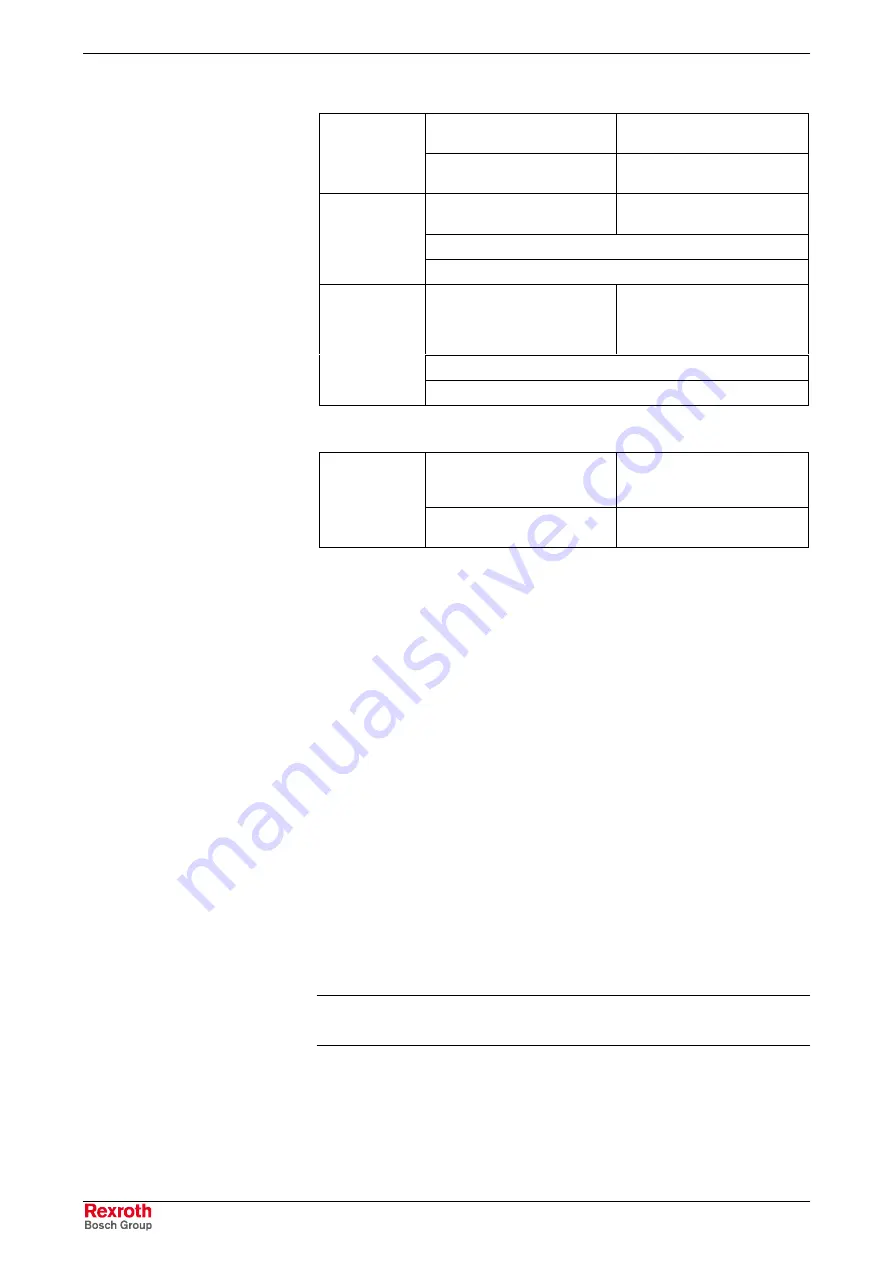
4-52
Master Communication
MPH-02, MPB-02, MPD-02
DOK-INDRV*-MP*-02VRS**-FK01-EN-P
ProfiDrive parameter request via DPV1
request reference
1 to 255
request ID
2 = change parameter
request
header
axis
0
number of parameters
1
attribute
16 = value
number of elements
1
parameter number
parameter
address
sub-index
format
65 = bytes
66 = word
67 = double word
number of values
1 to 10
value(s)
parameter
value(s)
...
DPV1 parameter response
request ref. mirrored
1 to 255
response ID
2 = positive acknowledge
130 = negative acknowledge
response
header
axis mirrored
1
number of parameters
1
Cyclic Communication via Process Data Channel
Communication Cycle Time
Cyclic communication via the process data channel takes place in the so-
called communication cycle (cf.
P-0-4076, Field bus: cycle time (Tcyc)
).
The communication cycle indicates the time intervals in which the cyclic
data are transmitted or processed.
Cycle times of the interface:
•
basic
design
→
1 ms to 65 ms (in steps of 1 ms)
•
advanced
design
→
500 µs to 65 ms (in steps of 500 µs)
Processing the Cyclic Data
The internal processing of the command values and actual values is
carried out synchronously with the control clock. As the communication
via PROFIBUS-DP is not carried out in a synchronous way, this type of
master communication is not suited for synchronous operating modes
such as "position control with cyclic command value input", but only for
positioning modes and velocity control.
In the drive only a limited number of cyclic data can be processed
(
Basic: 16 Byte; Advanced: 32 Byte).
Note:
There is no limit value check for the cyclically transmitted
command values and they are not stored in volatile form.
Configuring the Process Data Channel
The cyclic data have to be configured in the parameter mode. The section
"Configuring the PROFIBUS-DP Slave" describes how the cyclic data are
configured.
Change Parameter
Courtesy
of
CMA/Flodyne/Hydradyne
▪
Motion
Control
▪
Hydraulic
▪
Pneumatic
▪
Electrical
▪
Mechanical
▪
(800)
426-5480
▪
www.cmafh.com