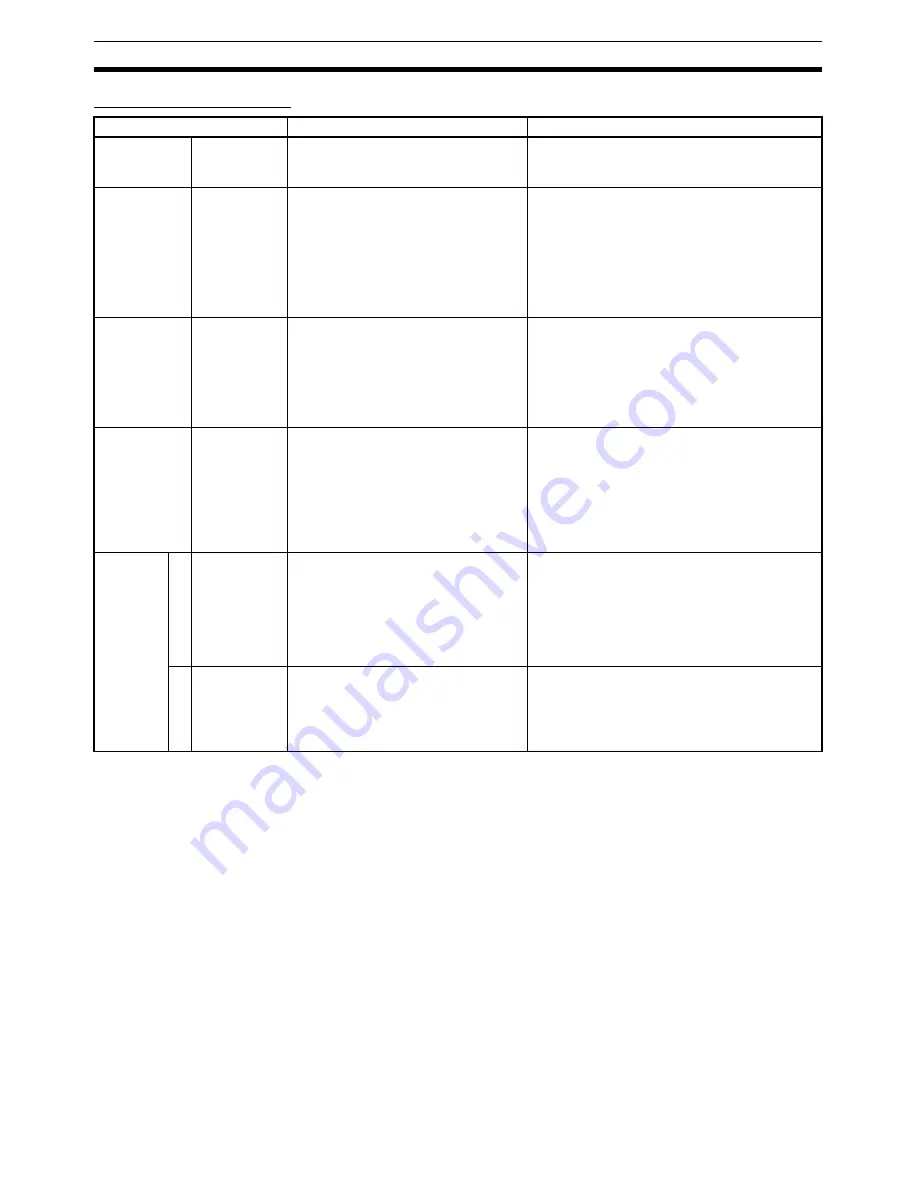
74
Overall Structure
Section 4-1
PCU Setting Procedure
Step
Operation
Result
1
Set unit num-
ber.
Set the unit number on the unit number
setting switch and turn ON the power
to the PCU.
The Common Operating Memory Area starts
from the beginning word obtained using the fol-
lowing equation: n = CIO 1500 + (unit No. × 25)
2
Set common
parameters.
Write the common parameters to the
PCU and save them in the internal
flash memory using the WRITE DATA
and SAVE DATA Bits in the Common
Operating Memory Area.
After saving the common parameters,
restart the PCU or cycle the power to
enable the parameters.
The axes being used (scan list) and MECHA-
TROLINK communications settings are deter-
mined. The Axis Operating Output/Input
Memory Areas for the axes to be used are allo-
cated.
3
Set axis
parameters.
Write the axis parameters to the PCU
and save them in the internal flash
memory using the WRITE DATA and
SAVE DATA Bits in the Common Oper-
ating Memory Area. (These parame-
ters are set at the same time as the
common parameters.)
The settings of the origin search operation and
other parameters for the axes to be used are
determined.
4
Start MECHA-
TROLINK
communica-
tions.
Start MECHATROLINK communica-
tions using the CONNECT Bit in the
Common Operating Memory Area.
When MECHATROLINK communications start,
the axes are operated according to the bits in
the Axis Operating Output Memory Areas and
the status of the axes can be monitored using
the bits in the Axis Operating Input Memory
Areas. Subsequent operations are performed
with MECHATROLINK communications in
progress.
MECHA-
TROLINK
communi-
cations in
progress
5
Set Servo
parameters.
Write the Servo parameters using the
WRITE SERVO PARAMETER Bit and
SAVE SERVO PARAMETER Bit in the
Axis Operating Output Memory Areas.
Read the Servo parameters using the
READ SERVO PARAMETER Bit in the
Axis Operating Input Memory Areas.
The settings for each axis or each Servo Param-
eter are transferred. The transferred online
parameters are enabled when writing is com-
pleted, and transferred offline parameters are
enabled when the Servo Drive power is cycled
or DEVICE SETUP is executed.
6
Operate axes. Start operating axes using the bits in
the Axis Operating Output Memory
Areas.
Monitor the status of axes using the
Axis Operating Input Memory Areas.
Commands are executed and status information
is obtained when the PLC’s I/O is refreshed.
Summary of Contents for CJ1W-MA - REV 10-2008
Page 3: ...iv ...
Page 5: ...vi ...
Page 21: ...xxii ...
Page 57: ...30 Starting Operation Section 2 2 ...
Page 97: ...70 Wiring Section 3 4 ...
Page 247: ...220 Transferring Servo Parameters Section 5 3 ...
Page 281: ...254 Standard Settings for Servo Drives Using MECHATROLINK Section 6 4 ...
Page 343: ...316 Absolute Encoder Origin Section 8 6 ...
Page 375: ...348 Linear Interpolation Section 9 7 ...
Page 423: ...396 DEVIATION COUNTER RESET Section 10 10 ...
Page 631: ...604 Additional Functions for the CJ1W NCF71 MA Appendix F ...
Page 641: ...614 Index ...
Page 643: ...616 Revision History ...