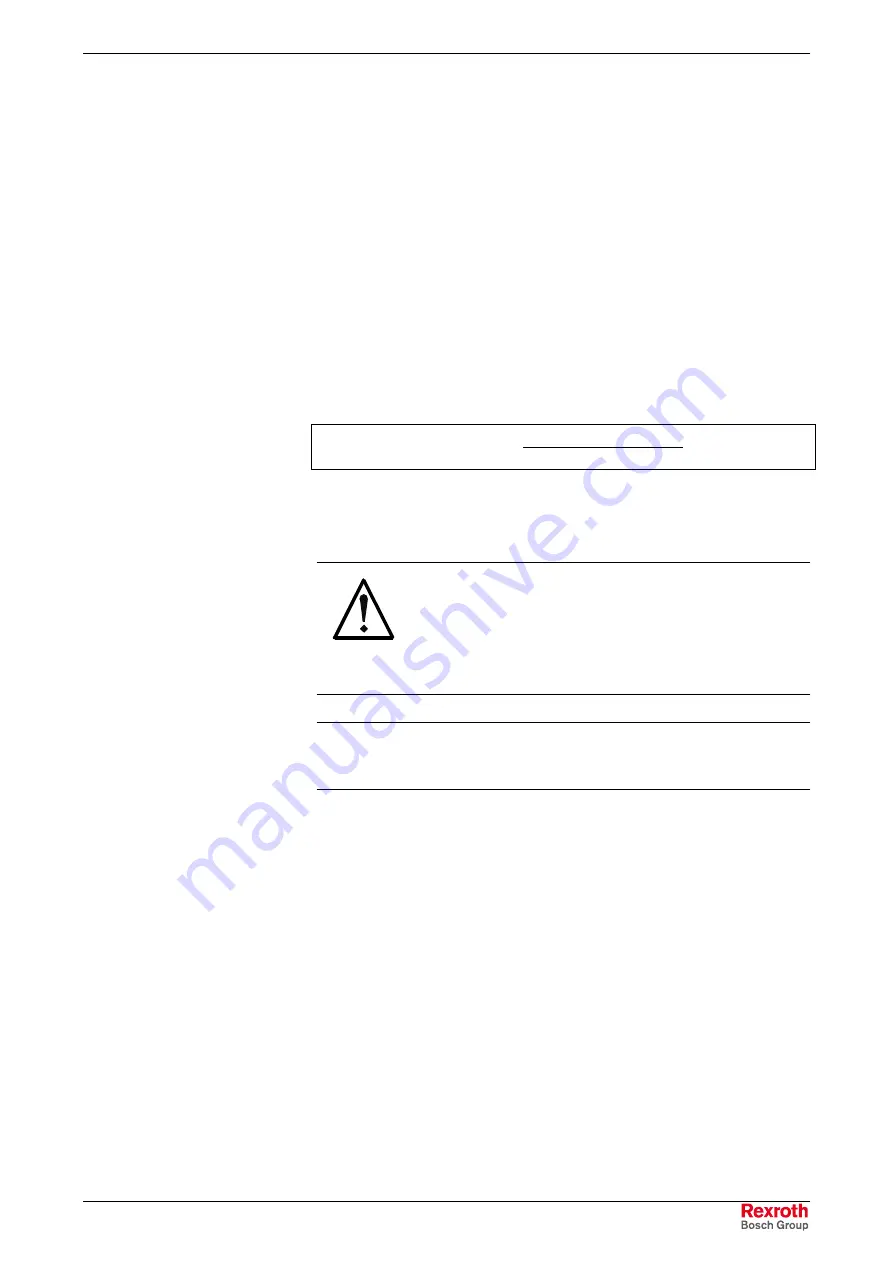
MPH-02, MPB-02, MPD-02
Drive Control
6-47
DOK-INDRV*-MP*-02VRS**-FK01-EN-P
See Parameter Description "P-0-0165, Selection for autom. controller
adjust"
Possible results of automatic control loop setting (with respective bit set in
P-0-0165):
•
bit 1
→
setting of velocity control loop
(cf. S-0-0100, S-0-0101, P-0-0004, P-0-1120 ...)
•
bit 2
→
setting of position control loop (cf. S-0-0104)
•
bit 4
→
determination of load inertia (reduced to motor shaft) and
input in parameter P-0-4010
•
bit 6
→
determination of maximum drive acceleration and input in
parameter P-0-0168
•
bit 3
→
determination of acceleration feedforward
As the result of the automatic control loop setting, the value
for acceleration feedforward is calculated according to the
formula below and entered in parameter P-0-0348.
0051
0
S
0051)
0
P
(
4010)
0
(P
0348
0
S
−
−
−
−
+
−
−
=
−
−
Fig. 6-30:
Calculating the acceleration feedforward
Notes on Commissioning
CAUTION
Carrying out the automatic control loop setting
is connected with a drive motion!
⇒
Select the travel range defined with the parameters
P-0-0166 and P-0-0167 or P-0-0169 such that
danger to man and machine resulting from drive
motion is excluded.
Note:
The parameter settings required to execute the command
"automatic control loop setting" must be made prior to
command start.
The automatic control loop setting is started by writing the binary numeric
value "3" (11b) to parameter
P-0-0162,
C1800 Command Automatic
control loop adjust
(command start).
An axis motion and thus the execution of the automatic control loop
setting is only possible if the "Drive Halt" signal has not been set. If the
"Drive Halt" signal has been set, the drive will acknowledge the start of
the
C1800 Command Automatic control loop adjust
, but the axis won’t
move.
Starting the Automatic Control
Loop Setting
Triggering a Motion
Courtesy
of
CMA/Flodyne/Hydradyne
▪
Motion
Control
▪
Hydraulic
▪
Pneumatic
▪
Electrical
▪
Mechanical
▪
(800)
426-5480
▪
www.cmafh.com