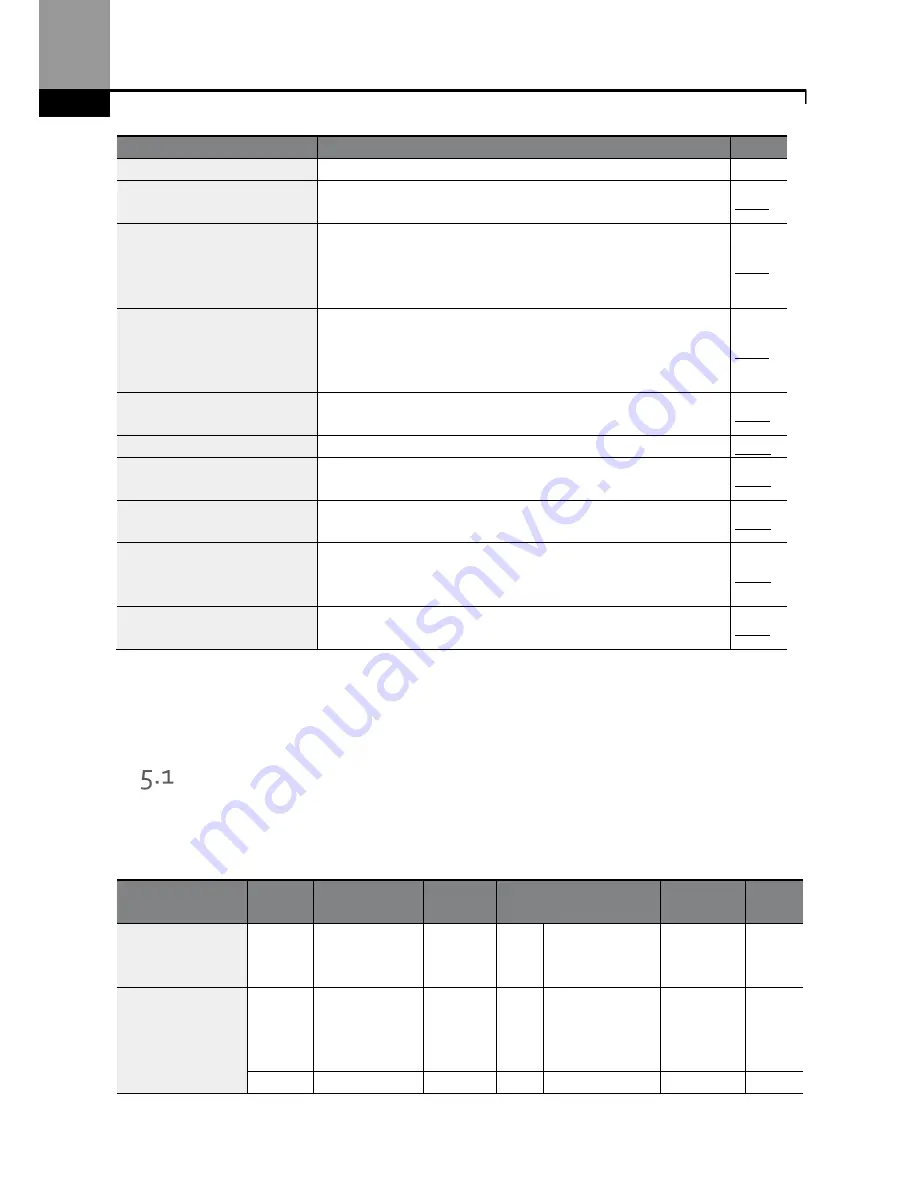
Learning Advanced Features
120
Advanced Tasks
Description
Ref.
motors during low-load and no-load conditions.
Speed search operation
Used to prevent faults when the inverter voltage is output
while the motor is idling or free-running.
p.172
Auto restart operation
Auto restart configuration is used to automatically restart the
inverter when a trip condition is released, after the inverter
stops operating due to activation of protective devices
(faults).
p.176
Second motor operation
Used to switch equipment operation by connecting two
motors to one inverter. Configure and operate the second
motor using the terminal input defined for the second motor
operation.
p.179
Commercial power source
switch operation
Used to switch the power source to the motor from the
inverter output to a commercial power source, or vice versa.
p.181
Cooling fan control
Used to control the cooling fan of the inverter.
p.182
Timer settings
Set the timer value and control the On/Off state of the multi-
function output and relay.
p.190
Brake control
Used to control the On/Off operation of the load’s electronic
braking system.
p.190
Multi-function output
On/Off control
Set standard values and turn On/Off the output relays or
multi-function output terminals according to the analog input
value.
p.192
Regeneration prevention for
press operation.
Used during a press operation to avoid motor regeneration,
by increasing the motor operation speed.
p.193
* Draw operation is an openloop tension control. This feature allows a constant tension to be
applied to the material that is drawn by a motor-driven device, by fine-tuning the motor speed
using operation frequencies that are proportional to a ratio of the main frequency reference.
Operating with Auxiliary References
Frequency references can be configured with various calculated conditions that use the main and
auxiliary frequency references simultaneously. The main frequency reference is used as the
operating frequency, while the auxiliary reference is used to modify and fine-tune the main
reference. The auxiliary reference can also be disabled using a digial input.
Group
Code
Name
LCD
Display
Parameter Setting
Setting
Range
Unit
Operation
Frq
Frequency
reference
source
Freq Ref
Src
0
Keypad-1
0–12
-
bA
03
Auxiliary
frequency
reference
source
Aux Ref
Src
1
V1
0–4
-
04
Auxiliary
Aux Calc 0
M+(G*A)
0–7
-
Содержание Rsi S Series
Страница 2: ......
Страница 6: ......
Страница 12: ...Preparing the Installation 0...
Страница 22: ...Preparing the Installation 10...
Страница 70: ...LearningAdvanced Features 58...
Страница 152: ...LearningAdvanced Features 140 PID controlblock diagram...
Страница 224: ...LearningAdvanced Features 212...
Страница 356: ...344...
Страница 362: ...Maintenance 350...
Страница 381: ...369 TechnicalSpecification...
Страница 397: ......