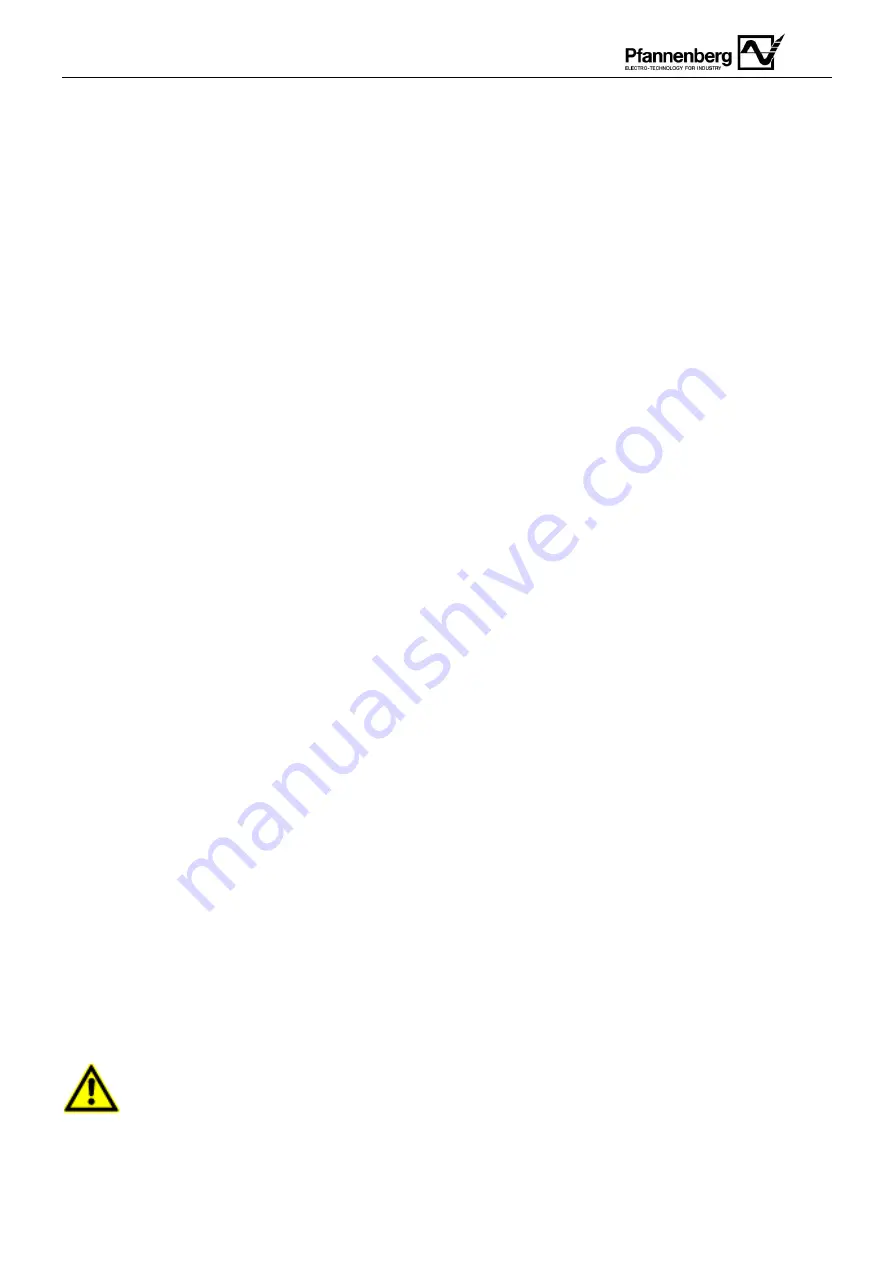
English
5
*NOTE:
for environmental reasons never discharge refrigerant into atmosphere (follow local regulations to properly dispose of
refrigerant).
It is recommended to familiarize with all technical documentation provided with the unit (such as Mechanical & Electrical
Diagrams) in order to avoid improper operation of this unit.
It is also
mandatory
to comply with
Regulation (EC) No 842/2006
of the European Parliament and of the Council of 17 May
2006 on certain fluorinated greenhouse gases.
The above mentioned Regulation lays down specific measures and restrictions to be considered while commissioning,
operating, maintaining and disposing any equipment containing greenhouse gases, such as HFCs, as specified in Annex I.
The Regulation (EC) No 842/2006 also (but not only) specifies mandatory leakage-check frequency to be performed by certified
personnel and mandatory records providing the evidence of exact fluorinated gas charge and subsequent added and/or
recovered quantities as described in Article 3 (reported below):
Article 3
Containment
Operators of the following stationary applications: refrigeration, air conditioning and heat pump equipment, including their
circuits, as well as fire protection systems, which contain fluorinated greenhouse gases listed in Annex I, shall, using all
measures which are technically feasible and do not entail disproportionate cost:
(a) prevent leakage of these gases; and
(b) as soon as possible repair any detected leakage.
Operators of the applications referred to in paragraph 1 shall ensure that they are checked for leakage by certified personnel
who comply with the requirements of Article 5, according to the following schedule:
(a) applications containing
3 kg or more
of fluorinated greenhouse gases shall be checked for leakage at least once
every 12
months
; this shall not apply to equipment with hermetically sealed systems, which are labeled as such and contain less than 6
kg of fluorinated greenhouse gases;
(b) applications containing
30 kg or more
of fluorinated greenhouse gases shall be checked for leakage at least once
every six
months
;
(c) applications containing
300 kg or more
of fluorinated greenhouse gases shall be checked for leakage at least once
every
three months
.
The applications shall be checked for leakage
within one month after a leak has been repaired
to ensure that the repair has
been effective.
For the purposes of this paragraph, ‘checked for leakage’ means that the equipment or system is examined for leakage using
direct or indirect measuring methods, focusing on those parts of the equipment or system most likely to leak. The direct and
indirect measuring methods of checking for leakage shall be specified in the standard checking requirements referred to in
paragraph 7.
Operators of the applications referred to in paragraph 1, containing 300 kg or more of fluorinated greenhouse gases, shall install
leakage detection systems. These leakage detection systems shall be checked at least once every 12 months to ensure their
proper functioning. In the case of such fire protection systems installed before 4 July 2007, leakage detection systems shall be
fitted by 4 July 2010.
Where a properly functioning appropriate leakage detection system is in place, the frequency of the checks required under
paragraph 2(b) and (c) shall be halved.
In the case of fire protection systems where there is an existing inspection regime in place to meet ISO 14520 standard, these
inspections may also fulfill the obligations of this Regulation as long as those inspections are at least as frequent.
Operators of the applications referred to in paragraph 1, containing
3 kg or more
of fluorinated greenhouse gases, shall
maintain records
on the quantity and type of fluorinated greenhouse gases installed, any quantities added and the quantity
recovered during servicing, maintenance and final disposal. They shall also maintain records of other relevant information
including the identification of the company or technician who performed the servicing or maintenance, as well as the dates and
results of the checks carried out under paragraphs 2, 3 and 4 and relevant information specifically identifying the separate
stationary equipment of applications referred to in paragraph 2(b) and (c). These records shall be made available on request to
the competent authority and to the Commission.
Regulation (EC) No 842/2006
also include: ‘
Scope
’ – Article 1; ‘
Definitions
’ – Article 2; ‘
Recovery
’ – Article 4; ‘
Training and
Certification
’ – Article 5; ‘
Reporting
’ – Article 6; ‘
Labelling
’ – Article 7; ‘
Control of Use
’ – Article 8; ‘
Placing on the Market
’ –
Article 9; ‘
Review
’ – Article 10; Article 11; ‘
Committee
’ – Article 12; ‘
Penalties
’ – Article 13; Article 14; ‘
Entry into force
’.
CAUTION:
in accordance to the F-GAS regulation DRP43/2012, every year the operator (the owner of
the equipment) is responsible to ensure a Gas leakage test, the recording of the gas quantity change inside the unit
and the communication to the responsible agency of the state in the European community where the unit is in
operation.
Please ask Pfannenberg service in case support is needed
Summary of Contents for EB 130 WT
Page 20: ...English 20 APPENDIX A1...
Page 21: ...English 21 APPENDIX A2...
Page 26: ...English 26 Max pressure valve Thermostatic Valve Evaporator Refrigerant pipes Fan Pump...
Page 54: ...Deutsch 54 ANLAGE A1...
Page 56: ...Deutsch 56 ANLAGE A2...
Page 62: ...Deutsch 62 H chstdruckventil Thermostatisches Ventil Verdampfer K hlmittelrohre L fter Pumpe...
Page 89: ...Italiano 89 ALLEGATO A1...
Page 91: ...Italiano 91 ALLEGATO A2...
Page 124: ...Espa ol 124 ANEXO A1...
Page 126: ...Espa ol 126 ANEXO A2...
Page 159: ...Fran ais 159 ANNEXE A1...
Page 161: ...Fran ais 161 ANNEXE A2...
Page 177: ...177 1 2 3 4 5 6 7 8 8 1 9 10 11 12 A1 A2 B1 B2 C 1 2 D 1 12 2 EN 60204...
Page 178: ...178 30 435 PSI 5 8 85 PSI PWW PS 12...
Page 182: ...182 4 7 3...
Page 183: ...183 3 b PWW 3 4 PWW 9000 12000 1 PWW 18000 24000 3 4 PWW 9000 12000 1 PWW 18000 24000 4...
Page 187: ...187 60 90 m PFANNENBERG 18 15 ISO 4406 10 40 C 45 C 50 C 15 C PFANNENBERG 0 C 11 A1 A2 PWW A2...
Page 189: ...189 11 12 13 14...
Page 190: ...190 l R S T 15 16 17...
Page 191: ...191 5 R S T 18 19 20 21...
Page 192: ...192 PFANNENBERG...
Page 193: ...193 12 KLIXON 2 1 Klixon...
Page 194: ...194 40 C...
Page 195: ...195...
Page 196: ...196 A1...
Page 198: ...198 A2...
Page 200: ...200 B1 n 842 2006 2 PWW 22 23...
Page 201: ...201 A2 20 30 5 7 11 24 25...
Page 202: ...202 24 36 25 309 1 2004...
Page 203: ...203 B2 EB EB150 T EB190 WT...
Page 204: ...204...
Page 205: ...205 C 1 Pfannenberg PFANNENBERG 1 2 3 26 2 1 0...
Page 210: ...210 2 PWW INLET 2 1 31 PWW Air purge valve Max safety valve Refill valve...
Page 211: ...211 D 1 1 1 90 m pH 1 2 3 4 32...