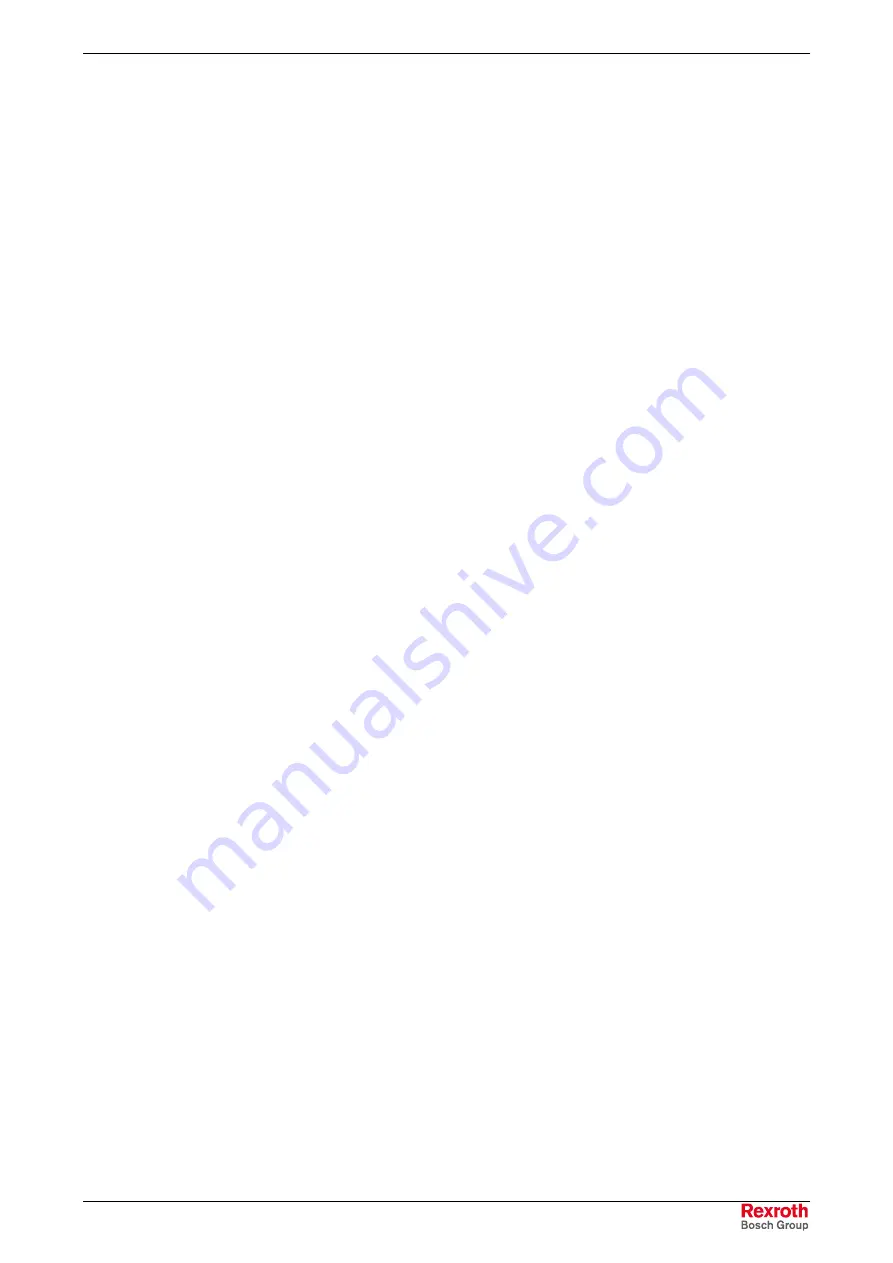
MPH-02, MPB-02, MPD-02
Drive Control
6-19
DOK-INDRV*-MP*-02VRS**-FK01-EN-P
•
C0132 Invalid settings for controller cycle times
An error in the parameterization of the controller cycle times and pulse
width modulation frequency was detected.
•
C0251 Error during synchronization to master communication
The synchronization of drive control to the bus interface (SERCOS,
PROFIBUS, Interbus …) failed during progression to the operating
mode.
•
E8025 Overvoltage in power section
This warning is generated when the DC bus voltage exceeds a value
of 870.0 V. In this case, the current loop is temporarily switched off to
protect the motor.
•
E8028 Overcurrent in power section
This warning is generated when the total current > 1.2 * minimum
(
S-0-0109, Motor peak current
;
S-0-0110, Amplifier peak current
).
In this case, the current loop is temporarily switched off to protect the
motor (avoiding demagnetization).
•
F2067 Synchronization to master communication incorrect
The synchronization of drive control to the bus interface (SERCOS,
PROFIBUS, Interbus …) failed during operating.
•
F2077 Current measurement trim wrong
During zero adjust of the current measurement a deviation outside the
tolerance range occurred (hardware defect).
Commutation Setting
Brief Description
The following Rexroth kit motors are manufactured according to the
"synchronous motor" functional principle:
•
LSF, MLF linear motors
•
MBS and MBT rotary motors
As the motor is assembled in the machine, stator, rotor and measuring
system can only be put together on site. The electric-magnetic-
mechanical allocation of the synchronous motor is therefore only to be
made on site. This is done by determining and setting the commutation
offset.
Absolute measuring systems should ideally be used for synchronous
Rexroth kit motors. The advantage in this case is the absolute position
detection of the rotor position which immediately ensures, when drive
enable is set, the correct assignment of current in the primary part to the
magnetic field in the secondary part. This is realized by the commutation
offset stored at initial commissioning.
For some applications it is necessary to use incremental measuring
systems because the available length of absolute measuring systems is
limited, for example. The disadvantage in this case is that absolute
detection of the rotor position is impossible. It is therefore necessary, after
each time the drive is switched on again or after having changed the
communication phase from "P2" to "P4" ("bb" or "Ab"), to set the
commutation offset again. This disadvantage can be removed by using
the Hall sensor box SHL01.1, because with regard to commutation setting
the relative motor encoder then behaves like an absolute measuring
system.
Errors, Warnings and Monitoring
Functions
Measuring Systems for
Synchronous Rexroth Motors
Courtesy
of
CMA/Flodyne/Hydradyne
▪
Motion
Control
▪
Hydraulic
▪
Pneumatic
▪
Electrical
▪
Mechanical
▪
(800)
426-5480
▪
www.cmafh.com