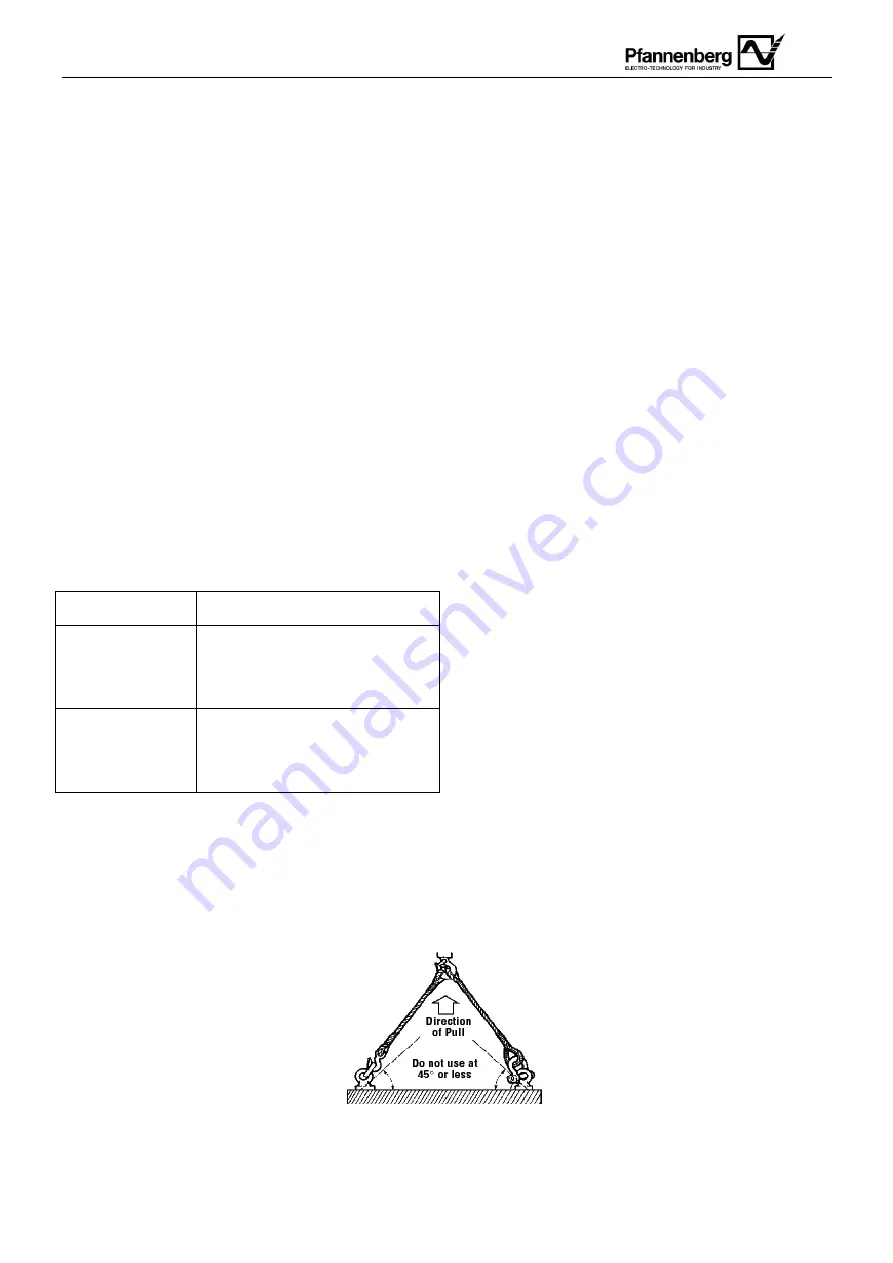
English
6
3. Residual risks
There are some residual risks after the installation of the unit that have to be considered:
Residual risks according to 2006/42/CE Directive:
The condenser has fins on his external surface, so there is the possibility for the operator to touch sharp edges
during service of the unit.
Although the unit is designed with all the possible safety requirements, in case of external fire there is the
possibility that the internal pressure and temperature of the unit will increase in a dangerous and uncontrollable
way; in that case use the extinguishing tools suitable for that conditions.
Residual risks according to 97/23/CE Directive:
Although the unit is designed with all the possible safety requirements, in case of external fire there is the
possibility that the internal pressure and temperature of the unit will increase in a dangerous and uncontrollable
way; in that case use the extinguishing tools suitable for that conditions.
For the series production of the standard units of category
, the pressure resistance test (typically the
hydrostatic pressure test) is made on a statistic base, not on all units.
This can be accepted, also considering all the safety devices mounted on the units.
4. Receiving and Unpacking
Each unit is packed in a carton box.
It is recommended to pay particular attention during handling and transportation of the unit and to maintain the packaged uni ts
in the vertical position, in order to avoid any kind of dents to the external frame and any damage to the internal components.
Secure units to the transport vehicle with suitable strapping.
Note!
The above mentioned packages are not suitable for piling up units on top of each other
Store the Chiller in a dry place, away from heat sources. All waste materials should be recycled in the appropriate manner.
For the operations of lifting and movement it is necessary to use a fork lift truck with proper load capacity and with forks longer
than the base of the Chiller. Avoid sudden movements which can damage the framework and the internal components.
PFANNENBERG Std Chiller (above 45Kg weight) are also provided with 4 eye bolts for lifting and transportation; to be used for
vertical loading/unloading only (to see the right point for lifting please refer to the stickers on the unit).
Check after the final positioning of the Chiller the internal connections to avoid damage during operation.
EB Models
Packaging solution
EB 30 – 43 – 60 WT
EB 75 – 90 WT
EB 130 – 150 WT
Chiller supplied on a wooden
pallet and protected by
a cardboard box
EB 190 – 250 WT
EB 300 – 350 – 400 WT
Chiller supplied on a wooden
pallet and wrapped
with protective film
Picture 1
– Chiller lifting
Summary of Contents for EB 130 WT
Page 20: ...English 20 APPENDIX A1...
Page 21: ...English 21 APPENDIX A2...
Page 26: ...English 26 Max pressure valve Thermostatic Valve Evaporator Refrigerant pipes Fan Pump...
Page 54: ...Deutsch 54 ANLAGE A1...
Page 56: ...Deutsch 56 ANLAGE A2...
Page 62: ...Deutsch 62 H chstdruckventil Thermostatisches Ventil Verdampfer K hlmittelrohre L fter Pumpe...
Page 89: ...Italiano 89 ALLEGATO A1...
Page 91: ...Italiano 91 ALLEGATO A2...
Page 124: ...Espa ol 124 ANEXO A1...
Page 126: ...Espa ol 126 ANEXO A2...
Page 159: ...Fran ais 159 ANNEXE A1...
Page 161: ...Fran ais 161 ANNEXE A2...
Page 177: ...177 1 2 3 4 5 6 7 8 8 1 9 10 11 12 A1 A2 B1 B2 C 1 2 D 1 12 2 EN 60204...
Page 178: ...178 30 435 PSI 5 8 85 PSI PWW PS 12...
Page 182: ...182 4 7 3...
Page 183: ...183 3 b PWW 3 4 PWW 9000 12000 1 PWW 18000 24000 3 4 PWW 9000 12000 1 PWW 18000 24000 4...
Page 187: ...187 60 90 m PFANNENBERG 18 15 ISO 4406 10 40 C 45 C 50 C 15 C PFANNENBERG 0 C 11 A1 A2 PWW A2...
Page 189: ...189 11 12 13 14...
Page 190: ...190 l R S T 15 16 17...
Page 191: ...191 5 R S T 18 19 20 21...
Page 192: ...192 PFANNENBERG...
Page 193: ...193 12 KLIXON 2 1 Klixon...
Page 194: ...194 40 C...
Page 195: ...195...
Page 196: ...196 A1...
Page 198: ...198 A2...
Page 200: ...200 B1 n 842 2006 2 PWW 22 23...
Page 201: ...201 A2 20 30 5 7 11 24 25...
Page 202: ...202 24 36 25 309 1 2004...
Page 203: ...203 B2 EB EB150 T EB190 WT...
Page 204: ...204...
Page 205: ...205 C 1 Pfannenberg PFANNENBERG 1 2 3 26 2 1 0...
Page 210: ...210 2 PWW INLET 2 1 31 PWW Air purge valve Max safety valve Refill valve...
Page 211: ...211 D 1 1 1 90 m pH 1 2 3 4 32...