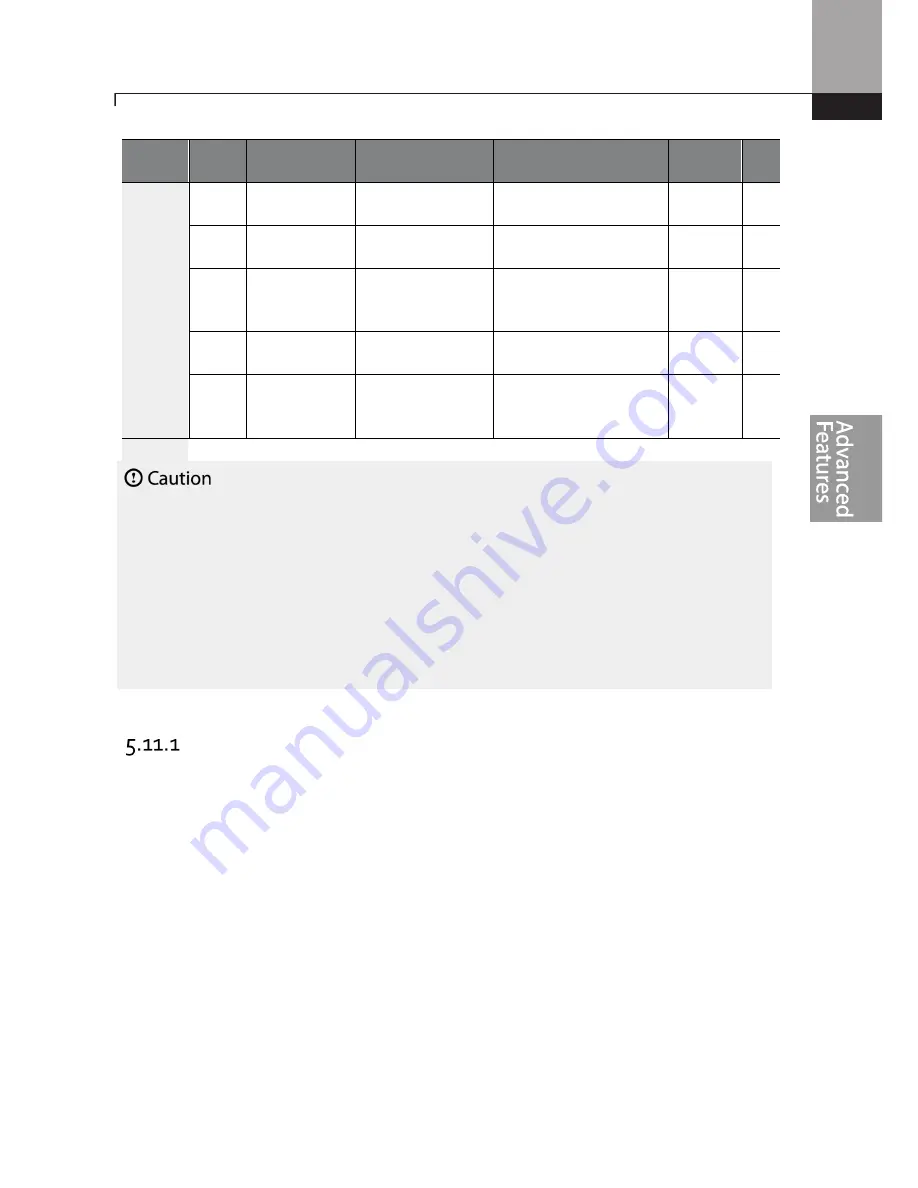
Learning Advanced Features
157
Group
Code
Name
LCD Display
Parameter Setting
Setting
Range
Unit
53
Torque limit
source
Torque Lmt Src
0
Keypad-1
0–
12
54
FWD reverse
torque limit
FWD +Trq Lmt
180.0
0.0–
200.0
%
55
FWD
regenerative
torque limit
FWD -Trq Lmt
180.0
0.0–
200.0
%
56
REV reverse
torque limit
REV +Trq Lmt
180.0
0.0–
200.0
%
57
REV
regenerative
torque limit
REV -Trq Lmt
180.0
0.0–
200.0
%
Enter the motor-related parameters in the Basic function group from the motor name plate. For
high-performance operation, the other parameter values must be estimated. Perform auto tuning
by setting bA. 20 (Auto Tuning) to 7 [All (PM)] to automatically measure the other parameters
before operating a PM synchronous motor in sensorless vector control mode. For high-
performance PM sensorless vector control, the inverter and the motor must have the same
capacity. The inverter control may be inaccurate if the motor capacity and the inverter capacity do
not match. In sensorless vector control mode, do not connect multiple motors to the inverter
output. Note: when you select one of the auto tuning options below and run it, this parameter
value will revert back to “0” when the auto tuning is complete.
Detecting the Initial Pole Position
Initial pole position detection is a process to match the rotor position calculated by the inverter and
the actual rotor position in a motor. In a permanent-magnet (PM) synchronous motor, rotor flux is
generated from the permanent magnet attached to the rotor. Therefore, to run the motor in vector
control mode, the exact rotor position (flux position) must be detected for accurate control of the
torque generated by the motor.
At Cn. 46 (InitAngle Sel), select the type of initial pole position detection.
When Cn. 46 is set to 0 (None), the motor is operated according to the pole position estimated by
the inverter’s internal algorithm, instead of actually detecting the physical position of the rotor
pole.
When Cn. 46 is set to 1 (Angle Detect), the motor is operated according to the pole position
detected by changes in the current. The voltage pulse input is used to detect the pole position and
results in a small amount of noise at motor startup.
When Cn. 46 is set to 2 (Alignment), the inverter forcefully aligns the rotor position by supplying DC
current for a certain period of time.
Содержание Rsi S Series
Страница 2: ......
Страница 6: ......
Страница 12: ...Preparing the Installation 0...
Страница 22: ...Preparing the Installation 10...
Страница 70: ...LearningAdvanced Features 58...
Страница 152: ...LearningAdvanced Features 140 PID controlblock diagram...
Страница 224: ...LearningAdvanced Features 212...
Страница 356: ...344...
Страница 362: ...Maintenance 350...
Страница 381: ...369 TechnicalSpecification...
Страница 397: ......