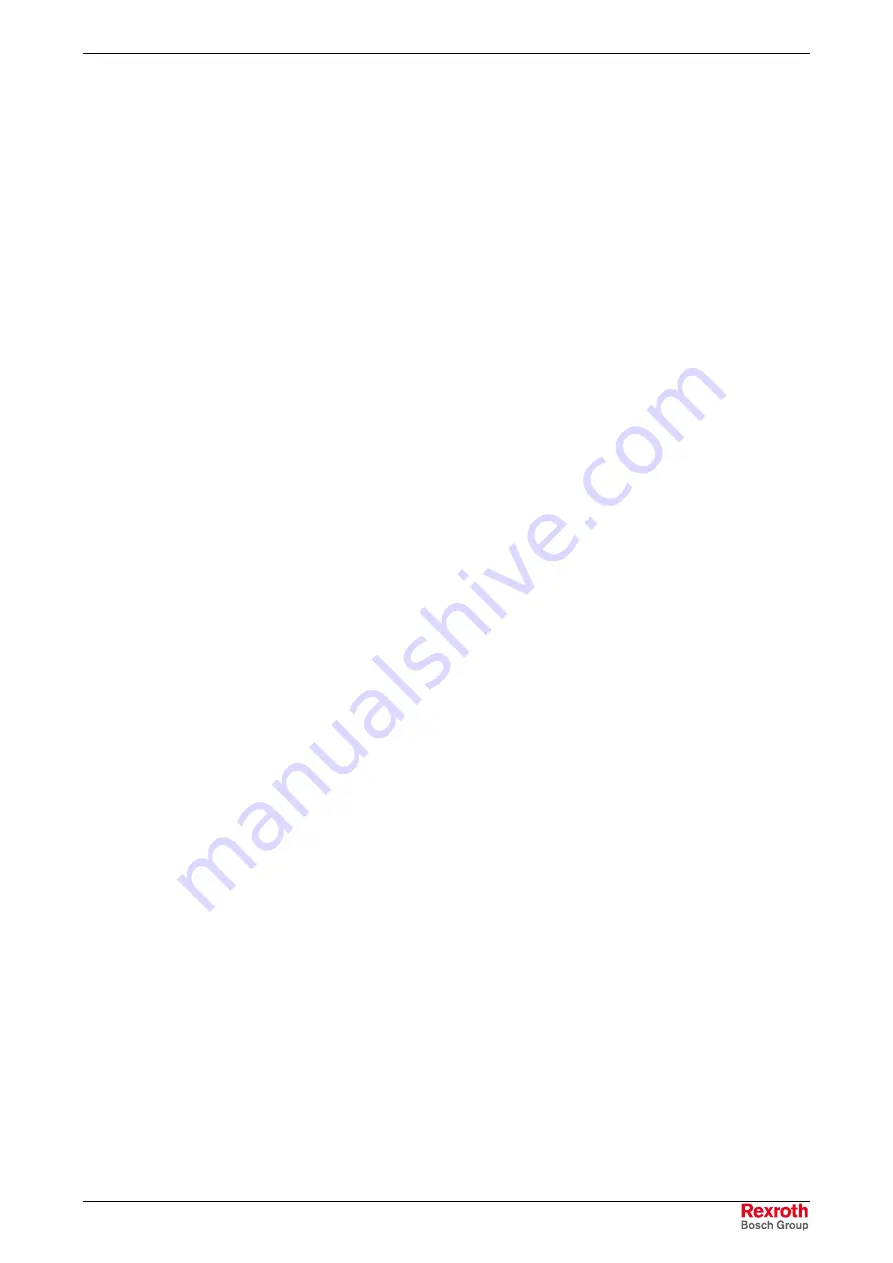
MPH-02, MPB-02, MPD-02
Drive Control
6-41
DOK-INDRV*-MP*-02VRS**-FK01-EN-P
The "torque/force control" mode actually isn’t torque or force control but
current control. Therefore, only the current control loop is closed in the
drive.
See also "Torque/Force Control" in chapter "Operating Modes"
Notes on Commissioning for Control Loop Setting
The control loop settings in a digital drive controller are very important for
the features of the servo axis.
To optimize the control loop setting, application-specific controller
parameters are available for all digital Rexroth drives.
Due to the cascade structure of the control loops it is necessary to
parameterize them "from the inside to the outside". The resulting order for
setting the control loops is as follows:
1.
Current control loop
For
Rexroth motors with motor encoder data memory
(MHD,
MKD and MKE series), optimizing the current loop is not required
because the corresponding parameter values (S-0-0106 and
S-0-0107) are read from the motor encoder data memory.
For all
Rexroth motors without motor encoder data memory
(e.g.
linear motors), the parameter settings can be taken from a central
motor data base via the "DriveTop" commissioning tool.
The commissioning of
third-party motors
(incl. control loop setting)
is described in the respective sections on third-party motors in this
documentation (see "Third-Party Motors at IndraDrive Controllers" in
chapter "Motor, Mechanical Axis System, Measuring Systems").
2.
Velocity control loop
The settings of the velocity loop (S-0-0100 and S-0-0101) with the
respective filters (P-0-0004 and P-0-1120, P-0-1121, P-0-1122,
P-0-1123) on the one hand depend on the motor parameters (inertia
and torque/force constant), on the other hand they strongly depend on
the mechanical properties (load inertia/mass, friction, stiffness of the
connection, ...). Therefore, manual or automatic optimization is often
required (see section "Control Loop Setting").
3.
Position control loop
In general, the position control loop only has to be adjusted to the
dynamics of the outer velocity loop, as well as to the kind of preset
command values (jerk, acceleration and interpolation procedure).
Default Settings in the Motor Encoder Data Memory
For all Rexroth motors of the series with motor encoder data memory
(e.g. MHD, MKD, MKE, MSK and possibly MAD and MAF), the basic
settings for the controllers are stored and can be loaded to the drive by
executing the "load defaults procedure" command (S-0-0262).
There are two ways to activate the
S-0-0262, C07_x Load defaults
procedure command
parameter:
•
Automatically when running up the drive by recognizing that the motor
type (cf. parameter S-0-0141) has changed. The display then reads
"RL" and the "load defaults procedure" command is internally started
by pressing the "Esc" button on the control panel, unless this was
deactivated in
P-0-0556, Control word of axis controller
.
•
Starting the command by writing "11b" to parameter S-0-0262.
See also "Loading, Storing and Saving Parameters" in chapter "Handling,
Diagnostic and Service Functions"
Torque/Force Control
Order of Manual Control Loop
Setting
S-0-0262, C07_x Load defaults
procedure command
Courtesy
of
CMA/Flodyne/Hydradyne
▪
Motion
Control
▪
Hydraulic
▪
Pneumatic
▪
Electrical
▪
Mechanical
▪
(800)
426-5480
▪
www.cmafh.com