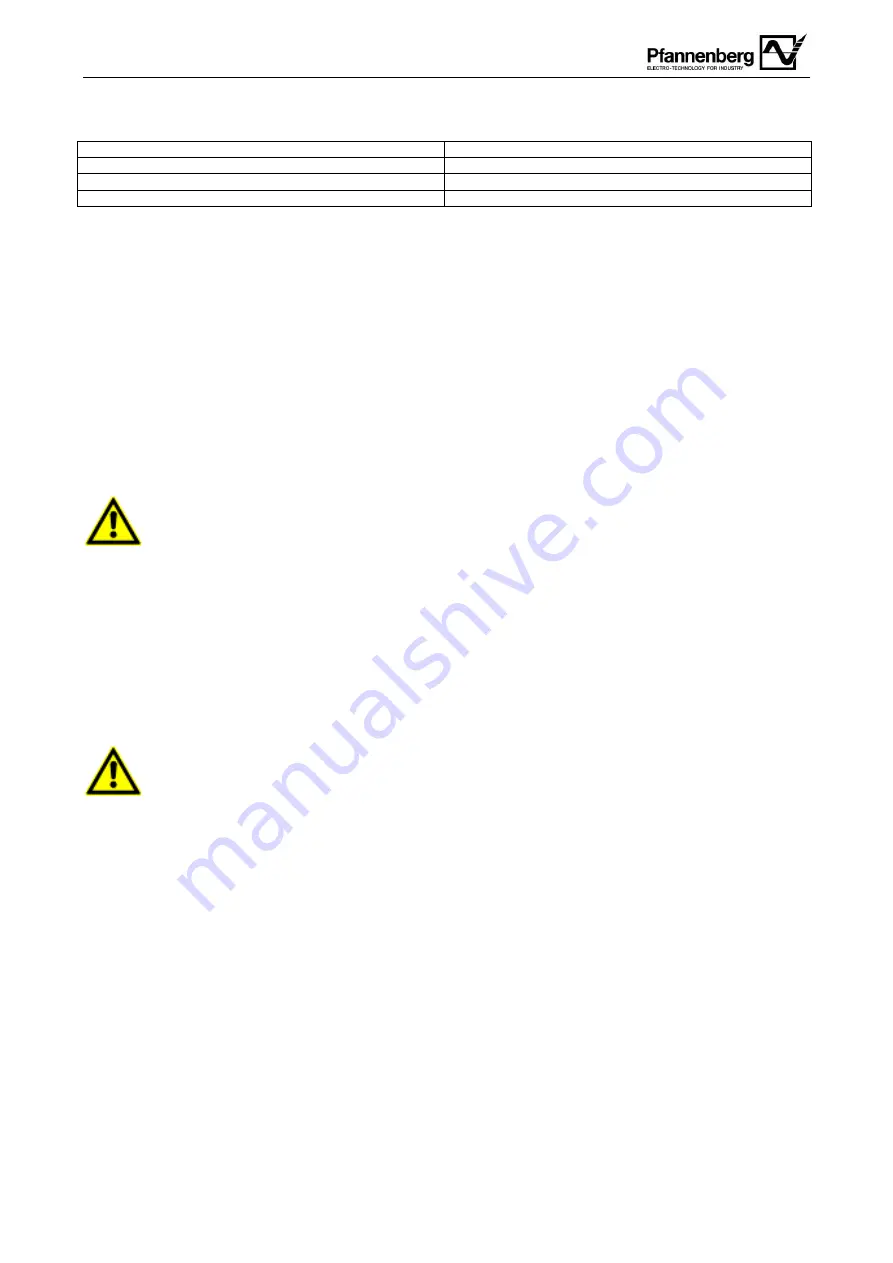
Deutsch
66
Abbildung 30 - Schema Wiederherstellung des Hydraulikkreislaufs des Rückkühlers
From customer cooling circuit
Vom Kühlkreislauf des Kunden
Cooling fluid tank
Tank der Kühlflüssigkeit
Refill pump
Füllpumpe
To customer cooling circuit
Zum Kühlkreislauf des Kunden
Phase 6:
Den Anschluss an das Stromnetz des Kunden und des Alarmkabels mit der Ausrüstung des Kunden ausführen
(siehe Schaltplan für weitere Details).
Phase 7:
Zum Entlüften der Pumpe des Rückkühlers die Entlüftungsschraube am Pumpenoberteil lockern (wenn
vorhanden). Berücksichtigen, dass die Pumpe korrekt entlüftet ist, wenn nur Wasser austritt.
Zur Beachtung:
Die Entlüftungsschraube muss besonders aufmerksam gelockert werden (nur 1 oder 2 Umdrehungen),
damit die Dichtung nicht austritt.
Phase 8:
Den Hauptschalter und den Trennschalter der Pumpe des Rückkühlers
auf „ON“ stellen (alle anderen
Trennschalter müssen auf „OFF“ bleiben).
Sicherstellen, dass sich die Pumpe des Rückkühlers vorschriftsmäßig dreht.
Zur Beachtung:
Auf der Rückseite der
Pumpe zeigt ein Pfeil die Drehrichtung an. Bei falscher Drehrichtung zwei der Phasen R-S-T auf dem Klemmenbrett
umkehren.
ACHTUNG!
Die Pumpe darf nicht trocken oder mit umgekehrter Drehrichtung funktionieren. Daher muss
die Kontrolle der vorschriftsmäßigen Drehrichtung schnell erfolgen.
Phase 9:
Die Pumpe des Rückkühlers mindestens 20 Minuten laufen lassen, damit die im Hydraulikkreislauf enthaltene
Restluft abgelassen wird.
Die Pumpe des Rückkühlers anhalten und den Vorfülldruck prüfen.
Gegebenenfalls erneut befüllen.
Phase 10:
Alle Trennschalter auf „ON“ stellen.
Jetzt ist der Rückkühler für den regulären Betrieb bereit.
ACHTUNG!
Wenn der Rückkühler in niedriger Position installiert werden muss (das Entlüftungsventil 3
würde sich in diesem Fall nicht am höchsten Punkt des Hydraulikkreislaufs befinden), könnten zusätzliche
Entlüftungsventile am externen Hydraulikkreislauf erforderlich sein.
Zur Beachtung:
Die Rückkühler mit
GESCHLOSSENEM KREISLAUF
sind mit einem Sicherheitsablassventil ausgestattet (Teil
2 auf obenstehender
Abbildung 26
), das auf
4
bar (87 PSI) eingestellt ist.
Der auf dem Kennschild des Rückkühlers angegebene höchste hydraulische Betriebsdruck (PS) versteht sich
zuzüglich des Vorfülldrucks.
Regelmäßig den Vorfülldruck im Hydraulikkreislauf prüfen und gegebenenfalls Flüssigkeit nachfüllen.
Summary of Contents for EB 130 WT
Page 20: ...English 20 APPENDIX A1...
Page 21: ...English 21 APPENDIX A2...
Page 26: ...English 26 Max pressure valve Thermostatic Valve Evaporator Refrigerant pipes Fan Pump...
Page 54: ...Deutsch 54 ANLAGE A1...
Page 56: ...Deutsch 56 ANLAGE A2...
Page 62: ...Deutsch 62 H chstdruckventil Thermostatisches Ventil Verdampfer K hlmittelrohre L fter Pumpe...
Page 89: ...Italiano 89 ALLEGATO A1...
Page 91: ...Italiano 91 ALLEGATO A2...
Page 124: ...Espa ol 124 ANEXO A1...
Page 126: ...Espa ol 126 ANEXO A2...
Page 159: ...Fran ais 159 ANNEXE A1...
Page 161: ...Fran ais 161 ANNEXE A2...
Page 177: ...177 1 2 3 4 5 6 7 8 8 1 9 10 11 12 A1 A2 B1 B2 C 1 2 D 1 12 2 EN 60204...
Page 178: ...178 30 435 PSI 5 8 85 PSI PWW PS 12...
Page 182: ...182 4 7 3...
Page 183: ...183 3 b PWW 3 4 PWW 9000 12000 1 PWW 18000 24000 3 4 PWW 9000 12000 1 PWW 18000 24000 4...
Page 187: ...187 60 90 m PFANNENBERG 18 15 ISO 4406 10 40 C 45 C 50 C 15 C PFANNENBERG 0 C 11 A1 A2 PWW A2...
Page 189: ...189 11 12 13 14...
Page 190: ...190 l R S T 15 16 17...
Page 191: ...191 5 R S T 18 19 20 21...
Page 192: ...192 PFANNENBERG...
Page 193: ...193 12 KLIXON 2 1 Klixon...
Page 194: ...194 40 C...
Page 195: ...195...
Page 196: ...196 A1...
Page 198: ...198 A2...
Page 200: ...200 B1 n 842 2006 2 PWW 22 23...
Page 201: ...201 A2 20 30 5 7 11 24 25...
Page 202: ...202 24 36 25 309 1 2004...
Page 203: ...203 B2 EB EB150 T EB190 WT...
Page 204: ...204...
Page 205: ...205 C 1 Pfannenberg PFANNENBERG 1 2 3 26 2 1 0...
Page 210: ...210 2 PWW INLET 2 1 31 PWW Air purge valve Max safety valve Refill valve...
Page 211: ...211 D 1 1 1 90 m pH 1 2 3 4 32...