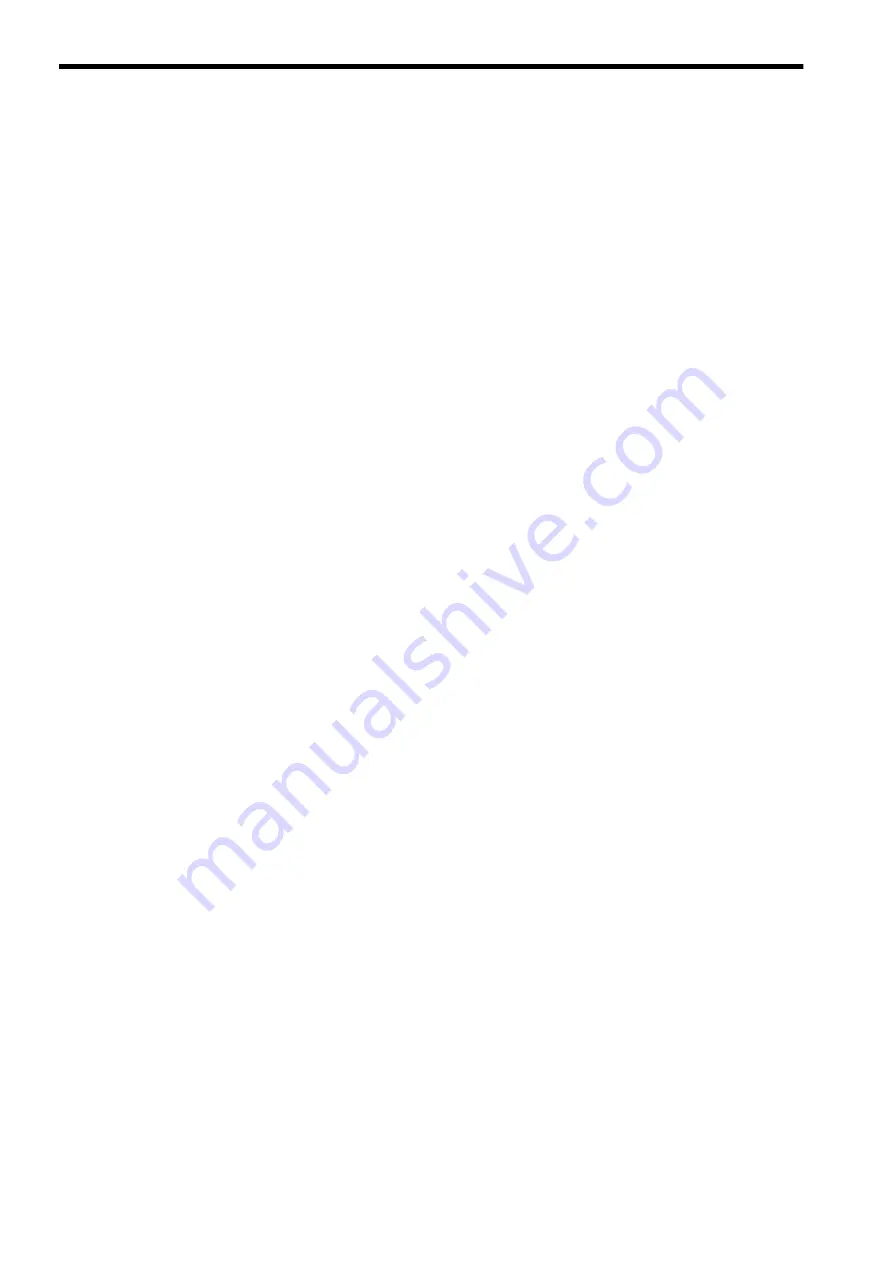
Drive set-up procedure
14.2.7 Speed feedback compensation
14-44
14.2.7 Speed feedback compensation
You can suppress vibration and increase speed loop gain by using speed feedback compen-
sation.
The following explains about parameters for speed feedback compensation.
• MD3046 digit 1 (Pn110 digit 1) SWITCH_ONLINE_AUTO_TUNING (For each axis)
Meaning:
Selects speed feedback compensation function
Setting value: 0 --- Enabled
1 --- Disabled
Note: Pay attention to the polarity of "Enabled" and "Disabled".
• MD3047 (Pn111) SPEED_FEEDBACK_COMP_GAIN (For each axis)
Meaning:
Speed feedback compensation gain
Setting value: [%]
• MD3048 (Pn112) SPEED_FEEDBACK_DELAY_COMP (For each axis)
Meaning:
Speed feedback delay compensation
(Speed feedback compensation inertia gain)
Setting value: [%]
Note: Previous parameter "Speed feedback compensation attenuation fac-
tor" is no longer used.
Adjustment procedures
1. Check an axis to which you want to make an adjustment to disable speed feedback func-
tion (MD3046 digit 1 (Pn110 digit 1) = 1) by watching its torque waveform or others on
the analog monitor, and confirm that the axis vibrates.
2. Assign the following values to the parameters above for the axis you want to make an
adjustment.
• MD3047 = 100
• MD3048 = Setting value of MD3033 (Load inertia ratio) + 100
3. Enable speed feedback function (MD3046 digit 1 (Pn110 digit 1) = 0)
4. Adjust only the 1st-stage torque filter time constant by assigning a large value to
MD3351 (Pn401) as far as no vibration happens at any feed speed. If a vibration hap-
pens, decrease the value.
The maximum value that can be assigned to the MD3351 (Pn401) is calculated from the
speed loop gain MD3030 (Pn100) as follows. Notice that you should assign a smallest
possible value to it.
• MD3351 = 600000/(MD3030
×
2
π
)
5. If no vibration happens in the procedure 4, increase speed loop gain MD3030 (Pn100).
6. If vibration starts while you are increasing MD3030, increase MD3351 paying attention
to the above-mentioned maximum value.
Summary of Contents for CNC Series
Page 1: ...Maintenance Manual Serviceman Handbook MANUAL No NCSIE SP02 19 Yaskawa Siemens CNC Series...
Page 26: ...Part 1 Hardware...
Page 38: ...System Configuration 1 2 3 Spindle motor designations 1 12...
Page 58: ...Installing the control panels 2 3 5 Installing lightning surge absorbers 2 20...
Page 62: ...Installing the motors 3 4...
Page 84: ...Connection method 4 3 2 Setting the rotary switches on the inverters and servo units 4 22...
Page 96: ...Part 2 Software...
Page 102: ...Software configuration 6 6...
Page 113: ...7 2 Network settings 7 11 8 Click on the radio button to the left of Specify an IP address...
Page 121: ...7 2 Network settings 7 19...
Page 122: ...Part 3 PLC...
Page 154: ...Part 4 Setting up and maintenance...
Page 160: ...Overview of System 10 1 2 Basic operation 10 6...
Page 204: ...How to use Digital Operation 12 2 9 Setting the password setting for write prohibit 12 32...
Page 327: ...Error and Troubleshooting 15 4...
Page 328: ...15 1 Errors without Alarm Display and Troubleshooting 15 5...
Page 329: ...Error and Troubleshooting 15 6...
Page 343: ...Maintenance and Check 16 3 3 Setting up Initializing Absolute encoder 16 14...