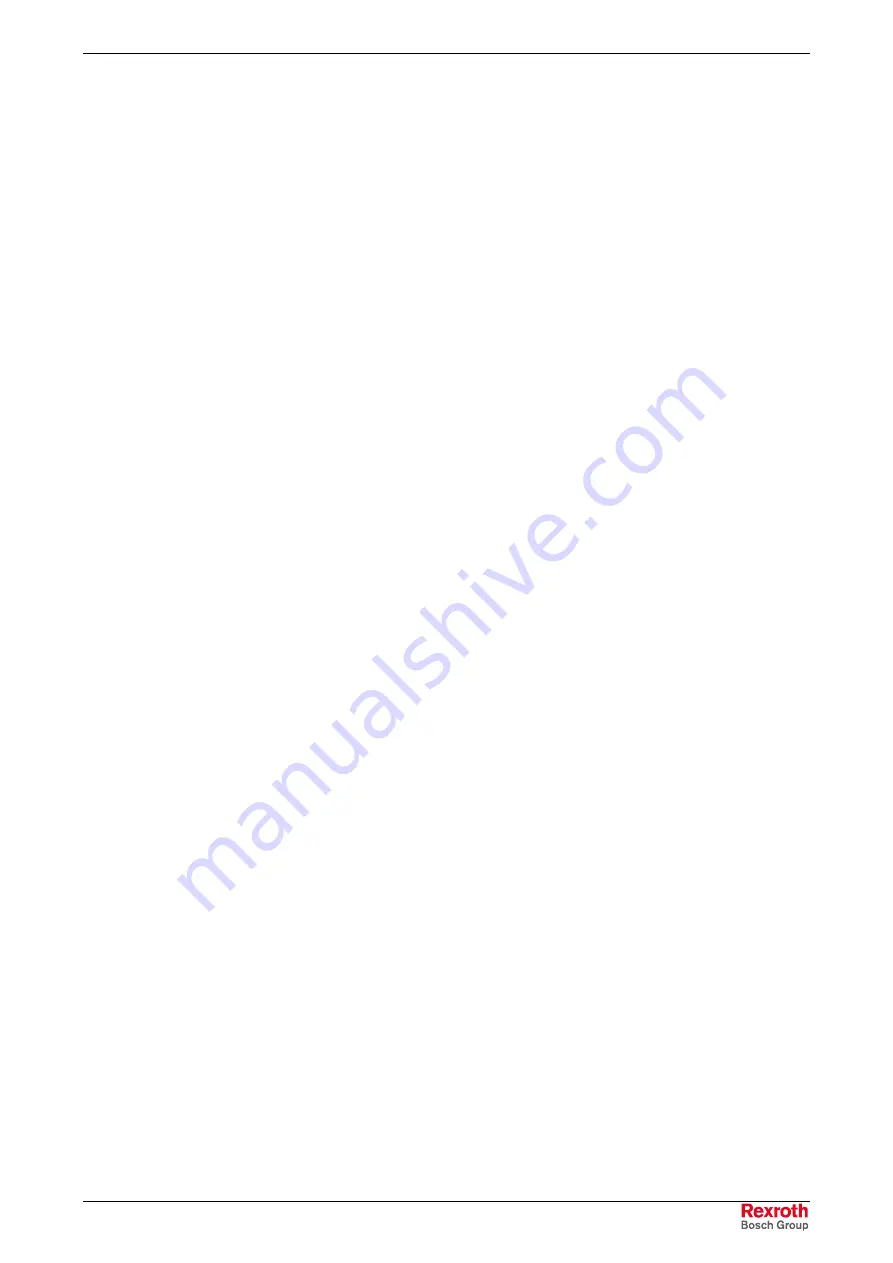
MPH-02, MPB-02, MPD-02
Motor, Mechanical Axis System, Measuring Systems
5-57
DOK-INDRV*-MP*-02VRS**-FK01-EN-P
Monitoring the encoder signals allows detecting faulty states, such as:
•
encoder is dirty
•
noise injection in the case of inappropriate wire routing or wire design
•
exceeding the max. allowed encoder velocity (limit frequency of the
encoder signals)
•
wire break or short circuit on wire
In addition it is possible to monitor drives with an encoder that can be
evaluated in absolute form for compliance with the position when
switching on compared to the last time the drive was switched off. This
allows detecting, for example, whether a vertical axis moved down after
the machine was switched off or whether an axis was moved away from
the position it had when the machine stopped.
It is also possible to monitor the difference between the actual position
values of motor encoder and external encoder. This allows, for example,
detecting slip due to wear in mechanical transfer elements between motor
and axis at an early stage.
If the loss of the position data reference of absolute encoders (motor
encoder or optional encoder) is detected due to changes in parameter
values, e.g. of the mechanical drive system, the drive will signal this faulty
status.
•
S-0-0391, Monitoring window feedback 2
•
P-0-0095, Absolute encoder monitoring window for motor
encoder
•
P-0-0096, Absolute encoder monitoring window for opt. encoder
•
P-0-0177, Absolute encoder buffer 1 (motor encoder)
•
P-0-0178, Absolute encoder buffer 2 (optional encoder)
•
P-0-0185, Function of encoder 2 (optional encoder)
•
P-0-0391, Actual position value difference encoder1 - encoder2
•
E2074 Encoder 1: encoder signals disturbed
•
E2075 Encoder 2: encoder signals disturbed
•
F2036 Excessive position feedback difference
•
F2042 Encoder 2: encoder signals incorrect
•
F2046 Max. signal frequency of encoder 2 exceeded
•
F2048 Low battery voltage
•
F2074 Actual pos. value 1 outside absolute encoder window
•
F2075 Actual pos. value 2 outside absolute encoder window
•
F2174 Loss of motor encoder reference
•
F2175 Loss of optional encoder reference
•
F8022 Enc. 1: enc. signals incorr. (can be cleared in ph. 2)
Functional Description
IndraDrive controllers can evaluate signals of the following encoder types:
•
sine encoder 1 Vpp (Heidenhain standard)
•
resolver encoder (Rexroth standard)
•
square-wave encoder 5V TTL (Heidenhain standard)
Monitoring the Axis Position
when Switching On
Monitoring Mechanical Transfer
Elements
Monitoring the Position Data
Reference
Pertinent Parameters
Pertinent Diagnostic Messages
Courtesy
of
CMA/Flodyne/Hydradyne
▪
Motion
Control
▪
Hydraulic
▪
Pneumatic
▪
Electrical
▪
Mechanical
▪
(800)
426-5480
▪
www.cmafh.com