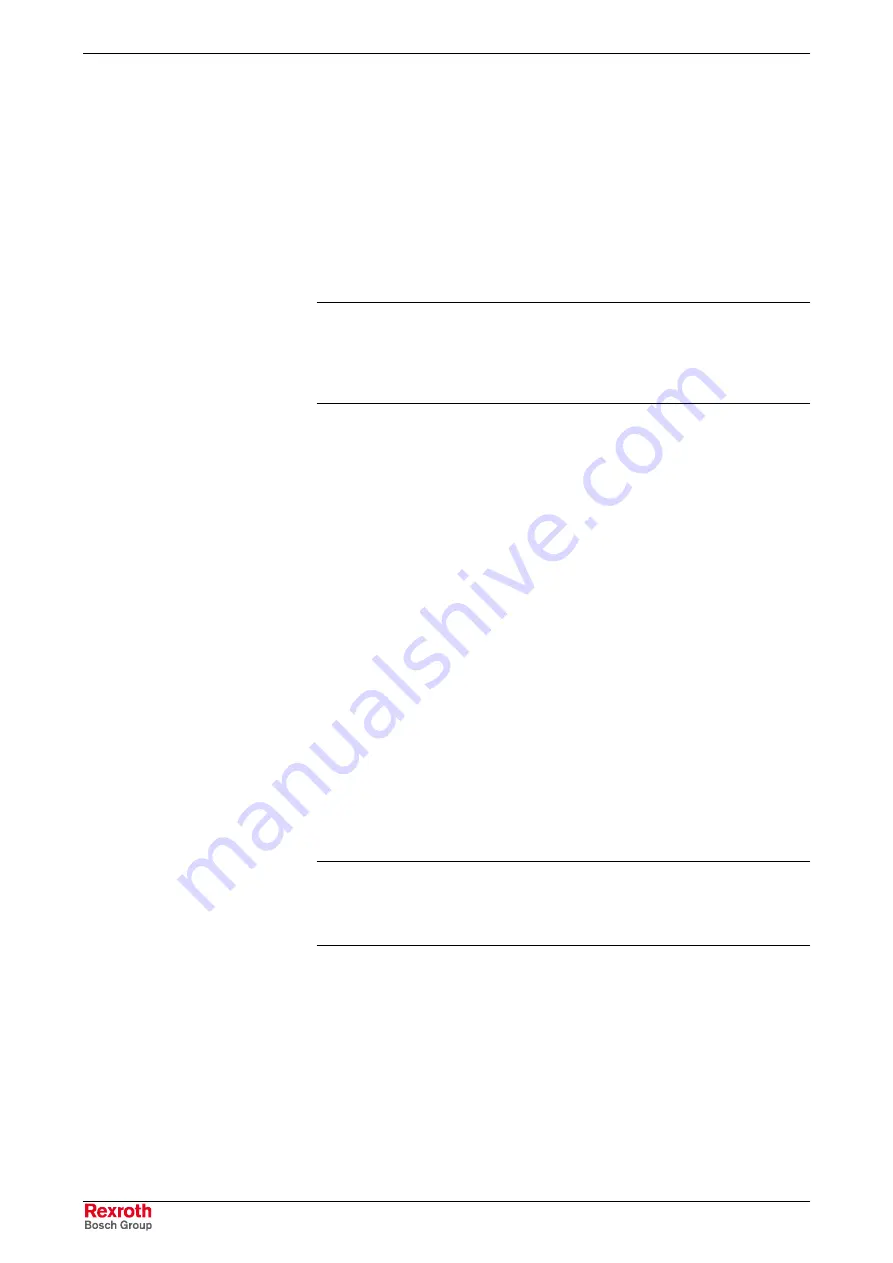
5-56
Motor, Mechanical Axis System, Measuring Systems
MPH-02, MPB-02, MPD-02
DOK-INDRV*-MP*-02VRS**-FK01-EN-P
Set the resolution (number of lines, division period) of the optional
encoder:
S-0-0117, Feedback 2 Resolution
Set the kind of encoder and the rotational direction of the motor encoder:
S-0-0277, Position feedback 1 type
Set the kind of encoder and the rotational direction of the optional
encoder:
S-0-0115, Position feedback 2 type
Note:
In the case of Rexroth housing motors (MHD, MKD, MKE,
2AD, ADF, MAD, MAF), P-0-0074, S-0-0116 and S-0-0277 are
automatically written with the correct value; in the case of
linear motors, P-0-0074 and S-0-0116 are automatically
written with the correct value.
Enter the travel range of the axis:
•
S-0-0278, Maximum travel range
Current actual position value of the motor encoder:
•
S-0-0051, Position feedback 1 value
Current actual position value of the optional encoder:
S-0-0053, Position feedback 2 value
Position status of the connected encoders:
S-0-0403, Position feedback value status
Multiplication of the motor encoder:
S-0-0256, Multiplication 1
Multiplication of the optional encoder:
S-0-0257, Multiplication 2
Resolution of the position data in the drive:
P-0-0129, Internal position data format
Note:
When S-0-0256 and, if available, S-0-0257 have the value
32768, the encoder evaluation is ideal. When the value is
lower, S-0-0278 has to be checked for correct travel range
input!
Monitoring the Measuring Systems
Brief Description
Correct position information is the prerequisite for reliable drive behavior
and motion according to contour. In order to guarantee best possible
position evaluation the encoder signals are therefore monitored for
plausibility and compliance with the allowed tolerances.
Setting the Travel Range
Information on Position
Evaluation
Monitoring the Encoder Signals
Courtesy
of
CMA/Flodyne/Hydradyne
▪
Motion
Control
▪
Hydraulic
▪
Pneumatic
▪
Electrical
▪
Mechanical
▪
(800)
426-5480
▪
www.cmafh.com