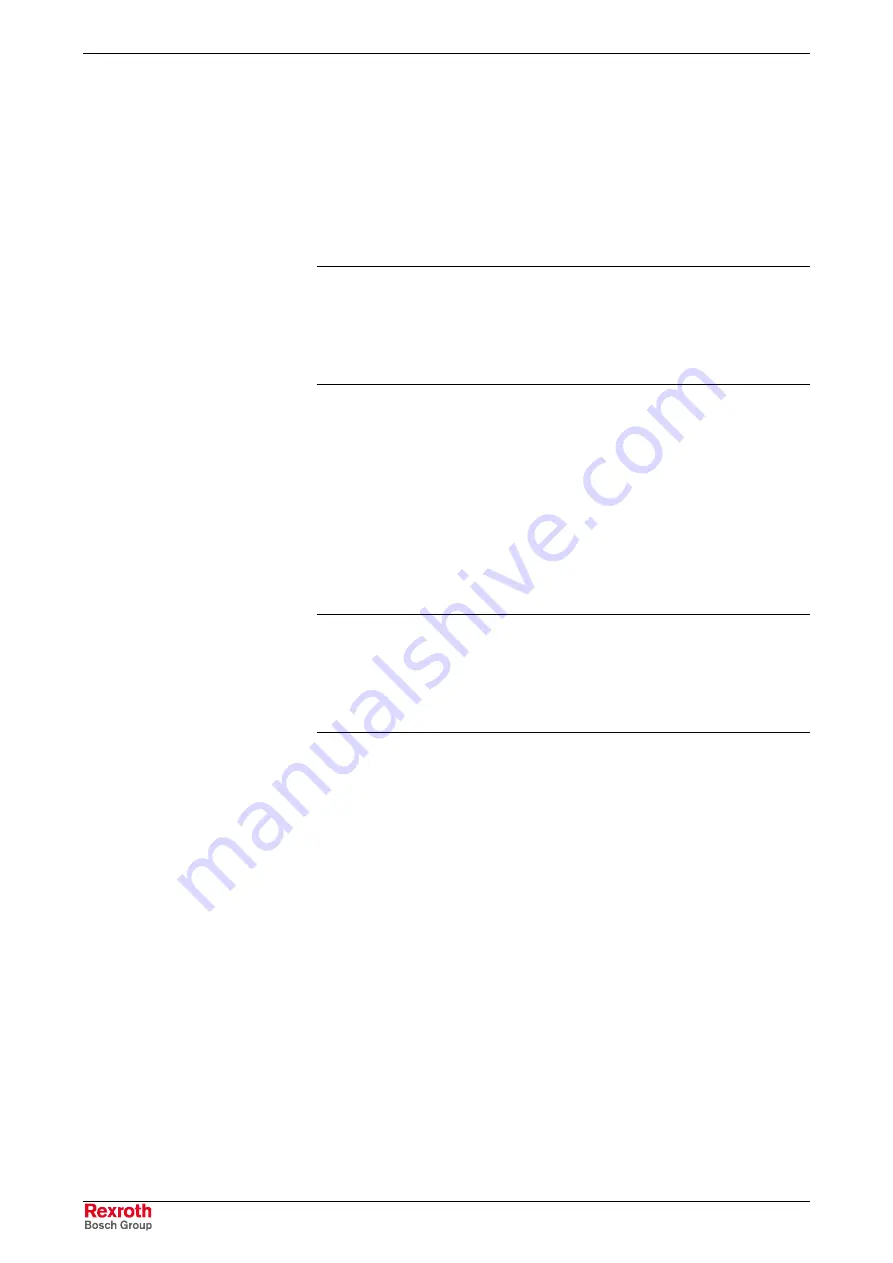
4-68
Master Communication
MPH-02, MPB-02, MPD-02
DOK-INDRV*-MP*-02VRS**-FK01-EN-P
Notes on Commissioning/Parameterization
Encoder Emulation
In spite of its high degree of functionality and performance, the encoder
emulation available for IndraDrive devices is subject to some systematic
restrictions.
See "Encoder Emulation" in chapter "Extended Drive Functions"
Note:
If the higher-level master and the drive have not been
synchronized, beat effects can occur during sampling due to
the different clock-pulse rates. Bosch
Rexroth therefore
recommends not to use the analog interface in high end
applications but in these cases use digital interfaces, such as
SERCOS interface.
Analog Inputs
For inputting the cyclic command value you should preferably use
assignment channel A as it has a higher sampling rate than assignment
channel B.
In spite of their high degree of functionality and performance, the analog
inputs available for IndraDrive devices are subject to certain restrictions.
These restrictions are explained in detail in section "Analog Inputs"
See also "Analog Inputs" in chapter "Extended Drive Functions"
Note:
If the drives with analog command value input have not been
synchronized, beat effects can occur during sampling in spite
of the 8-fold oversampling. Bosch
Rexroth therefore
recommends not to use the analog interface in high end
applications but in these cases use digital interfaces, such as
SERCOS interface.
Main Spindle Drive with Analog Interface and Parallel
Interface
In the case of main spindle drives, operating states that are important for
the working cycle have to be transmitted to the master so that it can
process or advance the command blocks in accordance with the process
and in a fail-safe way.
The "spindle positioning" command allows aligning the spindle for tool
change without the master having to leave the "velocity control" mode
mainly used for spindles.
In the case of master communication with analog interface, the required
messages have to be made available to the master via the digital outputs.
The "spindle positioning" command has to be started via a digital input.
To do this, the main spindle messages are assigned to the digital outputs,
the command parameter to a digital input.
The following
messages
are relevant for main spindle drives:
•
speed reached (
S-0-0330, Message ’n_actual = n_command’
)
•
spindle has stopped (
S-0-0331, Status ’n_feedback = 0’
)
•
speed value has fallen below threshold (
S-0-0332, Message ’nactual
< nx’
)
Courtesy
of
CMA/Flodyne/Hydradyne
▪
Motion
Control
▪
Hydraulic
▪
Pneumatic
▪
Electrical
▪
Mechanical
▪
(800)
426-5480
▪
www.cmafh.com