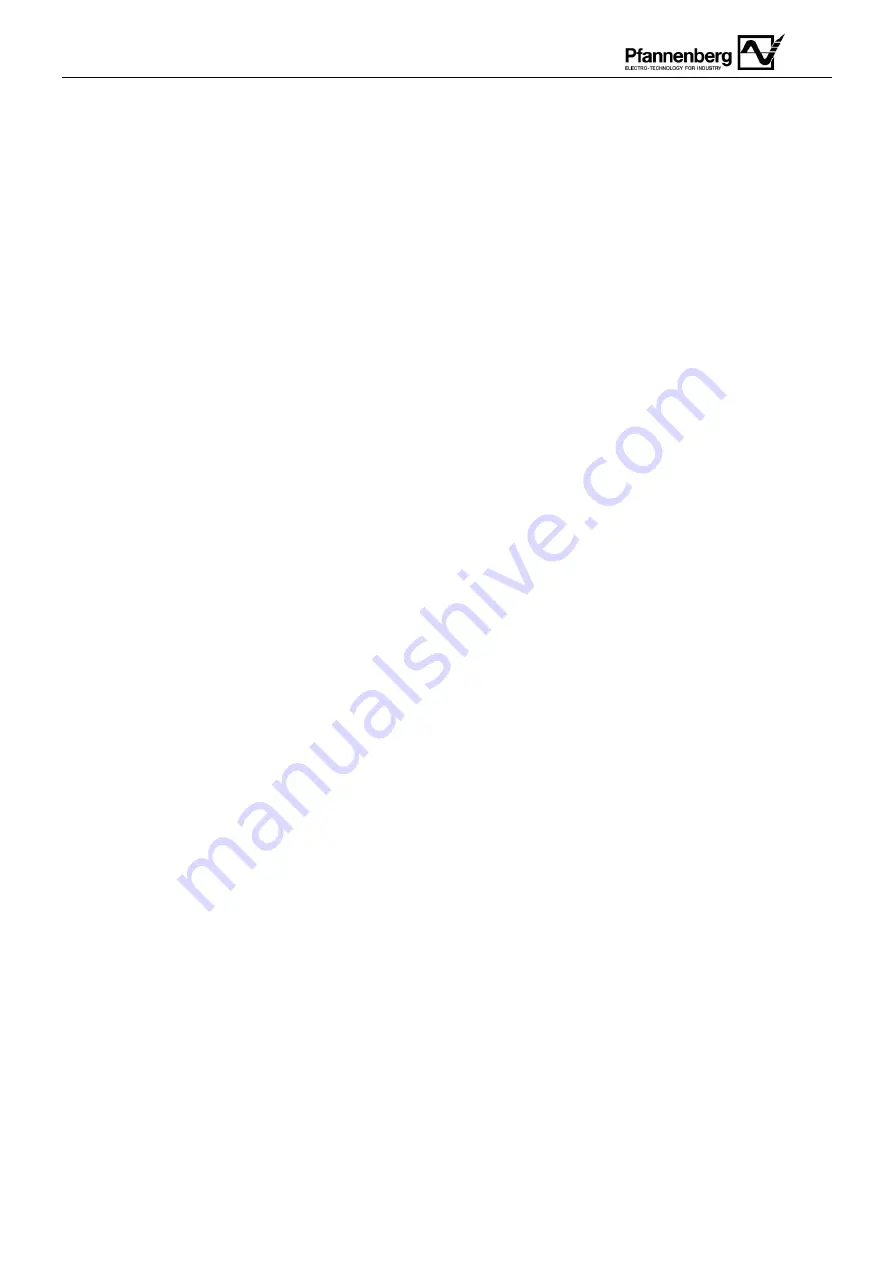
English
3
Index
1.
Warranty
2.
Safety
3.
Residual risks
4.
Receiving and Unpacking
5.
Positioning the Chiller
6.
Foundation
7.
Connections
8.
Process Water / Fluids
8.1
Waterquality
9.
Process Oil / Fluids
10.
Ambient temperature
11.
Start up of the chiller
Debug Table
APPENDIX A1
APPENDIX A2
APPENDIX B1
APPENDIX B2
APPENDIX C
1
Close Loop Chiller Start-up
2
Water - water Chiller Start-up
1. Warranty
This warranty covers the material design and quality during the first 12 months starting from the delivery date. Within this
defined period our Company will either repair, or replace (with ex works delivery) all parts which on the sole opinion of the
supplier, have caused quality problems which are not a result of poor maintenance, inexperience of the operators, faulty
installation or failures which are caused because this instruction was not followed. This warranty does not include the expenses,
travel hours and travel allowance related to our technicians in case their presence is required at the customer's factory. Th ese
expenses will be totally invoiced as working hours. The customer shall not have the right to claim any refund from our Company
for the time during which the machine shall remain inactive, related to repairs. No refund will be acknowledged for expenses,
damages, either direct or indirect, which are a result of the above.
Separate agreements with customers have to be agreed in written form may vary from this paragraph.
2. Safety
The Chiller
instructions must be read by the installer and personnel in charge for operation, before starting the chiller.
All safety and security instructions given in this manual have to be observed!
Only qualified personnel are allowed to install, operate and do the maintenance work.
Non observance of the instructions may cause injuries and will cancel the manufacturers liability for subsequent damage.
National regulations on accident prevention, regulations of the local power supply authorities as well as any specific safety
instructions for chiller must be observed.
The safety of the unit is only guaranteed, if it is used as intended.
The following points must be observed before commissioning and while operating the Chiller:
Familiarize yourself with all operating controls.
Make sure that all working limits indicated within unit label are observed.
Use protective devices to check electrical insulation. Do not carry out any work on any part of the equipment that might
be live with wet clothing, hands and feet.
Never spill or pour any cooling medium into the environment as this may cause health hazard.
The components of the Chiller must not be modified in any way.
Disconnect the power supply and release pressure from any pressurized component before carrying out any service
work on the Chiller.
A qualified commissioning engineer must ensure that the Chiller has been connected to the electrical mains in
accordance with the standard EN 60204 and all other applicable national regulations.
Summary of Contents for EB 130 WT
Page 20: ...English 20 APPENDIX A1...
Page 21: ...English 21 APPENDIX A2...
Page 26: ...English 26 Max pressure valve Thermostatic Valve Evaporator Refrigerant pipes Fan Pump...
Page 54: ...Deutsch 54 ANLAGE A1...
Page 56: ...Deutsch 56 ANLAGE A2...
Page 62: ...Deutsch 62 H chstdruckventil Thermostatisches Ventil Verdampfer K hlmittelrohre L fter Pumpe...
Page 89: ...Italiano 89 ALLEGATO A1...
Page 91: ...Italiano 91 ALLEGATO A2...
Page 124: ...Espa ol 124 ANEXO A1...
Page 126: ...Espa ol 126 ANEXO A2...
Page 159: ...Fran ais 159 ANNEXE A1...
Page 161: ...Fran ais 161 ANNEXE A2...
Page 177: ...177 1 2 3 4 5 6 7 8 8 1 9 10 11 12 A1 A2 B1 B2 C 1 2 D 1 12 2 EN 60204...
Page 178: ...178 30 435 PSI 5 8 85 PSI PWW PS 12...
Page 182: ...182 4 7 3...
Page 183: ...183 3 b PWW 3 4 PWW 9000 12000 1 PWW 18000 24000 3 4 PWW 9000 12000 1 PWW 18000 24000 4...
Page 187: ...187 60 90 m PFANNENBERG 18 15 ISO 4406 10 40 C 45 C 50 C 15 C PFANNENBERG 0 C 11 A1 A2 PWW A2...
Page 189: ...189 11 12 13 14...
Page 190: ...190 l R S T 15 16 17...
Page 191: ...191 5 R S T 18 19 20 21...
Page 192: ...192 PFANNENBERG...
Page 193: ...193 12 KLIXON 2 1 Klixon...
Page 194: ...194 40 C...
Page 195: ...195...
Page 196: ...196 A1...
Page 198: ...198 A2...
Page 200: ...200 B1 n 842 2006 2 PWW 22 23...
Page 201: ...201 A2 20 30 5 7 11 24 25...
Page 202: ...202 24 36 25 309 1 2004...
Page 203: ...203 B2 EB EB150 T EB190 WT...
Page 204: ...204...
Page 205: ...205 C 1 Pfannenberg PFANNENBERG 1 2 3 26 2 1 0...
Page 210: ...210 2 PWW INLET 2 1 31 PWW Air purge valve Max safety valve Refill valve...
Page 211: ...211 D 1 1 1 90 m pH 1 2 3 4 32...