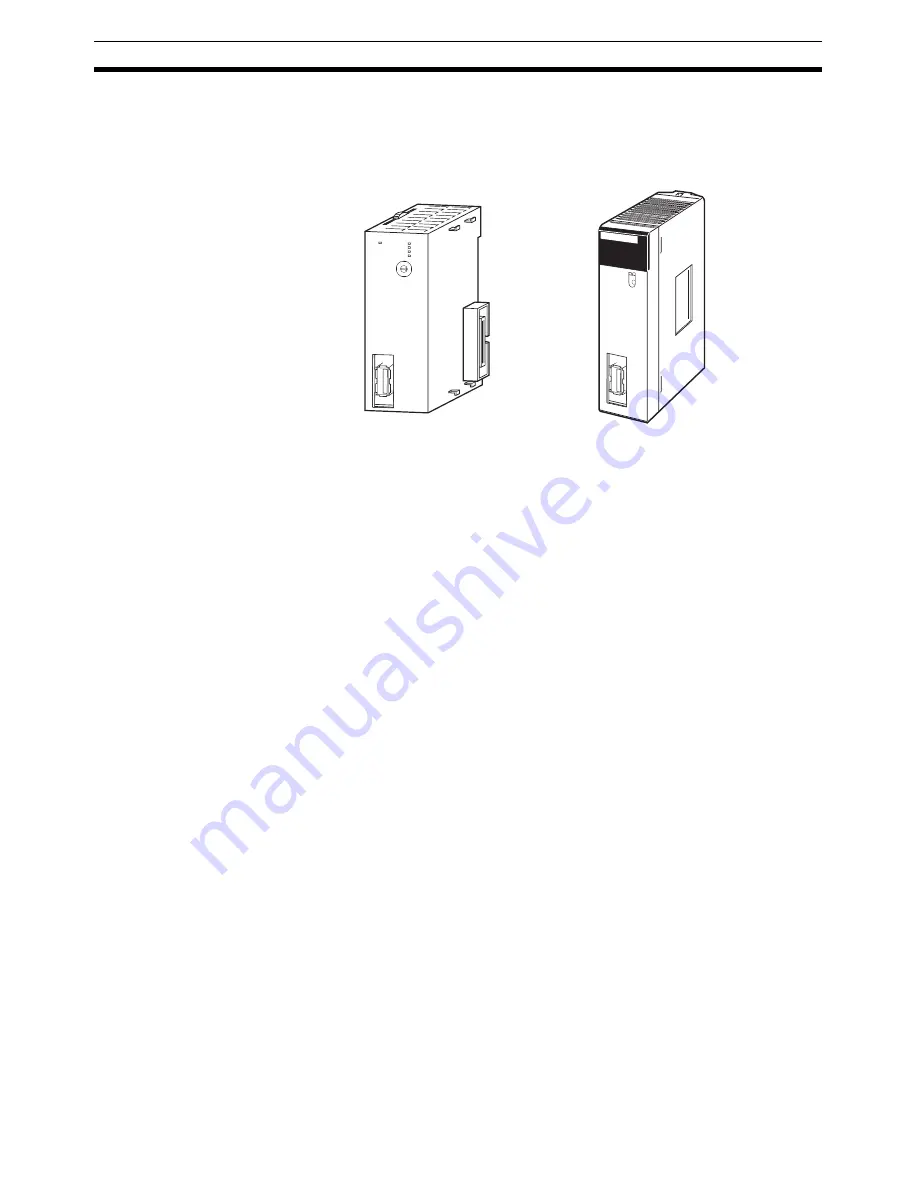
2
Features
Section 1-1
1-1
Features
The Position Control Unit is a CS/CJ-series CPU Bus Unit. The Position Con-
trol Unit (PCU) receives commands from the CPU Unit's internal Auxiliary
Area and outputs positioning commands to MECHATROLINK-II Servo Drives.
MECHATROLINK is a registered trademark of MECHATROLINK Members
Association.
Compatible with the
MECHATROLINK-II High-
speed Field Network
A MECHATROLINK-II high-speed (10 Mbps) communications interface is
used to control Servo Drives for up to 16 axes with a single CS/CJ-series Unit.
Shielded twisted-pair cables in daisy-chain formation make wiring simple and
enable multi-axis systems that require less wiring and are smaller in size.
High-speed, High-
precision Control Using
Data Communications
Optimal motor performance can be achieved by transmitting data using com-
munications between the Programmable Controller (PLC) and Servo Drives,
without having to set an upper limit for the designated speed. High-speed and
high-precision position control using high-resolution motors are possible.
Position Control (Direct
Operation)
Positioning can be performed simply by directly setting the target position and
target speed from the CPU Unit. Positioning to either absolute or relative posi-
tions is also possible. Interrupt feeding is also supported. With interrupt feed-
ing, positioning is continued for a specified amount after an interrupt input
signal is received, and then the axis is stopped.
Speed Control and Torque
Control
The Servo Drive's speed and torque can be controlled by directly specifying
the target speed and torque from the CPU Unit.
Compatible with
Servomotors with
Absolute Encoders
The PCU is compatible with Servomotors that have absolute encoders. Using
such Servomotors eliminates the need to repeatedly perform origin searches.
Transfer Data between
Host PLC and Servo Drive
The Servo Drive's parameters and monitors can be set from the CPU Unit. All
the data for the multi-axis system can be centrally controlled from the host
PLC. This removes the difficulty in starting up devices or setting data when
replacing a Unit.
CJ1W-NC271/471/F71
CS1W-NC271/471/F71
RUN
ERC
ERH
ERM
MLK
NCF71
UNIT
No.
MLK
01
234
567
89
AB
CDEF
Position Control Unit
RUN
ERC
ERH
ERM
MLK
NCF71
CS
UNIT
No.
98
543
21
0
MLK
Summary of Contents for CJ1W-MA - REV 10-2008
Page 3: ...iv ...
Page 5: ...vi ...
Page 21: ...xxii ...
Page 57: ...30 Starting Operation Section 2 2 ...
Page 97: ...70 Wiring Section 3 4 ...
Page 247: ...220 Transferring Servo Parameters Section 5 3 ...
Page 281: ...254 Standard Settings for Servo Drives Using MECHATROLINK Section 6 4 ...
Page 343: ...316 Absolute Encoder Origin Section 8 6 ...
Page 375: ...348 Linear Interpolation Section 9 7 ...
Page 423: ...396 DEVIATION COUNTER RESET Section 10 10 ...
Page 631: ...604 Additional Functions for the CJ1W NCF71 MA Appendix F ...
Page 641: ...614 Index ...
Page 643: ...616 Revision History ...