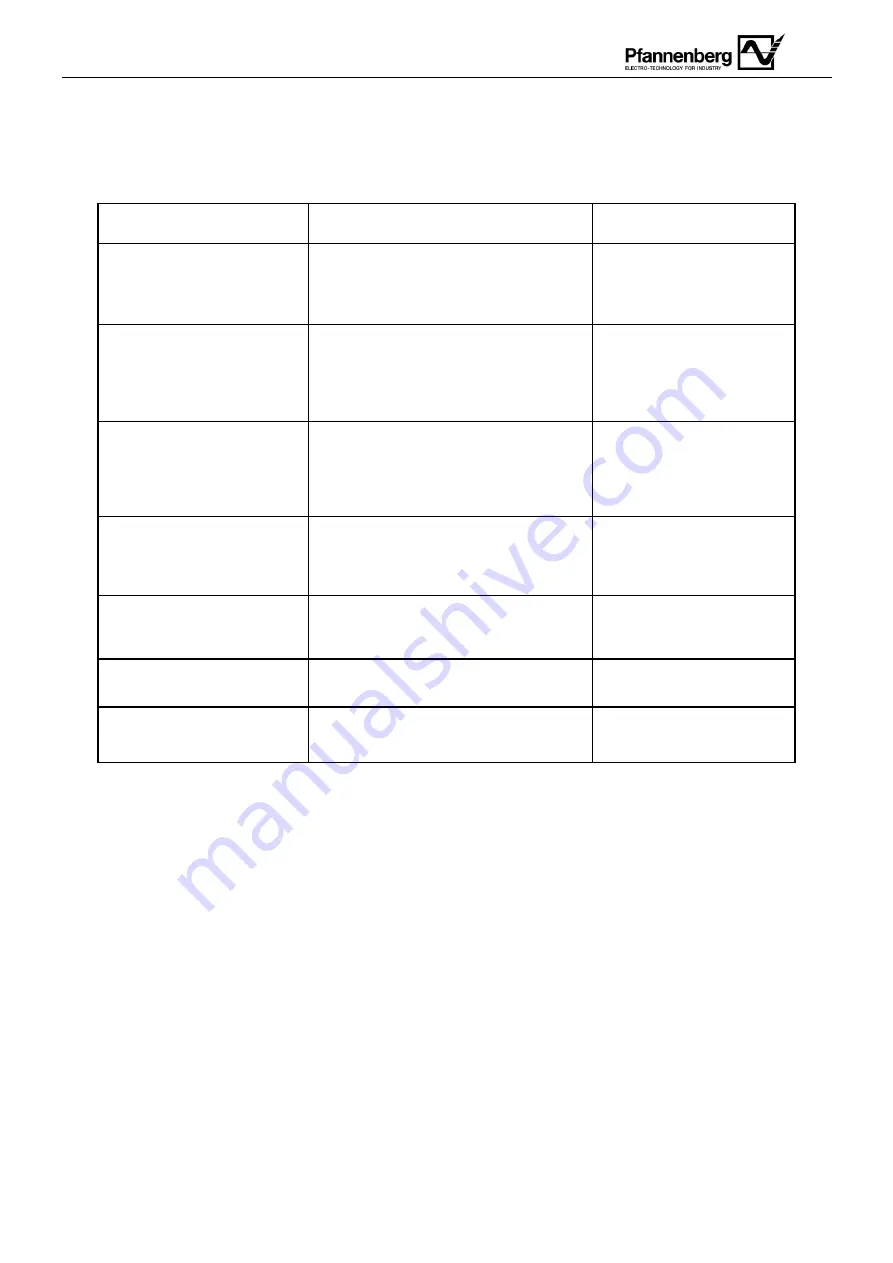
English
4
For Health and Safety reasons, please find below a list of potential risks that the operator is exposed to while commissioning
and/or operating and/or dismantling the unit:
Risk
Recommended Safety Measure
Residual Risk to be aware of
sharp edges
(such as heat
exchanger fins and internal
metal plates live edges)
It is recommended to use safety equipment
(such as gloves and protective cloths)
-
hot surfaces
(such as electric motor body of
pump or compressor and
refrigeration copper pipes)
It is recommended to use safety equipment
(such as gloves and protective cloths)
-
refrigerant under pressures
up
to 30 bar (435 PSI) within
refrigeration circuit
Always verify functionality of High Pressure
Switch.
Never open refrigeration circuit for
maintenance before releasing pressure*
Due to Toxicity of refrigerant
and oil still inside circuit, it is
recommended to use suitable
gloves and mask while
servicing refrigerant
equipment.
cooling water/glycol mixture
under pressures
up to 5,8 bar
(85PSI) within hydraulic circuits
(PWW series: PS = 12 bar)
Always check that all cooling water/glycol
pressure is released before sectioning and
servicing hydraulic equipment using purging
system and refill ball valve
Due to Toxicity of glycol and oil
still inside circuit, it is
recommended to use suitable
gloves and mask while
servicing hydraulic equipment
electrical shock
Always disconnect power supply and post a
‘
MAINTENANCE WORK IN PROGRESS’
sign on a visible position next to the main
switch during service
-
rotating fans
Always disconnect power supply and make
sure all mechanical equipment is stopped
before service.
-
Toxicity of refrigerant and
cooling liquid
It is recommended to use suitable protection
equipment (such as gloves, glasses, safety
shoes)
-
Summary of Contents for EB 130 WT
Page 20: ...English 20 APPENDIX A1...
Page 21: ...English 21 APPENDIX A2...
Page 26: ...English 26 Max pressure valve Thermostatic Valve Evaporator Refrigerant pipes Fan Pump...
Page 54: ...Deutsch 54 ANLAGE A1...
Page 56: ...Deutsch 56 ANLAGE A2...
Page 62: ...Deutsch 62 H chstdruckventil Thermostatisches Ventil Verdampfer K hlmittelrohre L fter Pumpe...
Page 89: ...Italiano 89 ALLEGATO A1...
Page 91: ...Italiano 91 ALLEGATO A2...
Page 124: ...Espa ol 124 ANEXO A1...
Page 126: ...Espa ol 126 ANEXO A2...
Page 159: ...Fran ais 159 ANNEXE A1...
Page 161: ...Fran ais 161 ANNEXE A2...
Page 177: ...177 1 2 3 4 5 6 7 8 8 1 9 10 11 12 A1 A2 B1 B2 C 1 2 D 1 12 2 EN 60204...
Page 178: ...178 30 435 PSI 5 8 85 PSI PWW PS 12...
Page 182: ...182 4 7 3...
Page 183: ...183 3 b PWW 3 4 PWW 9000 12000 1 PWW 18000 24000 3 4 PWW 9000 12000 1 PWW 18000 24000 4...
Page 187: ...187 60 90 m PFANNENBERG 18 15 ISO 4406 10 40 C 45 C 50 C 15 C PFANNENBERG 0 C 11 A1 A2 PWW A2...
Page 189: ...189 11 12 13 14...
Page 190: ...190 l R S T 15 16 17...
Page 191: ...191 5 R S T 18 19 20 21...
Page 192: ...192 PFANNENBERG...
Page 193: ...193 12 KLIXON 2 1 Klixon...
Page 194: ...194 40 C...
Page 195: ...195...
Page 196: ...196 A1...
Page 198: ...198 A2...
Page 200: ...200 B1 n 842 2006 2 PWW 22 23...
Page 201: ...201 A2 20 30 5 7 11 24 25...
Page 202: ...202 24 36 25 309 1 2004...
Page 203: ...203 B2 EB EB150 T EB190 WT...
Page 204: ...204...
Page 205: ...205 C 1 Pfannenberg PFANNENBERG 1 2 3 26 2 1 0...
Page 210: ...210 2 PWW INLET 2 1 31 PWW Air purge valve Max safety valve Refill valve...
Page 211: ...211 D 1 1 1 90 m pH 1 2 3 4 32...